How Do You Calculate The Efficiency Of A Machine
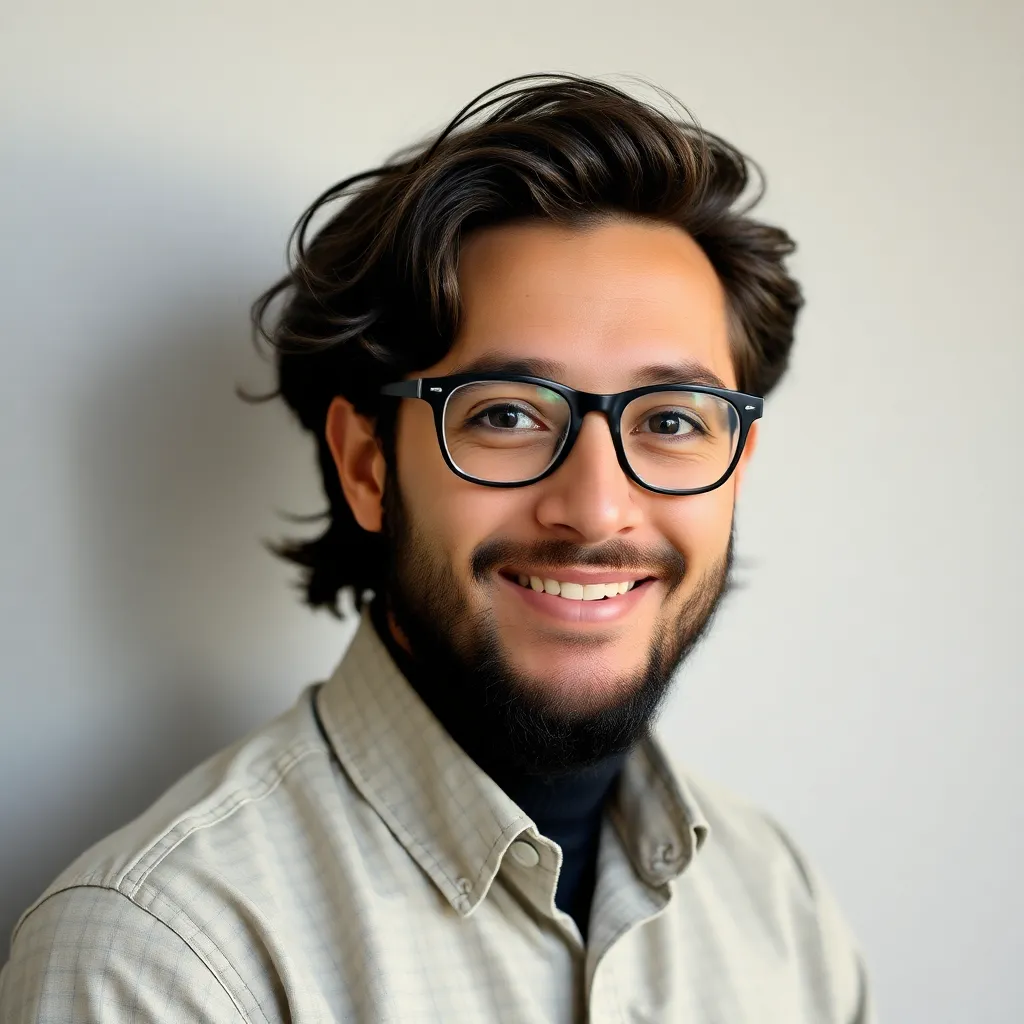
Treneri
May 11, 2025 · 5 min read
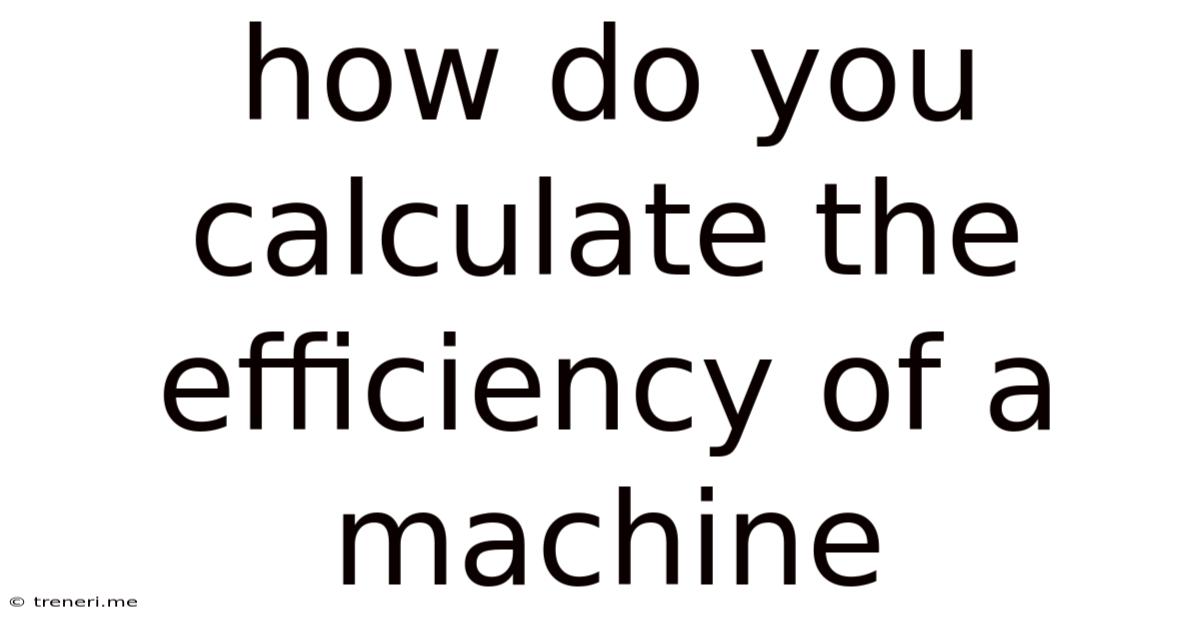
Table of Contents
How Do You Calculate the Efficiency of a Machine? A Comprehensive Guide
Understanding machine efficiency is crucial for optimizing performance, reducing waste, and improving profitability across various industries. Whether you're designing a new engine, analyzing a manufacturing process, or troubleshooting a malfunctioning appliance, knowing how to calculate efficiency is a valuable skill. This comprehensive guide will delve into the methods and concepts behind calculating machine efficiency, offering practical examples and insights.
What is Machine Efficiency?
Machine efficiency is a measure of how effectively a machine converts input energy or resources into useful output. It's expressed as a percentage, representing the ratio of useful output to the total input. A higher efficiency percentage indicates that the machine is performing optimally, minimizing energy waste and maximizing productivity. Conversely, a low efficiency percentage points to potential areas for improvement or the presence of inefficiencies.
In simple terms: Efficiency = (Useful Output / Input) x 100%
This fundamental formula applies across various machine types and energy forms, but the specific definitions of "input" and "useful output" can vary depending on the application.
Factors Affecting Machine Efficiency
Before delving into calculations, understanding the factors that influence a machine's efficiency is essential. These factors can be broadly categorized as:
1. Design and Construction:
- Friction: Friction between moving parts consumes energy and reduces efficiency. Well-lubricated components, precise machining, and the use of low-friction materials are crucial for minimizing frictional losses.
