10 1 Compression Ratio To Psi
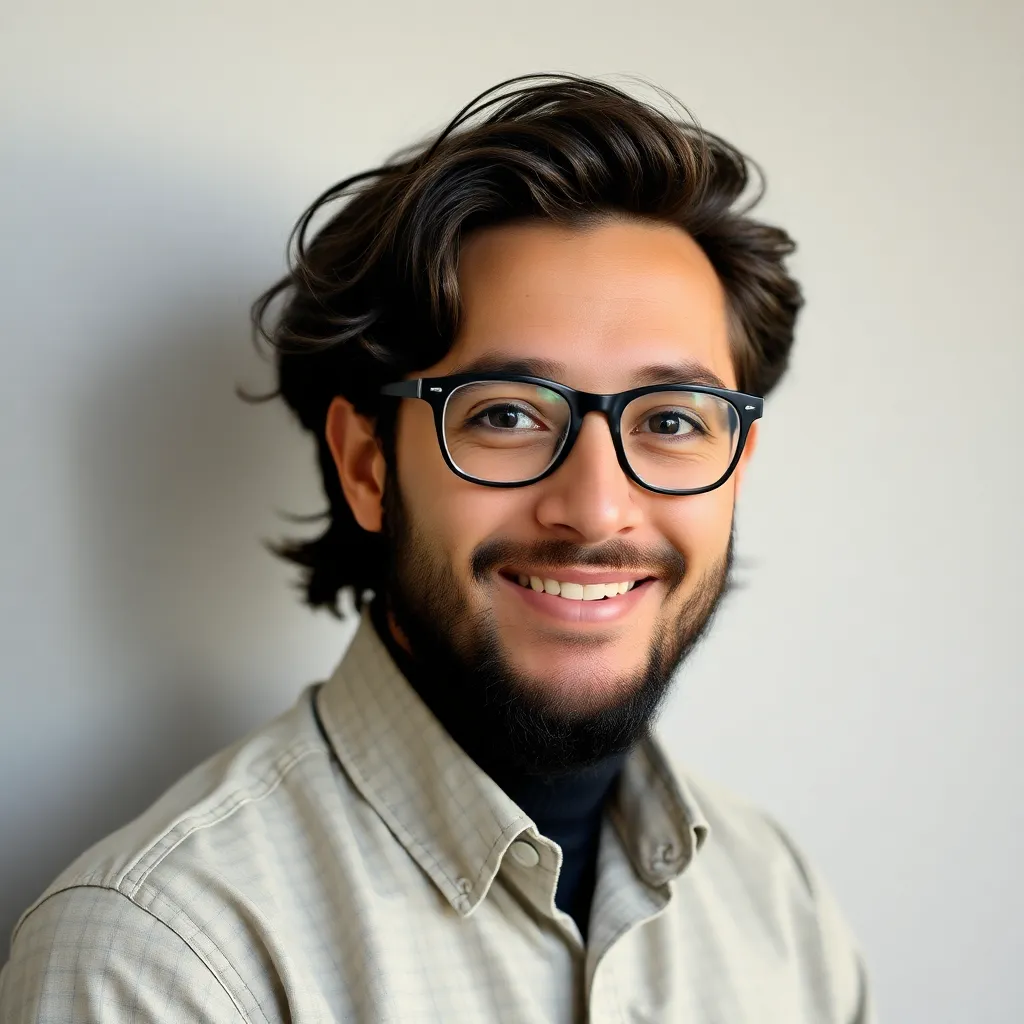
Treneri
May 12, 2025 · 5 min read
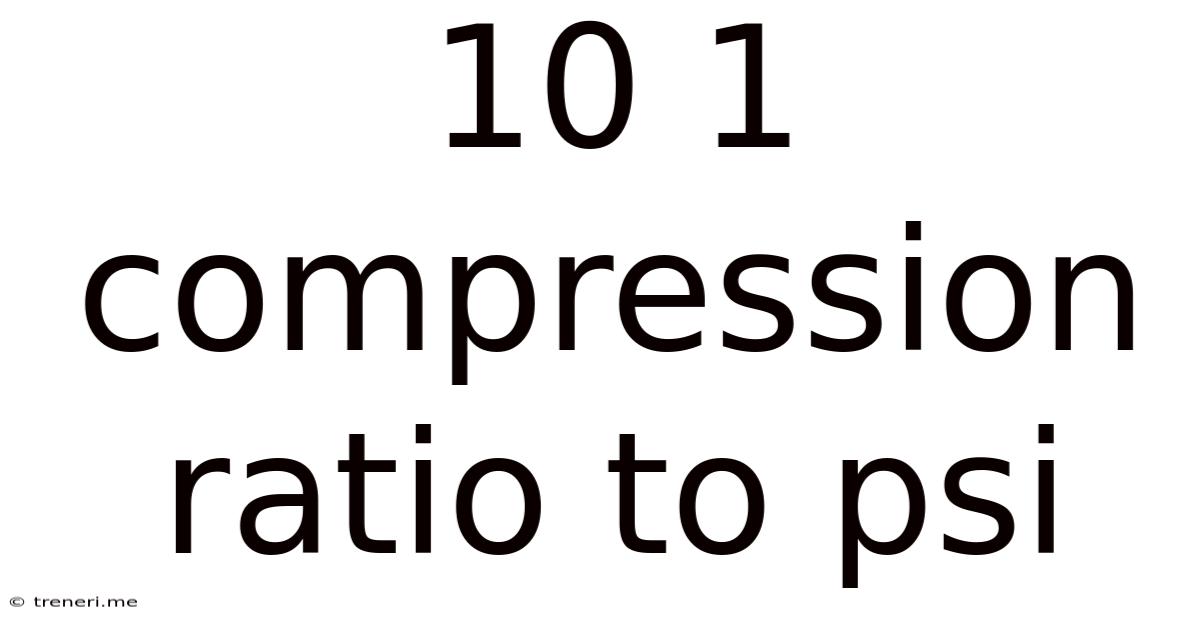
Table of Contents
10:1 Compression Ratio to PSI: A Deep Dive into Engine Performance
Understanding the relationship between compression ratio and cylinder pressure (PSI) is crucial for anyone interested in engine performance, tuning, or simply maintaining their vehicle. This article delves deep into the complexities of a 10:1 compression ratio, exploring its implications for power output, fuel efficiency, and the necessary considerations for its successful implementation. We'll explore the conversion from compression ratio to PSI, the factors influencing this conversion, and potential issues that might arise.
What is Compression Ratio?
The compression ratio is a fundamental engine specification representing the ratio of the volume of the cylinder when the piston is at the bottom of its stroke (Bottom Dead Center or BDC) to the volume when the piston is at the top of its stroke (Top Dead Center or TDC). A 10:1 compression ratio means that the volume of the cylinder at BDC is ten times larger than the volume at TDC. This ratio is a crucial factor in determining the engine's performance characteristics.
Why is Compression Ratio Important?
A higher compression ratio leads to:
-
Increased Power Output: Higher compression increases the pressure and temperature of the air-fuel mixture before ignition, resulting in a more powerful explosion and greater force pushing the piston down.
-
