How To Bend A Rolling Offset
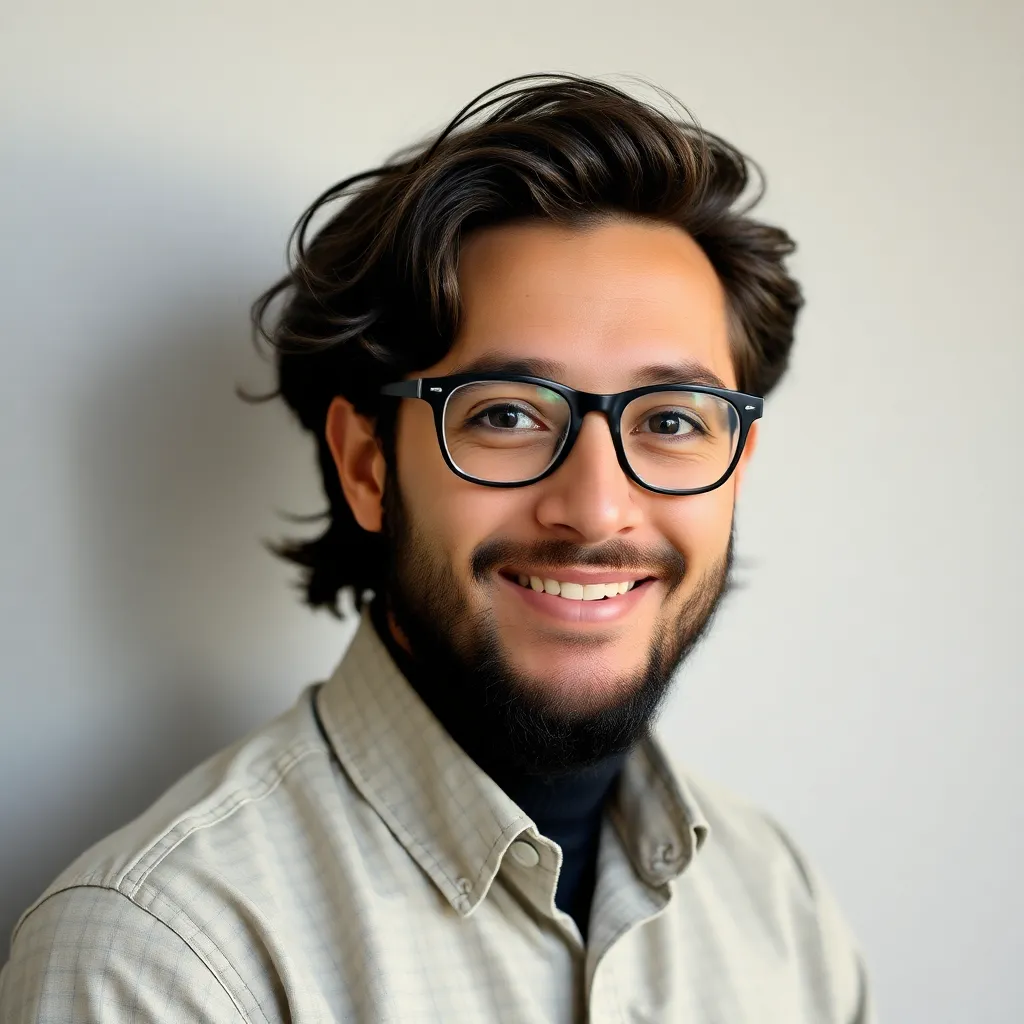
Treneri
May 15, 2025 · 6 min read

Table of Contents
How to Bend a Rolling Offset: A Comprehensive Guide for HVAC Professionals
Rolling offsets, also known as saddle offsets, are a crucial element in HVAC ductwork installation. They're used to smoothly transition between two sections of ductwork that are at different heights or angles, maintaining a consistent airflow. However, accurately bending a rolling offset requires precision and skill. This comprehensive guide will walk you through the process, covering everything from planning and measurement to the bending techniques themselves.
Understanding Rolling Offsets: Terminology and Geometry
Before we dive into the bending process, let's clarify some essential terminology:
Key Terms:
- Offset: The horizontal or vertical distance between the two duct sections.
- Roll: The curved section of the duct connecting the two straight sections. It's essentially the "bend" itself.
- Radius: The distance from the center of the curve to the outer edge of the duct. A smaller radius results in a tighter bend.
- Throat: The shortest distance between the two straight duct sections.
- Setback: The distance from the start of the roll to where the duct changes direction.
Geometry of a Rolling Offset:
The accurate creation of a rolling offset relies on precise calculations. Understanding the relationship between the offset, roll length, and radius is crucial. Various formulas and calculators are available online to help determine these dimensions, ensuring a perfect fit. However, having a solid understanding of the underlying geometry helps in troubleshooting and making adjustments on the fly.
Tools and Materials You'll Need:
Having the right tools is essential for a successful bend. This list includes:
- Measuring Tape: Crucial for accurate measurements of the offset and other dimensions.
- Metal Duct: The material you'll be bending – aluminum, galvanized steel, etc. Choose the appropriate gauge for your application.
- Marking Tools: A pencil, marker, or scribe for marking the bending points on the duct.
- Notch Tool: Used for creating precise notches for bending, especially on thicker gauge metal.
- Sheet Metal Snips or Shears: For cutting the duct to the required length.
- Hand Bender or Hydraulic Bender: Depending on the size and material of the duct, you might need a hand bender for smaller ducts or a hydraulic bender for larger ones. Hand benders are suitable for simpler bends, while hydraulic benders provide more control and precision for complex projects.
- Angle Finder: Helps in measuring angles accurately.
