How To Figure Out Cycle Time
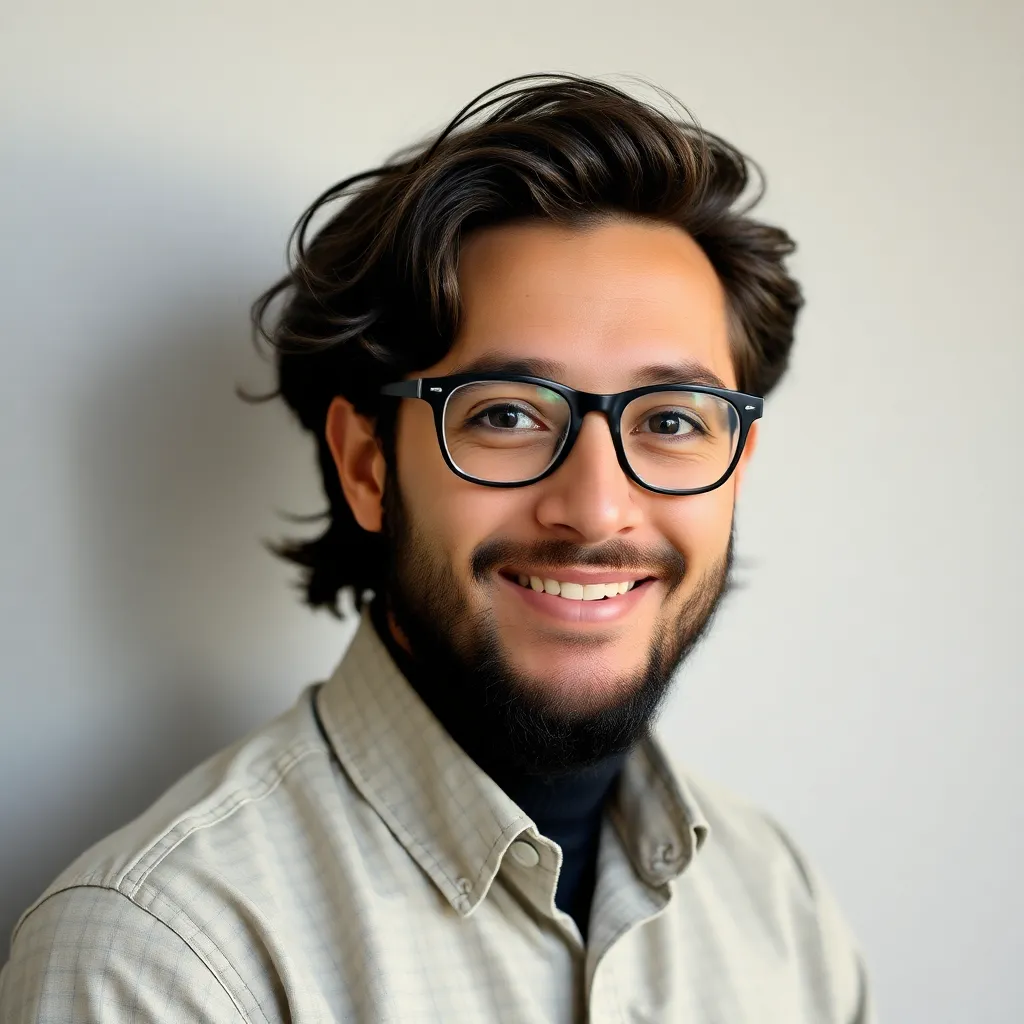
Treneri
Apr 05, 2025 · 6 min read
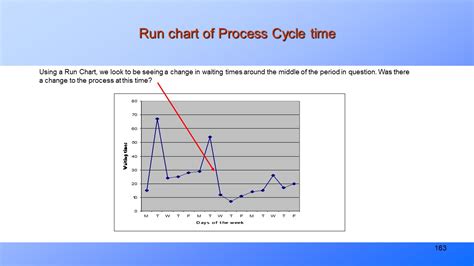
Table of Contents
How to Figure Out Cycle Time: A Comprehensive Guide
Cycle time is a crucial metric for businesses aiming to optimize processes and boost productivity. Understanding and effectively calculating cycle time allows for targeted improvements, leading to increased efficiency and profitability. This comprehensive guide will delve into the intricacies of cycle time, exploring different methodologies and offering practical strategies for accurate measurement and analysis.
What is Cycle Time?
Cycle time represents the total time it takes to complete a process, from start to finish. This encompasses all activities involved, including waiting periods, processing times, and any delays. Unlike lead time (which includes the time spent waiting for materials or approvals), cycle time focuses solely on the active time spent on the process itself. For example, in manufacturing, cycle time measures the time taken to produce one unit of a product, while in software development, it measures the time from the initiation of a task to its completion.
Key Differences between Cycle Time and Lead Time:
- Cycle Time: Focuses only on the active time spent completing a process.
- Lead Time: Includes cycle time plus any waiting time or delays.
Understanding this distinction is crucial for accurately assessing process efficiency. A short cycle time indicates a streamlined, efficient process, while a long cycle time highlights potential bottlenecks or inefficiencies that require attention.
Why is Cycle Time Important?
Accurately calculating and understanding cycle time offers numerous benefits for businesses:
- Improved Efficiency: Identifying bottlenecks and areas for improvement.
- Increased Productivity: Optimizing processes leads to faster output.
- Reduced Costs: Minimizing wasted time and resources.
- Better Planning: Accurate forecasting of project timelines and resource allocation.
- Enhanced Customer Satisfaction: Faster delivery and improved service quality.
- Data-Driven Decision Making: Using cycle time data for informed process improvements.
How to Calculate Cycle Time: Methods and Strategies
Calculating cycle time requires a systematic approach and meticulous data collection. Several methods can be employed, depending on the complexity of the process and the available data.
