3 Phase Motor Power Calculation Formula
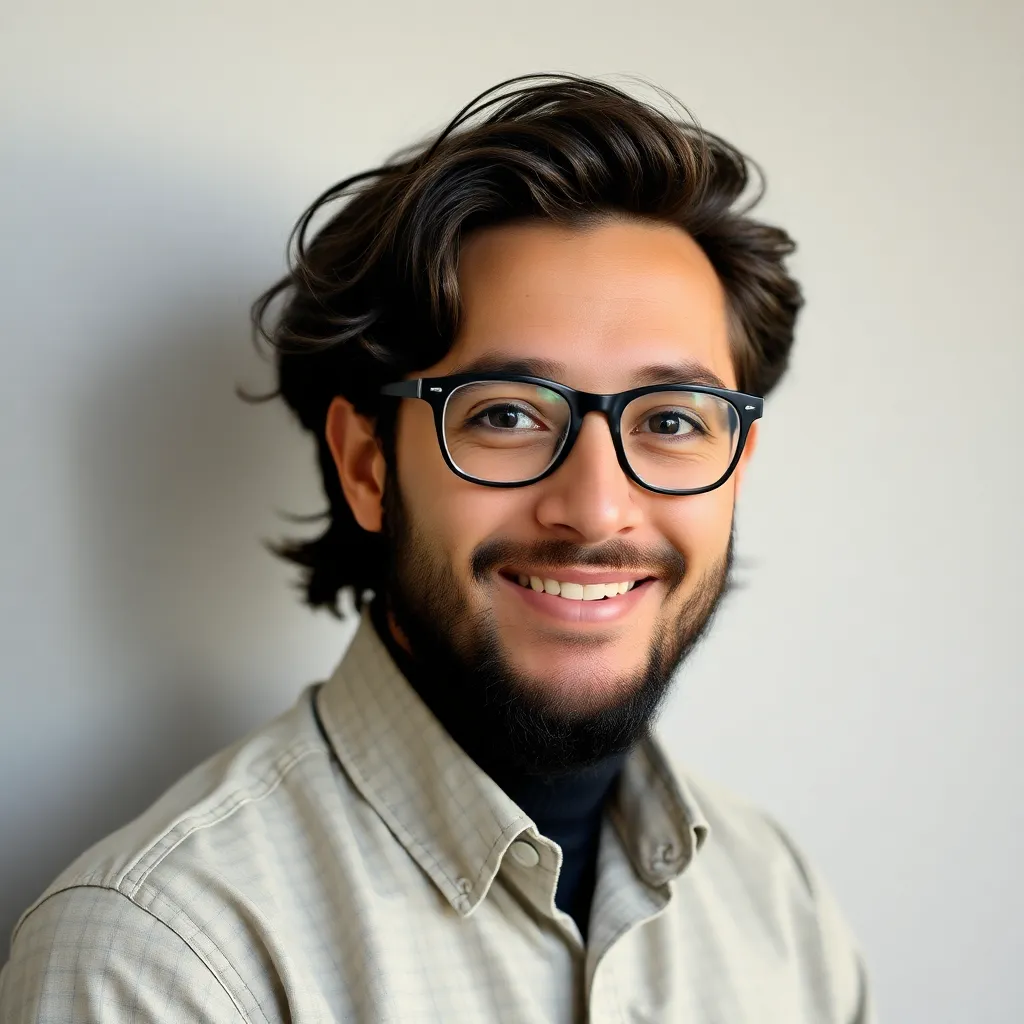
Treneri
Apr 18, 2025 · 5 min read

Table of Contents
3-Phase Motor Power Calculation: A Comprehensive Guide
Understanding how to calculate the power of a three-phase motor is crucial for electrical engineers, technicians, and anyone working with industrial machinery. Accurate power calculations ensure proper motor selection, efficient system design, and prevent potential equipment damage. This comprehensive guide will delve into the formulas, factors, and considerations involved in determining the power consumption and output of three-phase motors.
Understanding Three-Phase Power Systems
Before diving into the formulas, let's establish a foundational understanding of three-phase power systems. Three-phase systems offer significant advantages over single-phase systems, primarily due to their higher power delivery capacity and efficiency. Power is distributed across three separate phases, each carrying a portion of the total load. This balanced distribution minimizes voltage fluctuations and reduces the size and weight of required conductors compared to a single-phase system delivering the same power.
The three phases are typically designated as A, B, and C, and their voltages are offset by 120 degrees. This phase shift is critical for the balanced operation of the system. The types of three-phase connections commonly found are:
-
Wye (Y) Connection: The ends of each coil are connected together at a common neutral point. Line voltage is √3 times higher than the phase voltage.
-
Delta (Δ) Connection: The coils are connected in a closed loop, forming a triangle. Line voltage is equal to phase voltage.
