How Do You Calculate Lead Time
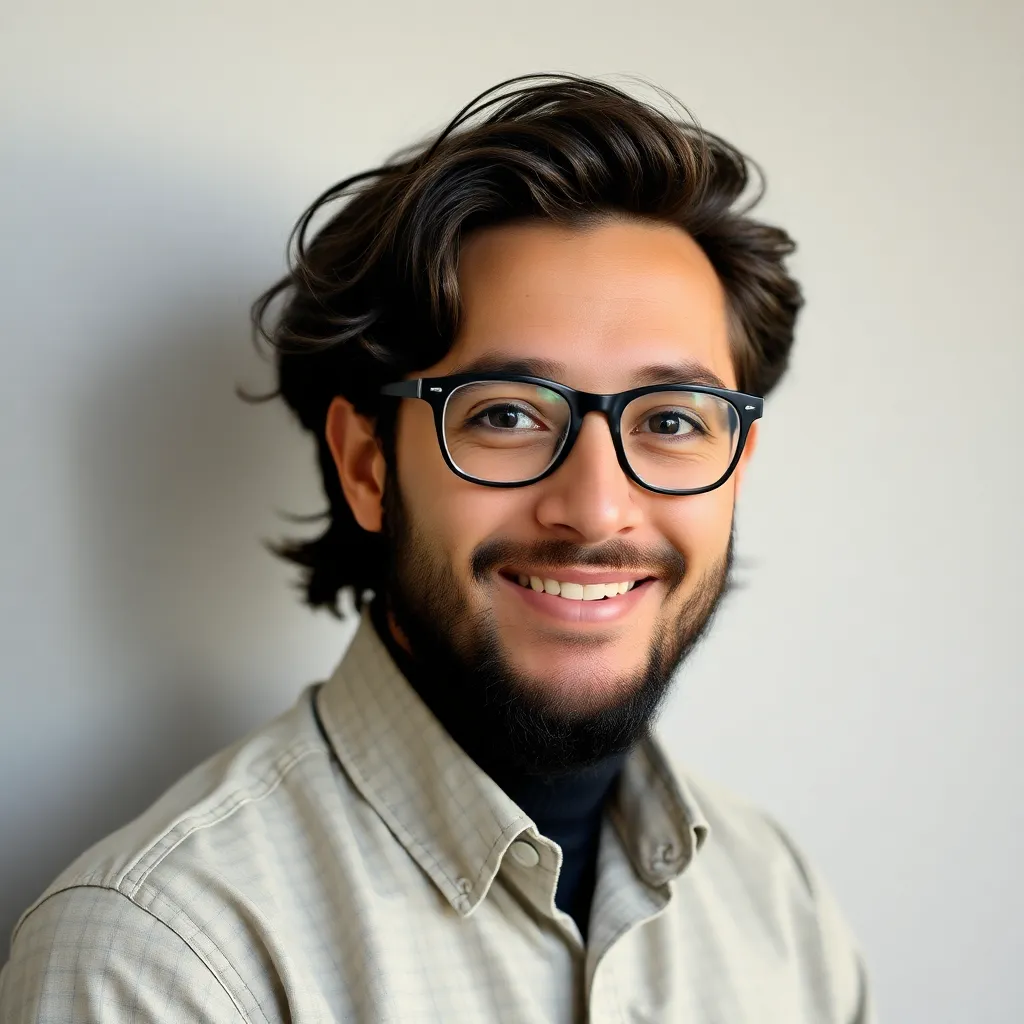
Treneri
Apr 23, 2025 · 6 min read

Table of Contents
How Do You Calculate Lead Time? A Comprehensive Guide
Lead time, the period between initiating a process and its completion, is a critical metric across diverse industries. Understanding and effectively calculating lead time is crucial for optimizing operations, improving customer satisfaction, and gaining a competitive edge. This comprehensive guide will delve into the intricacies of lead time calculation, exploring various methods, factors influencing it, and strategies for its effective management.
What is Lead Time?
Lead time represents the total time required to complete a process, from initiation to final delivery or completion. This timeframe encompasses all stages involved, from order placement to product delivery or service completion. Accurately calculating lead time allows businesses to:
- Improve Forecasting: Predict future demands and production needs more precisely.
- Enhance Inventory Management: Optimize stock levels to meet customer demands without excessive storage costs.
- Streamline Operations: Identify bottlenecks and inefficiencies in the production process for improvement.
- Boost Customer Satisfaction: Meet delivery deadlines and enhance overall customer experience.
- Gain Competitive Advantage: Offer faster turnaround times compared to competitors.
Different Types of Lead Time
While the core concept remains consistent, lead time can manifest in various forms depending on the context:
1. Procurement Lead Time:
This refers to the time taken to acquire necessary materials or components from suppliers. It starts from placing an order and ends with the receipt of goods. Factors such as supplier reliability, shipping times, and customs clearance significantly influence this lead time.
2. Manufacturing Lead Time:
This encompasses the duration from raw material receipt to finished goods production. It includes processing, assembly, quality control, and other manufacturing stages. Efficient production processes and streamlined workflows directly impact manufacturing lead time.
3. Order-to-Delivery Lead Time (OTD):
This represents the entire time from order placement to final product or service delivery to the customer. It encompasses all preceding lead times, including procurement, manufacturing, and potentially shipping. This is the most customer-centric lead time metric.