- Material Properties: The choice of materials directly impacts efficiency. Stronger, lighter materials can reduce energy consumption in moving parts. Materials with superior heat resistance are essential for high-temperature applications.
- Aerodynamics/Hydrodynamics: In machines involving fluid flow (e.g., pumps, turbines), streamlined designs minimize drag and improve efficiency.
- Manufacturing Tolerances: Precise manufacturing minimizes energy losses due to misalignments or vibrations.
2. Operational Factors:
- Load: The efficiency of many machines varies with the load. Operating at or near the optimal load often results in peak efficiency.
- Maintenance: Regular maintenance is crucial for sustaining efficiency. Worn parts, inadequate lubrication, and accumulated debris contribute to energy losses.
- Operator Skill: In some cases, operator skill affects efficiency. Proper operation and maintenance procedures maximize machine performance.
- Environmental Conditions: Temperature, humidity, and altitude can influence the performance of certain machines.
3. Energy Source and Conversion:
- Energy Losses during Conversion: The process of converting energy from one form to another (e.g., chemical to mechanical) always involves some energy losses as heat.
- Energy Quality: The quality of the input energy (e.g., consistent voltage, clean fuel) affects the efficiency of the conversion process.
Calculating Machine Efficiency: Different Approaches
The calculation of machine efficiency varies based on the type of machine and the nature of the energy transformation involved. Let's explore some common scenarios:
1. Mechanical Machines (e.g., Gear Systems, Levers, Pulleys):
For mechanical machines, efficiency is typically calculated as the ratio of useful work output to work input.