Key Parameters in 3-Phase Motor Power Calculation
Several parameters are essential for accurate power calculations:
-
Voltage (V): The voltage applied to the motor terminals. This can be line voltage (voltage between any two phases) or phase voltage (voltage between one phase and the neutral).
-
Current (I): The current flowing through each phase winding.
-
Power Factor (PF): The cosine of the angle between voltage and current. A power factor of 1 indicates perfect alignment, while a lower power factor indicates a phase difference, representing reactive power. This is crucial because the apparent power (calculated from voltage and current) includes reactive power, which doesn't contribute to actual work.
-
Efficiency (η): The ratio of output power to input power. Represents the losses within the motor due to friction, heat, and other factors.
Formulas for Calculating 3-Phase Motor Power
Several formulas are used depending on the available parameters and whether you're calculating input or output power.
1. Apparent Power (S):
Apparent power represents the total power delivered to the motor, including both real and reactive power. It's expressed in Volt-Amperes (VA).
For a three-phase system:
S = √3 * V_L * I_L
Where:
- S = Apparent power (VA)
- V_L = Line voltage (V)
- I_L = Line current (A)
This formula applies to both Wye and Delta connections.
2. Real Power (P):
Real power, also known as active power or true power, represents the power actually used to do work. It's measured in Watts (W).
P = √3 * V_L * I_L * PF
Where:
- P = Real power (W)
- V_L = Line voltage (V)
- I_L = Line current (A)
- PF = Power factor
3. Reactive Power (Q):
Reactive power is the power that oscillates between the source and the load, not contributing to actual work. It's measured in Volt-Ampere Reactive (VAR).
Q = √3 * V_L * I_L * sin(θ)
Where:
- Q = Reactive power (VAR)
- V_L = Line voltage (V)
- I_L = Line current (A)
- θ = Angle between voltage and current (power factor angle) sin(θ) = √(1 - PF²)
4. Output Power (P_out):
Output power is the actual mechanical power delivered by the motor to the load. It's calculated from the input power and motor efficiency.
P_out = P_in * η
Where:
- P_out = Output power (W)
- P_in = Input power (W) (Real power calculated previously)
- η = Efficiency (decimal value, e.g., 0.9 for 90% efficiency)
5. Horsepower (HP):
Power is often expressed in horsepower, particularly in motor specifications. The conversion is:
1 HP ≈ 746 W
Practical Considerations and Applications
Several factors influence the accuracy of these calculations and the overall performance of the motor.
1. Power Factor Correction:
Low power factors reduce the efficiency of the power system and increase operating costs. Power factor correction capacitors are often used to improve the power factor, bringing it closer to 1.
2. Motor Nameplate Data:
The motor's nameplate provides essential information, including voltage, current, power rating, and efficiency. Always refer to the nameplate data for the most accurate starting point in your calculations.
3. Load Characteristics:
The type of load connected to the motor influences its power consumption. A variable load may require different power calculations for different operating conditions.
Examples: Calculating 3-Phase Motor Power
Let's illustrate the calculations with two examples:
Example 1: Calculating Real Power
A three-phase motor operates at 480V line voltage and draws 20A line current with a power factor of 0.85.
- Real Power (P): P = √3 * 480V * 20A * 0.85 ≈ 13300 W or 13.3 kW
Example 2: Calculating Output Power
A motor has an input power of 15kW and an efficiency of 92%.
- Output Power (P_out): P_out = 15000W * 0.92 ≈ 13800 W or 13.8 kW
Advanced Considerations
For more precise calculations, you might need to consider factors such as:
-
Temperature Effects: Temperature affects motor performance and efficiency.
-
Harmonics: Non-linear loads can introduce harmonics into the power system, impacting power calculations.
-
Motor Slip: The difference between synchronous speed and actual motor speed.
-
Motor Type: Different motor types (induction, synchronous, etc.) have varying characteristics that affect power calculations.
Conclusion
Calculating the power of a three-phase motor is vital for various applications. This guide has provided a comprehensive overview of the formulas, parameters, and practical considerations involved. Accurate calculations lead to efficient system design, improved motor selection, reduced energy costs, and ultimately, a safer and more reliable industrial operation. Remember to always refer to the motor nameplate data and consider the factors discussed to achieve the most accurate results. Further exploration into advanced power system analysis techniques will provide even greater precision for complex industrial setups.
Latest Posts
Latest Posts
-
How Many Half Pints In A Gallon
Apr 19, 2025
-
How Much Grams Is A Pound
Apr 19, 2025
-
Can I Tan In Uv 4
Apr 19, 2025
-
How Long Is 18 Days In Weeks
Apr 19, 2025
-
How Much Is 20 Gallons Of Gas
Apr 19, 2025
Related Post
Thank you for visiting our website which covers about 3 Phase Motor Power Calculation Formula . We hope the information provided has been useful to you. Feel free to contact us if you have any questions or need further assistance. See you next time and don't miss to bookmark.