4. Production Lead Time:
This is the time between starting the production process and completing it. It focuses on the actual manufacturing or creation of the product or service and does not include order placement or delivery.
5. Project Lead Time:
In project management, lead time refers to the total time allocated to complete a project. This considers all tasks, dependencies, and potential delays.
How to Calculate Lead Time: Step-by-Step Guide
Calculating lead time involves meticulously tracking time spent at each stage of the process. The method employed depends on the complexity of the process and the data available.
1. Identify the Process Stages: Break down the entire process into individual, clearly defined stages. For instance, in manufacturing, this might include raw material procurement, production, quality inspection, packaging, and shipping.
2. Time Tracking: Implement a system for accurately tracking the time spent at each stage. This could involve:
- Manual Tracking: Using spreadsheets or simple time logs to record start and end times for each stage. This is suitable for simpler processes.
- Software Solutions: Employing specialized software designed for project management, ERP systems, or CRM platforms to automatically track time spent on various tasks. This is ideal for complex processes with multiple stakeholders.
3. Data Collection: Collect data consistently across multiple cycles or batches to get a statistically significant sample size. A larger dataset provides a more accurate representation of the lead time.
4. Calculation: Once data is gathered, calculate the lead time for each stage and the overall lead time. This typically involves subtracting the start time from the end time for each stage. Summing up the time for all stages provides the total lead time.
5. Analysis: Analyze the data to identify potential bottlenecks or areas for improvement. Identify stages with consistently longer durations compared to others.
Methods for Calculating Lead Time
The choice of method depends on the available data and the desired level of accuracy:
1. Simple Average Lead Time:
This is the simplest method and suitable for processes with relatively consistent lead times. It involves summing all individual lead times and dividing by the number of cycles.
Formula: Average Lead Time = (Sum of all Lead Times) / (Number of Cycles)
2. Weighted Average Lead Time:
This method is beneficial when different stages have varying levels of importance or complexity. It assigns weights to each stage based on its relative significance, providing a more nuanced representation of lead time.
Formula: Weighted Average Lead Time = Σ (Weight of Stage * Lead Time of Stage) / Σ Weights
3. Moving Average Lead Time:
This is useful when lead times fluctuate over time. It calculates the average lead time over a specific period, discarding older data to reflect recent trends. The "moving" aspect refers to the sliding window of data considered. A common choice is a 3-month or 6-month moving average.
Formula: Moving Average Lead Time = (Sum of Lead Times within the defined period) / (Number of periods)
Factors Influencing Lead Time
Numerous factors can influence lead time, making consistent monitoring and analysis crucial. These factors include:
- Supplier Reliability: Delays from suppliers can significantly impact procurement lead time.
- Production Capacity: Insufficient production capacity leads to longer manufacturing lead times.
- Inventory Levels: Adequate stock levels minimize delays caused by material shortages.
- Equipment Maintenance: Regular maintenance prevents equipment downtime, reducing lead time.
- Employee Skill and Training: Well-trained employees ensure efficient execution of tasks.
- Workflow Efficiency: Optimized workflows streamline the process, reducing overall lead time.
- Quality Control Procedures: Rigorous quality control can lengthen lead times but ensures superior product quality.
- Transportation and Logistics: Efficient transportation and logistics minimize shipping delays.
- Seasonality: Seasonal fluctuations in demand can impact lead times.
- External Factors: Unforeseen circumstances like natural disasters or economic downturns can cause delays.
Strategies for Lead Time Reduction
Reducing lead time requires a multi-pronged approach focusing on process optimization, technology integration, and proactive management:
- Process Mapping: Visualize the entire process to identify bottlenecks and areas for improvement.
- Lean Manufacturing Principles: Implement lean methodologies to eliminate waste and optimize workflows.
- Automation: Automate repetitive tasks to increase efficiency and reduce errors.
- Inventory Optimization: Implement just-in-time (JIT) inventory management to reduce storage costs and minimize delays.
- Supplier Relationship Management: Build strong relationships with reliable suppliers to ensure timely deliveries.
- Technology Integration: Employ ERP and other software solutions for better tracking and management of lead times.
- Employee Training and Development: Invest in training to improve employee skills and efficiency.
- Regular Performance Monitoring: Continuously monitor lead times to identify emerging issues and make necessary adjustments.
- Data-Driven Decision Making: Use data analytics to understand trends and make informed decisions for lead time reduction.
Conclusion
Lead time is a crucial metric that impacts various aspects of a business. Calculating lead time accurately requires a systematic approach, starting with process mapping and meticulous time tracking. By understanding the various methods for calculation, identifying factors influencing lead time, and implementing effective reduction strategies, businesses can enhance operational efficiency, improve customer satisfaction, and gain a competitive advantage. Remember that consistent monitoring and analysis are paramount to continuous improvement and successful lead time management.
Latest Posts
Latest Posts
-
How Many Meters Is 5 Cm
Apr 23, 2025
-
How Many Miles Is 260 Kilometers
Apr 23, 2025
-
1 Atm To Mm Of Hg
Apr 23, 2025
-
1 5 Cu Ft To Lbs Soil
Apr 23, 2025
-
How Much Is 22 000 Pennies In Dollars
Apr 23, 2025
Related Post
Thank you for visiting our website which covers about How Do You Calculate Lead Time . We hope the information provided has been useful to you. Feel free to contact us if you have any questions or need further assistance. See you next time and don't miss to bookmark.