1. Direct Measurement: The Stopwatch Method
This is the simplest method, involving directly timing the process from start to finish using a stopwatch or timer. While straightforward, it requires careful observation and might not be feasible for complex, lengthy processes.
Steps:
- Clearly define the process start and end points. This is crucial for consistency.
- Observe the process multiple times. Repeating the measurement multiple times helps account for variability and provides a more reliable average.
- Record the time for each process cycle.
- Calculate the average cycle time. Add up all recorded times and divide by the number of observations.
Example: Let's say you're measuring the cycle time for assembling a product. You observe the process five times, recording the following times: 15 minutes, 17 minutes, 16 minutes, 14 minutes, and 18 minutes. The average cycle time would be (15 + 17 + 16 + 14 + 18) / 5 = 16 minutes.
2. Data Analysis from Existing Records: The Retrospective Method
If you already collect data on individual process steps, you can utilize this information to calculate cycle time retrospectively. This method is useful for processes with readily available data, such as those managed through ERP or CRM systems.
Steps:
- Identify all steps involved in the process.
- Gather data on the duration of each step. This data might be available in logs, reports, or databases.
- Sum the durations of all steps. This gives you the total cycle time.
- Analyze the data to identify bottlenecks. Identify steps that consume significantly more time than others.
Example: Consider a customer service process where you have data on call duration, resolution time, and follow-up time. By summing these durations for each customer interaction, you can calculate the average cycle time for handling a customer service request.
3. Work Sampling: A Statistical Approach
Work sampling involves randomly observing the process at various intervals and recording the stage of completion. This method is particularly useful for lengthy or complex processes where continuous observation is impractical.
Steps:
- Determine the observation frequency. This depends on the process duration and desired accuracy.
- Randomly select observation times. Avoid systematic sampling to avoid bias.
- Record the process stage at each observation.
- Calculate the proportion of time spent in each stage.
- Estimate the cycle time based on the proportions and individual stage durations.
This method provides a statistical estimate of the cycle time and is most accurate when a large number of observations are taken.
4. Process Mapping: Visualizing the Flow
Process mapping provides a visual representation of the entire process, making it easier to identify bottlenecks and areas for improvement. This technique helps in calculating cycle time by breaking down the process into individual steps, allowing for a more granular analysis.
Steps:
- Map out the entire process flow. Use tools like swim lane diagrams or flowcharts to visualize the steps.
- Determine the duration of each step.
- Sum the durations of all steps to calculate the cycle time.
- Analyze the map to identify bottlenecks and areas for improvement.
Analyzing Cycle Time Data: Identifying Bottlenecks and Areas for Improvement
Once the cycle time is calculated, the next step involves analyzing the data to identify areas for improvement. This often involves identifying bottlenecks – steps that significantly delay the overall process.
Common Techniques for Analyzing Cycle Time Data:
- Pareto Analysis: Identify the 20% of steps responsible for 80% of the cycle time.
- Root Cause Analysis (RCA): Investigate the underlying causes of bottlenecks. Tools like the "5 Whys" technique can be helpful here.
- Statistical Process Control (SPC): Monitor cycle time over time to detect trends and variations.
Improving Cycle Time: Practical Strategies
Based on the analysis of cycle time data, various strategies can be employed to improve efficiency and reduce cycle time:
- Streamlining Processes: Eliminating unnecessary steps and simplifying workflows.
- Automation: Automating repetitive tasks to reduce manual effort and improve speed.
- Improved Training: Enhancing employee skills to reduce errors and increase efficiency.
- Technology Upgrades: Implementing new software or equipment to improve process speed.
- Better Resource Allocation: Optimizing resource allocation to prevent bottlenecks.
- Improved Communication: Enhancing communication and coordination among teams to reduce delays.
- Kaizen Events: Implementing continuous improvement initiatives to identify and address inefficiencies.
Cycle Time in Different Industries
Cycle time is relevant across numerous industries, each with its specific applications and challenges.
Manufacturing:
Cycle time in manufacturing represents the time it takes to produce a single unit of a product. Optimizing this metric is crucial for reducing production costs and meeting customer demand.
Software Development:
Cycle time in software development focuses on the time from the initiation of a task (e.g., bug fixing, feature development) to its completion. Faster cycle times lead to quicker software releases and faster response to customer needs.
Healthcare:
Cycle time in healthcare measures the time taken to complete specific processes, such as patient diagnosis, treatment, or discharge. Reducing cycle times can improve patient outcomes and reduce hospital stays.
Customer Service:
Cycle time in customer service represents the time it takes to resolve a customer issue. Shorter cycle times lead to improved customer satisfaction and loyalty.
Conclusion: Mastering Cycle Time for Enhanced Business Performance
Cycle time is a powerful metric for understanding and improving business processes. By employing appropriate methodologies for calculating and analyzing cycle time data, businesses can identify bottlenecks, streamline workflows, and ultimately enhance efficiency, productivity, and profitability. Remember that continuous monitoring and improvement are crucial for maintaining optimal cycle times and staying ahead in a competitive environment. The journey to mastering cycle time is an ongoing process of data analysis, process improvement, and a commitment to continuous optimization.
Latest Posts
Latest Posts
-
How Many Pints Are In 7 Cups
Apr 06, 2025
-
97 Months Is How Many Years
Apr 06, 2025
-
How Many Weeks Is 91 Days
Apr 06, 2025
-
Cubic Inches Per Gallon Of Water
Apr 06, 2025
-
15000 Feet Is How Many Miles
Apr 06, 2025
Related Post
Thank you for visiting our website which covers about How To Figure Out Cycle Time . We hope the information provided has been useful to you. Feel free to contact us if you have any questions or need further assistance. See you next time and don't miss to bookmark.