Formula: Efficiency = (Useful Work Output / Work Input) x 100%
- Work Input: This is the energy supplied to the machine, often calculated as force multiplied by distance (W = Fd).
- Useful Work Output: This is the work done by the machine in achieving its intended purpose. This often requires accounting for frictional losses and other inefficiencies.
Example: A pulley system lifts a 100 kg weight to a height of 5 meters using a force of 600 N applied over a distance of 10 meters.
- Work Input = 600 N * 10 m = 6000 J
- Work Output = 100 kg * 9.8 m/s² * 5 m = 4900 J
- Efficiency = (4900 J / 6000 J) x 100% = 81.67%
2. Thermal Machines (e.g., Internal Combustion Engines, Power Plants):
For thermal machines, efficiency is typically calculated based on the energy input and output in thermal units (e.g., Joules, BTU).
Formula: Efficiency = (Useful Energy Output / Heat Input) x 100%
- Heat Input: The amount of heat energy supplied to the machine. This could be from fuel combustion, electrical heating, etc.
- Useful Energy Output: The amount of mechanical or other useful energy produced by the machine.
Example: An engine consumes 10,000 Joules of heat energy from fuel combustion and produces 3,000 Joules of mechanical work.
- Efficiency = (3000 J / 10000 J) x 100% = 30%
3. Electrical Machines (e.g., Motors, Generators):
For electrical machines, efficiency is typically calculated as the ratio of electrical power output to electrical power input.
Formula: Efficiency = (Useful Power Output / Power Input) x 100%
- Power Input: The electrical power supplied to the machine, often measured in Watts (W).
- Useful Power Output: The electrical or mechanical power produced by the machine.
Example: An electric motor draws 1000 Watts of power and delivers 850 Watts of mechanical power.
- Efficiency = (850 W / 1000 W) x 100% = 85%
4. Manufacturing Processes:
In manufacturing, efficiency is often calculated differently depending on what is being measured:
- Labor Efficiency: Relates output to labor hours. (Output / Labor Hours)
- Material Efficiency: Relates the amount of usable material to the total material used. (Usable Material / Total Material Used)
- Energy Efficiency: Relates the output to the total energy consumed. (Output / Energy Consumed)
- Overall Equipment Effectiveness (OEE): A more comprehensive metric considering availability, performance, and quality. OEE calculation is more complex and requires detailed data on machine downtime, speed, and defects.
Improving Machine Efficiency
Improving machine efficiency involves a multifaceted approach that often necessitates a detailed analysis of the system and its components. Some common strategies include:
- Regular Maintenance: Preventing breakdowns, reducing wear and tear, and ensuring proper lubrication are essential.
- Optimization of Operating Parameters: Operating machines at their optimal load, speed, and temperature settings.
- Technological Upgrades: Implementing new technologies or improving existing systems can lead to significant efficiency gains. This might include the use of more efficient motors, improved control systems, or advanced materials.
- Process Improvement: Streamlining processes and eliminating bottlenecks can improve overall efficiency.
- Energy Management: Implementing energy-efficient practices, such as using energy-saving lighting, optimizing HVAC systems, and reducing idle time for equipment.
- Employee Training: Ensuring operators are well-trained to use and maintain machines correctly can minimize inefficiencies.
Conclusion: A Holistic Approach to Efficiency
Calculating machine efficiency is a crucial step in optimizing performance and reducing waste. The specific method used depends heavily on the type of machine and the nature of the energy transformations involved. However, the underlying principle remains consistent: maximizing useful output relative to input. By understanding the factors affecting efficiency and employing the appropriate calculation methods, engineers, managers, and operators can identify areas for improvement, leading to significant cost savings, enhanced productivity, and improved sustainability. Furthermore, consistently monitoring and analyzing efficiency data is essential for continuous improvement and optimizing the performance of machines and processes.
Latest Posts
Latest Posts
-
30 Year Amortization 5 Year Balloon
May 11, 2025
-
How To Find Base Of Trapezoid
May 11, 2025
-
Cuanto Falta Para El 10 De Septiembre
May 11, 2025
-
43 27 An Hour Is How Much A Year
May 11, 2025
-
How Much Soil Do I Need For Lawn
May 11, 2025
Related Post
Thank you for visiting our website which covers about How Do You Calculate The Efficiency Of A Machine . We hope the information provided has been useful to you. Feel free to contact us if you have any questions or need further assistance. See you next time and don't miss to bookmark.