How To Calculate Average Fixed Manufacturing Cost Per Unit
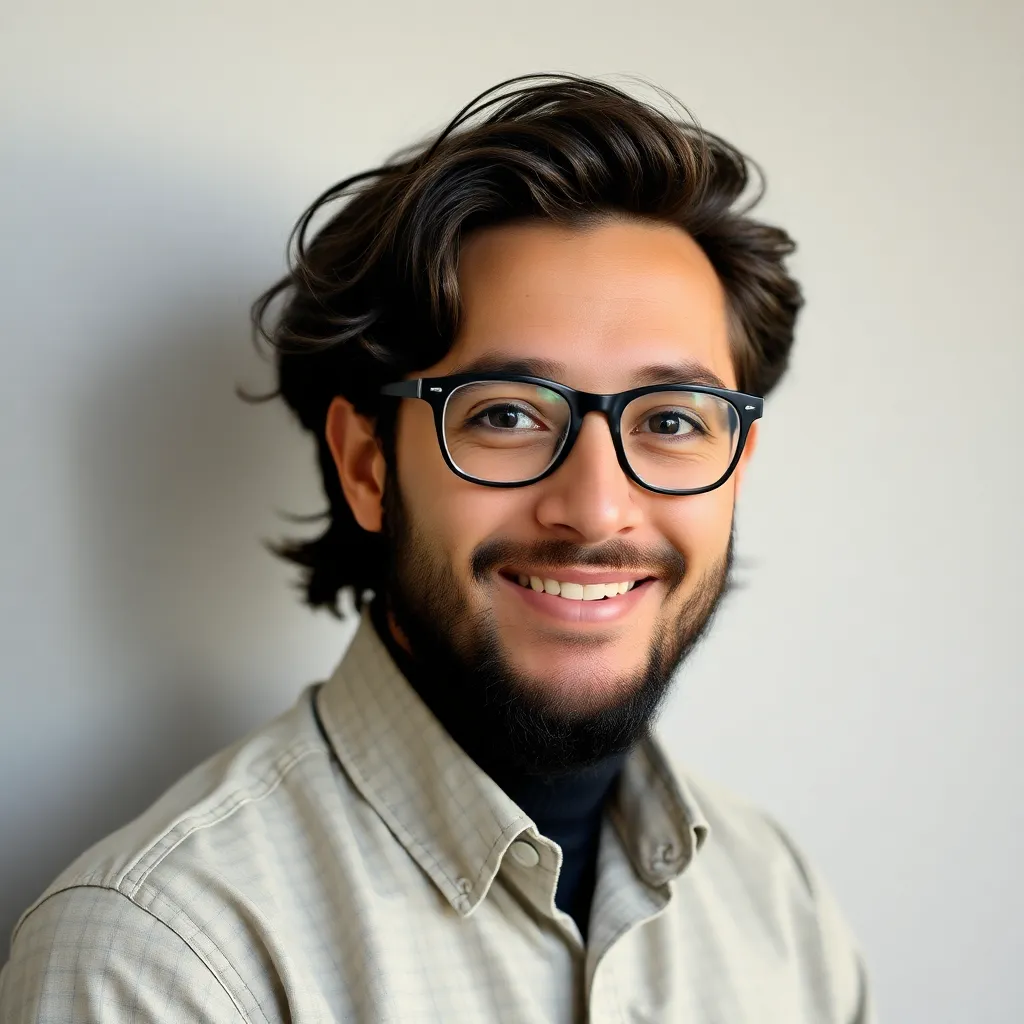
Treneri
May 13, 2025 · 5 min read
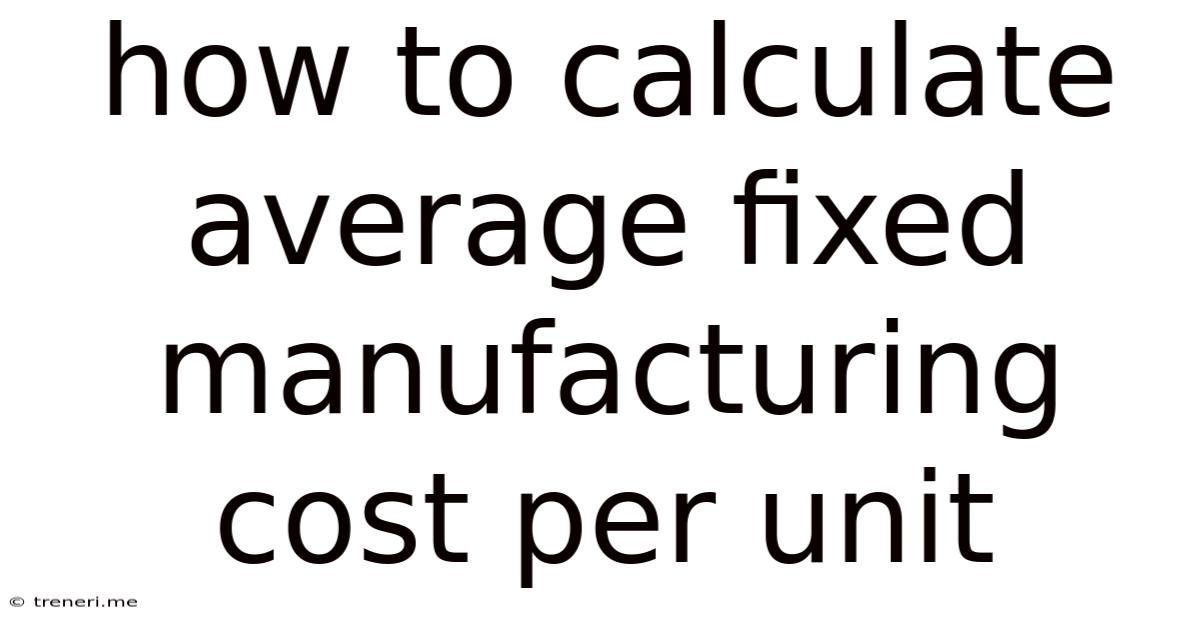
Table of Contents
How to Calculate Average Fixed Manufacturing Cost Per Unit
Understanding your manufacturing costs is crucial for pricing your products competitively, making informed business decisions, and ensuring profitability. One key element of this understanding is the average fixed manufacturing cost per unit. This metric reveals the fixed costs associated with production, spread across each unit produced. This comprehensive guide will walk you through the process of calculating this important figure, exploring its nuances and providing practical examples to solidify your understanding.
What are Fixed Manufacturing Costs?
Before diving into the calculation, let's define what constitutes fixed manufacturing costs. These are expenses that remain relatively constant regardless of the production volume. Unlike variable costs (which fluctuate with production), fixed costs stay the same within a specific production range. Examples include:
- Rent or mortgage payments for the manufacturing facility: These costs remain consistent whether you produce 100 units or 10,000 units.
- Depreciation on manufacturing equipment: The cost of equipment wears down over time, regardless of how much it's used. This depreciation is a fixed cost.
- Salaries of factory supervisors and managers: Their compensation is usually fixed, regardless of production output.
- Property taxes and insurance: These costs are largely independent of production volume.
- Licenses and permits: These are typically fixed annual or periodic expenses.
It's important to note that while these costs remain constant in the short term, they can change over the long term. For example, a lease renewal might result in a higher rent payment. Understanding this distinction is vital for accurate cost analysis.
Calculating Average Fixed Manufacturing Cost Per Unit: A Step-by-Step Guide
The calculation itself is relatively straightforward:
Average Fixed Manufacturing Cost Per Unit = Total Fixed Manufacturing Costs / Total Number of Units Produced
Let's break this down further:
1. Identify and Sum Your Total Fixed Manufacturing Costs:
Begin by compiling a comprehensive list of all your fixed manufacturing costs for a specific period (e.g., a month, quarter, or year). Be thorough and meticulous in your accounting. Ensure you only include costs directly related to manufacturing. Administrative costs or selling expenses should be excluded from this calculation.
2. Determine Your Total Number of Units Produced:
This is your total production output during the same period as your fixed cost calculation. This number should accurately reflect the total number of finished goods produced.
