How To Calculate Modulus Of Elasticity From Stress Strain Curve
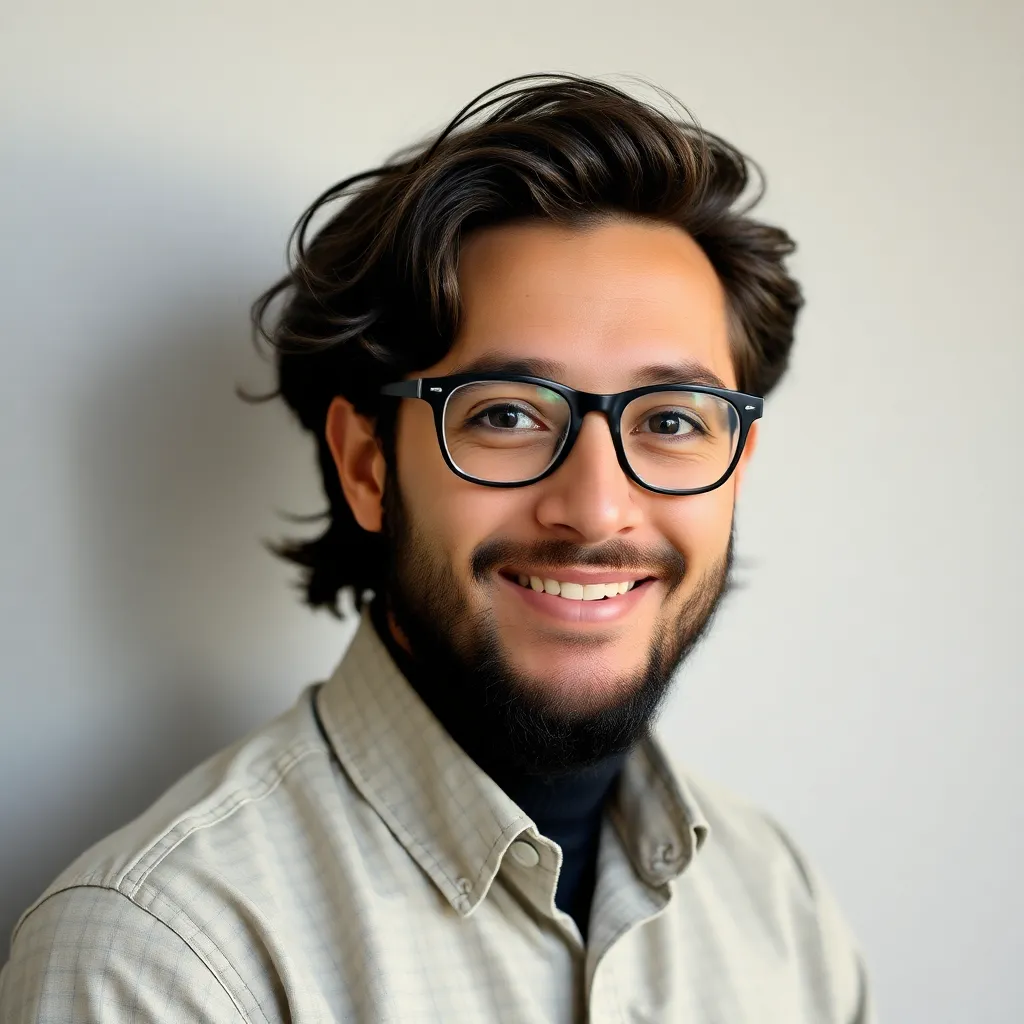
Treneri
May 13, 2025 · 5 min read

Table of Contents
How to Calculate Modulus of Elasticity from a Stress-Strain Curve
The modulus of elasticity, also known as Young's modulus (E), is a fundamental material property representing the stiffness or resistance to deformation of a solid material under tensile or compressive stress. It's crucial in engineering design, material science, and various other fields. This article will comprehensively guide you through understanding and calculating the modulus of elasticity directly from a stress-strain curve, a graphical representation of a material's response to applied force.
Understanding the Stress-Strain Curve
Before delving into calculations, it's vital to grasp the components of a stress-strain curve. This curve is generated experimentally by subjecting a material specimen to a controlled load and measuring the resulting deformation. The key parameters are:
1. Stress (σ):
Stress represents the intensity of the internal forces acting within a material caused by an externally applied load. It's calculated as:
σ = Force (F) / Area (A)
Where:
- F is the applied force (typically measured in Newtons, N).
- A is the cross-sectional area of the specimen (typically measured in square meters, m²). The units of stress are Pascals (Pa), equivalent to N/m².
2. Strain (ε):
Strain measures the deformation of the material in response to the applied stress. It's a dimensionless quantity representing the change in length relative to the original length:
ε = Change in Length (ΔL) / Original Length (L₀)
Where:
- ΔL is the increase in length (extension) or decrease in length (compression) of the specimen.
- L₀ is the original length of the specimen before applying any load.
Regions of the Stress-Strain Curve:
A typical stress-strain curve reveals several distinct regions that provide insights into the material's behavior:
-
Elastic Region: In this initial region, the material deforms elastically, meaning it returns to its original shape once the load is removed. The relationship between stress and strain is linear in this region, obeying Hooke's Law.