Improved Fuel Efficiency: More complete combustion due to the higher pressure and temperature means less unburnt fuel is wasted, leading to better fuel economy.
-
Enhanced Torque: A higher compression ratio often translates to increased torque, especially at lower RPMs, providing better pulling power.
However, it's important to note that a higher compression ratio also presents challenges:
-
Increased Risk of Detonation (Knocking): The higher pressure and temperature can lead to uncontrolled auto-ignition of the air-fuel mixture before the spark plug fires, causing a damaging knocking sound and potentially damaging engine components.
-
Higher Fuel Requirements: Higher compression ratios usually require higher-octane fuel to prevent detonation.
-
Design Complexity: Achieving high compression ratios may require specialized engine components and more precise manufacturing tolerances.
Converting Compression Ratio to PSI: The Complexities
Unfortunately, there isn't a simple, universally applicable formula to directly convert a 10:1 compression ratio to a specific PSI value. The actual cylinder pressure at the end of the compression stroke (which is often what's implied when discussing PSI in relation to compression ratio) depends on several interrelated factors:
1. Intake Air Pressure and Temperature:
The starting pressure and temperature of the intake air significantly impact the final cylinder pressure. A denser, cooler air charge at the start of compression leads to higher peak cylinder pressure. Altitude, air filter design, intake air temperature, and even the engine's airflow efficiency all play a crucial role.