3. Perform the Calculation:
Divide your total fixed manufacturing costs (Step 1) by the total number of units produced (Step 2). The result is your average fixed manufacturing cost per unit.
Example Calculation:
Let's consider a small bakery that produces custom cakes. Over the last quarter, they incurred the following fixed manufacturing costs:
- Rent: $3,000
- Equipment Depreciation: $500
- Baker's Salary: $6,000
- Utilities (factory): $1,000
- Total Fixed Manufacturing Costs: $10,500
During the same quarter, they baked and sold 1,500 custom cakes.
Average Fixed Manufacturing Cost Per Unit = $10,500 / 1,500 = $7
Therefore, the average fixed manufacturing cost per unit for the bakery is $7 per cake. This means that each cake "carries" $7 of fixed manufacturing overhead.
The Importance of the Relevant Range
It's crucial to understand the concept of the relevant range when dealing with fixed costs. The relevant range is the span of activity within which the assumptions about fixed costs remain valid. Outside this range, fixed costs may not remain constant. For example, if the bakery in our example dramatically increases production (e.g., to 5,000 cakes), they might need to rent additional space or hire additional staff, thus increasing their fixed costs. The average fixed cost per unit calculation is most accurate within the relevant range of production.
Using Average Fixed Manufacturing Cost in Decision-Making
Understanding your average fixed manufacturing cost per unit is vital for several key business decisions:
- Pricing Strategies: This cost is a crucial element when determining the minimum price needed to cover your costs and achieve a profit. You need to add your variable costs per unit and desired profit margin to this fixed cost.
- Production Planning: By analyzing the relationship between production volume and average fixed cost, you can make better decisions about scaling production.
- Cost Control: Identifying areas where fixed costs can be reduced without significantly impacting production is essential for improving profitability.
- Break-Even Analysis: Knowing your fixed costs is a fundamental part of calculating your break-even point—the level of production where total revenue equals total costs.
Limitations and Considerations
While the average fixed manufacturing cost per unit provides valuable insights, it's important to be aware of its limitations:
- Simplification: It's an average and doesn't reflect variations in fixed costs across different production periods.
- Allocation Issues: Accurately allocating fixed costs across different products or product lines can be challenging, especially in diverse manufacturing environments.
- Ignoring Economies of Scale: While fixed costs remain constant, increasing production volume can lead to economies of scale in other areas, potentially reducing the overall cost per unit.
Advanced Considerations: Activity-Based Costing
For more complex manufacturing environments with multiple products and processes, activity-based costing (ABC) offers a more refined approach to allocating costs. ABC focuses on identifying cost drivers (activities that cause costs) and allocating costs based on the consumption of these activities by different products. This approach can provide a more accurate picture of the true cost of each product, surpassing the limitations of simply averaging fixed costs.
Conclusion: Mastering the Calculation for Informed Decisions
Calculating the average fixed manufacturing cost per unit is a fundamental step in understanding your manufacturing costs and making well-informed business decisions. By accurately determining this metric, within the constraints of the relevant range, and understanding its limitations, you can gain valuable insights into your profitability, pricing strategies, and production planning. Remember to combine this analysis with a thorough understanding of your variable costs and market conditions to create a robust and effective business strategy. While the calculation is simple, its application and interpretation are crucial for success in the manufacturing industry. Understanding the nuances and limitations of this calculation will empower you to make better, data-driven choices for your business.
Latest Posts
Latest Posts
-
Weight Of 25 Gallons Of Water
May 13, 2025
-
Greatest Common Factor Of 32 And 56
May 13, 2025
-
What Is The Greatest Common Factor Of 42 And 21
May 13, 2025
-
What Is The Gcf Of 12 And 54
May 13, 2025
-
Hat Size 7 5 8 In Cm
May 13, 2025
Related Post
Thank you for visiting our website which covers about How To Calculate Average Fixed Manufacturing Cost Per Unit . We hope the information provided has been useful to you. Feel free to contact us if you have any questions or need further assistance. See you next time and don't miss to bookmark.