-
Yield Point: This point marks the transition from elastic to plastic deformation. Beyond this point, permanent deformation occurs even after the load is removed.
-
Plastic Region: In this region, the material undergoes permanent deformation. The stress-strain relationship is no longer linear.
-
Ultimate Tensile Strength: This is the maximum stress the material can withstand before failure.
-
Fracture Point: This point indicates the material's failure or breaking point.
Calculating Modulus of Elasticity from the Stress-Strain Curve
The modulus of elasticity (E) is the slope of the linear elastic portion of the stress-strain curve. This means we can calculate it using the following formula:
E = σ / ε
This equation holds true only within the elastic region where the relationship between stress and strain is linear. To calculate E:
-
Identify the Elastic Region: Locate the linear portion of the stress-strain curve. This is typically the initial part of the curve before the yield point.
-
Select Two Points: Choose two distinct points within the linear elastic region of the curve. The further apart these points are, the more accurate your calculation will be (within the limitations of the linear region). Let's denote these points as (σ₁, ε₁) and (σ₂, ε₂).
-
Calculate the Slope: The modulus of elasticity is the slope of the line connecting these two points. Use the following formula:
E = (σ₂ - σ₁) / (ε₂ - ε₁)
Where:
- σ₂ and σ₁ are the stress values at the two selected points.
- ε₂ and ε₁ are the corresponding strain values at the two selected points.
Example:
Let's say you've obtained the following data points from a stress-strain curve:
- Point 1: (σ₁ = 50 MPa, ε₁ = 0.001)
- Point 2: (σ₂ = 100 MPa, ε₂ = 0.002)
Using the formula:
E = (100 MPa - 50 MPa) / (0.002 - 0.001) = 50 MPa / 0.001 = 50,000 MPa = 50 GPa
Therefore, the modulus of elasticity for this material is 50 GPa.
Factors Affecting Modulus of Elasticity
Several factors can influence the modulus of elasticity of a material:
-
Temperature: Generally, the modulus of elasticity decreases with increasing temperature.
-
Material Composition: Different materials have vastly different moduli of elasticity. For example, steel has a much higher modulus of elasticity than rubber. Alloying and other processing techniques can significantly alter a material's E-value.
-
Microstructure: The arrangement of grains and phases within a material can influence its stiffness and hence its modulus of elasticity. For example, a fine-grained material is typically stronger and stiffer than a coarse-grained material.
-
Presence of Defects: Imperfections like voids, cracks, or inclusions within a material can reduce its overall stiffness and modulus of elasticity.
-
Loading Rate: The speed at which the load is applied can affect the measured modulus of elasticity, especially in materials exhibiting viscoelastic behavior.
Advanced Techniques and Considerations
While the simple slope calculation is sufficient for many applications, several more advanced techniques may be necessary for certain situations:
-
Digital Image Correlation (DIC): DIC is a non-contact optical method for measuring strain fields on the surface of a material under load. It provides highly accurate strain data that can be used to calculate the modulus of elasticity.
-
Finite Element Analysis (FEA): FEA is a computational technique used to simulate the mechanical behavior of materials and structures. It can be used to calculate the modulus of elasticity by comparing simulated stress-strain curves to experimental data.
-
Non-linear Elasticity: Some materials exhibit non-linear elastic behavior, meaning the stress-strain relationship is not linear even in the elastic region. In these cases, the tangent modulus, which is the slope of the stress-strain curve at a specific point, might be a more appropriate measure of stiffness.
-
Data Fitting: When experimental data points show some scatter, using regression techniques to fit a line to the data within the elastic region and then calculating the slope of this fitted line can enhance accuracy in determining the modulus of elasticity.
Conclusion
Determining the modulus of elasticity from a stress-strain curve is a crucial task in various engineering disciplines. This article has outlined the fundamental principles, procedures, and potential challenges involved in this calculation. Understanding the different regions of the stress-strain curve, accurately identifying the linear elastic region, and carefully selecting data points are essential for obtaining reliable results. While the simple slope calculation is often sufficient, advanced techniques such as DIC, FEA, and sophisticated data-fitting methods can provide more precise and comprehensive insights into material behavior, especially in cases involving non-linear elasticity or scattered experimental data. Remember to always consider the factors influencing the modulus of elasticity to fully interpret the results obtained. The accuracy of your modulus of elasticity calculation ultimately contributes to the reliability and safety of any engineering design or material analysis.
Latest Posts
Latest Posts
-
10 Minutos Saltando La Cuerda Calorias
May 13, 2025
-
Cuanto Equivale Una Libra A Kilos
May 13, 2025
-
16 Out Of 50 As A Percentage
May 13, 2025
-
How Many Ounces Are In 7 Lb
May 13, 2025
-
What Is 4 Of 100 000
May 13, 2025
Related Post
Thank you for visiting our website which covers about How To Calculate Modulus Of Elasticity From Stress Strain Curve . We hope the information provided has been useful to you. Feel free to contact us if you have any questions or need further assistance. See you next time and don't miss to bookmark.