2. Fuel-Air Mixture:
The richness of the air-fuel mixture influences the final pressure. A richer mixture (more fuel) can slightly reduce the final pressure due to the lower specific heat ratio of the mixture. Precise fuel delivery and proper air-fuel ratio control are paramount.
3. Engine Speed (RPM):**
Higher RPM generally leads to less time for the compression process, potentially resulting in slightly lower peak cylinder pressures compared to lower RPMs, although the overall rate of pressure rise would increase. The dynamic nature of engine operation significantly affects the exact pressure reached.
4. Engine Design and Combustion Characteristics:
The design of the combustion chamber, the shape of the piston crown, and the overall efficiency of the combustion process all impact the peak cylinder pressure. These factors influence how effectively the energy released during combustion is converted into mechanical energy.
5. Valve Timing and Lift:
The timing and duration of valve opening and closing events affect the amount of air inducted into the cylinder, thereby influencing the initial conditions for the compression stroke. This, in turn, impacts the final pressure.
Estimating Cylinder Pressure with a 10:1 Compression Ratio
While a precise calculation is impractical without specific engine data and conditions, we can offer a rough estimate. Assuming ideal conditions (optimal air density, stoichiometric air-fuel mixture, etc.), a 10:1 compression ratio engine might achieve peak cylinder pressures in the range of 250-350 PSI during the combustion event itself. However, this is a highly variable number and could easily deviate significantly.
It's crucial to understand that this is a very rough approximation. The actual pressure experienced will be much higher during the rapid combustion process, far exceeding these estimates. Measuring the instantaneous pressure during combustion requires specialized equipment.
Practical Implications of a 10:1 Compression Ratio
A 10:1 compression ratio represents a relatively high value, often found in performance-oriented engines or those designed for specific fuel types.
Advantages:
- Significant Power Gains: A noticeable increase in horsepower and torque compared to lower compression ratios.
- Improved Efficiency: Potentially better fuel economy due to more complete combustion.
- Stronger Low-End Torque: Enhanced pulling power at lower engine speeds.
Disadvantages:
- Detonation Risk: Higher susceptibility to knocking, particularly with lower-octane fuels. Using premium (high-octane) fuel is often mandatory.
- Increased Wear and Tear: The higher pressures and temperatures can increase wear on engine components over time.
- Higher Manufacturing Precision: Engines with high compression ratios usually require tighter tolerances and more expensive manufacturing processes.
Tuning and Modifications for 10:1 Compression Engines
Successfully running an engine with a 10:1 compression ratio often necessitates careful consideration of several factors:
- Fuel Quality: Using premium, high-octane fuel is crucial to prevent detonation.
- Ignition Timing: Precise ignition timing is essential to optimize combustion and avoid knocking. Advanced ignition timing might be necessary but requires careful calibration.
- Cooling System: Adequate cooling is critical due to the higher temperatures generated during combustion.
- Engine Management System (EMS): A sophisticated EMS is helpful for precise control of fuel delivery and ignition timing to prevent detonation and maximize efficiency.
Conclusion: Understanding the Nuances of Compression Ratio
The relationship between compression ratio and PSI is intricate and non-linear. While a 10:1 compression ratio promises substantial performance benefits, it introduces complexities that necessitate careful engine design, tuning, and fuel selection. Achieving optimal performance with this compression ratio demands a comprehensive understanding of engine mechanics and the interplay of various factors influencing combustion and pressure development. Simply converting the compression ratio to a single PSI figure without considering these factors is not only inaccurate but also potentially misleading. This deep dive has hopefully shed light on this crucial aspect of internal combustion engine performance. Remember that consulting with engine specialists and utilizing advanced diagnostic tools is crucial for optimal results when dealing with high-compression engines.
Latest Posts
Latest Posts
-
3 8 1 3 In Fraction Form
May 12, 2025
-
Cuanto Es 6 4 Pies En Metros
May 12, 2025
-
How Many Seconds Are In 18 Minutes
May 12, 2025
-
180 Days From February 8 2024
May 12, 2025
-
Greatest Common Factor Of 28 And 56
May 12, 2025
Related Post
Thank you for visiting our website which covers about 10 1 Compression Ratio To Psi . We hope the information provided has been useful to you. Feel free to contact us if you have any questions or need further assistance. See you next time and don't miss to bookmark.