- Safety Glasses: Protecting your eyes is essential while working with metal and tools.
- Gloves: To protect your hands from sharp edges.
- Slip Roll Former (Optional but highly recommended): This tool significantly simplifies the creation of rolling offsets, particularly for tighter radius bends. It allows for more precise and consistent bends compared to manual techniques.
- Bead Roller (Optional but helpful): This helps create reinforcing beads on the edges of the metal before bending. This increases the strength and stiffness of the ductwork, reducing the risk of damage during the bending process.
- Welding Equipment (Depending on material): For joining the duct sections and reinforcing the bend, if required. This is usually necessary for heavier gauge steel ductwork.
Step-by-Step Guide to Bending a Rolling Offset:
Let's assume you've already calculated the necessary dimensions of your rolling offset using the appropriate formulas or calculators. Now, here’s a step-by-step process:
Step 1: Prepare the Ductwork
- Measure and Cut: Cut the duct to the correct length, ensuring you add extra material for the bends. Accurate measurements are crucial to prevent costly mistakes.
- Mark the Bending Points: Carefully mark the points on the duct where the bends will begin and end, according to your calculations. Precise marking is essential for a smooth, consistent bend.
- Notching (If Necessary): For thicker gauge metal, creating precise notches before bending is vital. This helps to prevent creasing or collapsing of the duct during the bending process. This step is particularly important when using a hand bender.
Step 2: Bending with a Hand Bender
- Secure the Duct: Properly secure the duct in the hand bender, ensuring it's aligned with the bending axis.
- Gradual Bending: Apply steady pressure to the bender, gradually forming the curve. Avoid applying sudden force, as this can cause kinks or creases.
- Continuous Monitoring: Continuously check the bend against your measurements and markings to ensure it's accurate and consistent.
- Multiple Bends: For larger offsets, the bend might require multiple smaller bends to achieve the correct shape. Make sure to check and adjust after each small increment.
Step 3: Bending with a Hydraulic Bender
- Secure the Duct: Place the duct securely in the hydraulic bender, aligning it correctly according to the bending radius and angle.
- Set the Radius: Adjust the bender's settings to match your calculated radius.
- Apply Hydraulic Pressure: Carefully and slowly apply hydraulic pressure to bend the duct to the desired shape.
- Precise Control: Hydraulic benders offer greater precision, allowing for more accurate and consistent bends.
Step 4: Bending with a Slip Roll Former
- Feed the Material: The slip roll former requires feeding the metal progressively through the rollers, creating a consistent curve.
- Adjust Rollers: Adjust the spacing and pressure of the rollers to achieve the desired radius.
- Smooth and Consistent Roll: The slip roll former produces a smooth, even bend, reducing the chance of imperfections. This is generally the most efficient and precise method for experienced professionals.
Step 5: Joining the Sections
- Prepare the ends: Trim the ends of the bent duct and the straight sections to be joined, ensuring they fit perfectly.
- Join the Sections: Use appropriate joining methods: welding (for heavier gauge metal), mechanical fasteners (such as screws or rivets), or adhesive (for certain lightweight materials).
- Reinforce (If Necessary): Consider reinforcing the joints and bends for added strength and durability, especially in high-pressure applications.
Step 6: Final Inspection and Adjustments
- Check for Accuracy: Carefully inspect the finished rolling offset to ensure it meets your specifications. Measure the offset, throat, and radius to verify accuracy.
- Make Adjustments (If Necessary): If any adjustments are needed, carefully rework the bends until they are correct. It's better to take the time to correct minor errors than to proceed with an improperly bent offset.
- Clean-up: Remove any excess material, burrs, or sharp edges to ensure a clean and professional finish.
Troubleshooting Common Problems:
- Kinks or Creases: These often result from applying too much force during bending or improper use of the bending tools. Careful, gradual bending is crucial.
- Inconsistent Radius: This is caused by inaccurate measurements or uneven bending pressure. Double-check your calculations and ensure consistent pressure throughout the bending process.
- Poor Fit: Inaccurate measurements during the initial planning stage are the most common cause of a poor fit. Always double-check your calculations and measurements.
Advanced Techniques and Considerations:
- Multiple Offsets: More complex installations may require multiple rolling offsets in a sequence. Accurate planning and precise bending techniques are crucial for a successful outcome.
- Elbows and Transitions: Rolling offsets often need to be integrated with elbows and other ductwork components. Careful consideration of these transitions is important to ensure smooth airflow.
- Material Selection: The choice of material affects the bending process and the overall durability of the ductwork. Thicker gauge materials require more force to bend, but are more resistant to damage.
- Safety Precautions: Always prioritize safety. Wear appropriate personal protective equipment (PPE) throughout the process.
Conclusion:
Bending a rolling offset accurately requires skill, precision, and a good understanding of the underlying geometry. Whether you're using a hand bender, hydraulic bender, or slip roll former, careful planning and attention to detail are paramount. By following these steps and understanding potential problems, you can successfully create rolling offsets that meet your specifications and contribute to a professional and efficient HVAC installation. Remember that practice and experience are key to mastering this vital skill in the HVAC trade.
Latest Posts
Latest Posts
-
What Grade Is A 48 Out Of 60
May 15, 2025
-
90 Days From Sep 19 2023
May 15, 2025
-
Area Of Circle Inside A Square
May 15, 2025
-
90 Days From March 2 2024
May 15, 2025
-
How Do You Cross Multiply And Divide
May 15, 2025
Related Post
Thank you for visiting our website which covers about How To Bend A Rolling Offset . We hope the information provided has been useful to you. Feel free to contact us if you have any questions or need further assistance. See you next time and don't miss to bookmark.