How To Find The Heat Transfer Coefficient
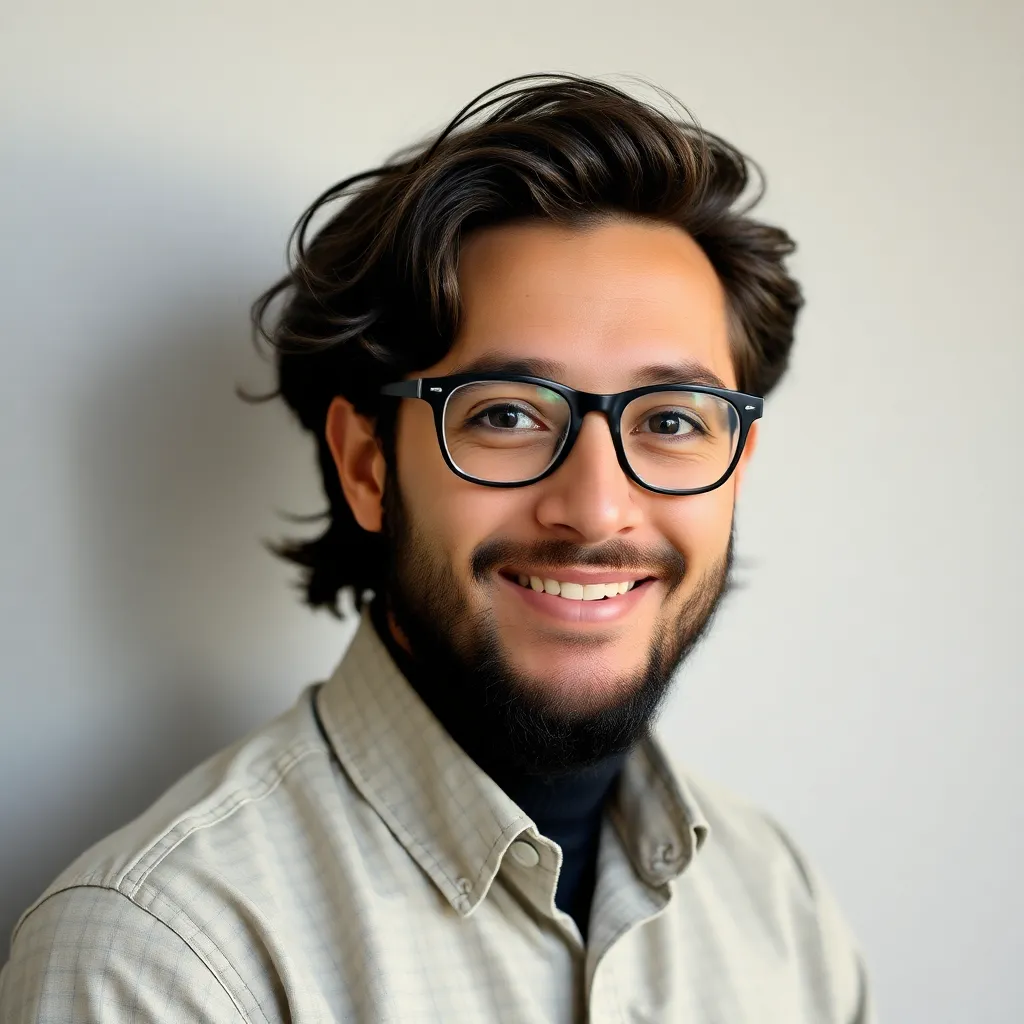
Treneri
Apr 26, 2025 · 6 min read

Table of Contents
How to Find the Heat Transfer Coefficient: A Comprehensive Guide
The heat transfer coefficient (h), a crucial parameter in thermal engineering, quantifies the rate of heat transfer between a surface and a fluid. Understanding how to determine this coefficient is essential for accurate design and analysis in various applications, from HVAC systems to chemical reactors. This comprehensive guide explores various methods for finding the heat transfer coefficient, ranging from empirical correlations to sophisticated computational techniques.
Understanding the Heat Transfer Coefficient
Before diving into the methods, let's solidify our understanding of the heat transfer coefficient. It's defined by Newton's Law of Cooling:
Q = hAΔT
Where:
- Q is the rate of heat transfer (Watts or BTU/hr)
- h is the heat transfer coefficient (W/m²K or BTU/hr·ft²·°F)
- A is the surface area (m² or ft²)
- ΔT is the temperature difference between the surface and the fluid (K or °F)
The heat transfer coefficient represents the ease with which heat flows between the surface and the fluid. A higher 'h' value indicates more efficient heat transfer. Factors influencing 'h' include:
- Fluid properties: Viscosity, thermal conductivity, specific heat capacity, and density.
- Flow characteristics: Laminar or turbulent flow, velocity, and flow geometry.
- Surface properties: Roughness, material, and the presence of any fouling.
Methods for Determining the Heat Transfer Coefficient
Determining the heat transfer coefficient involves a combination of theoretical analysis, experimental measurements, and empirical correlations. Here's a breakdown of the common approaches:
1. Empirical Correlations
Empirical correlations are equations derived from experimental data, providing a practical way to estimate 'h' for specific flow conditions and geometries. These correlations often involve dimensionless numbers like the Nusselt number (Nu), Reynolds number (Re), and Prandtl number (Pr).
Example: Forced Convection over a Flat Plate (Laminar Flow)
For laminar flow over a flat plate, a common correlation is:
Nu<sub>x</sub> = 0.332 Re<sub>x</sub><sup>0.5</sup> Pr<sup>1/3</sup>
Where:
- Nu<sub>x</sub> is the local Nusselt number at a distance 'x' from the leading edge.
- Re<sub>x</sub> is the local Reynolds number at 'x'.
- Pr is the Prandtl number of the fluid.
To obtain the average Nusselt number (Nu<sub>avg</sub>) over the entire plate length (L), the correlation is modified:
Nu<sub>avg</sub> = 0.664 Re<sub>L</sub><sup>0.5</sup> Pr<sup>1/3</sup>
This correlation requires calculating Re<sub>x</sub> and Re<sub>L</sub> using:
Re<sub>x</sub> = (ρVx)/μ and Re<sub>L</sub> = (ρVL)/μ
Where:
- ρ is the fluid density.
- V is the fluid velocity.
- x, L are the distances from the leading edge.
- μ is the dynamic viscosity of the fluid.
Once Nu<sub>avg</sub> is calculated, the average heat transfer coefficient (h<sub>avg</sub>) can be found using:
h<sub>avg</sub> = (Nu<sub>avg</sub> k)/L
Where 'k' is the thermal conductivity of the fluid.
Note: Numerous other correlations exist for different flow regimes (turbulent flow, natural convection, internal flow in pipes, etc.). Selecting the appropriate correlation is crucial and depends heavily on the specific application and conditions.
2. Computational Fluid Dynamics (CFD)
CFD is a powerful numerical technique used to solve the governing equations of fluid flow and heat transfer. Sophisticated software packages can simulate complex flow geometries and boundary conditions, yielding detailed temperature fields and heat transfer coefficients. CFD offers a significant advantage over empirical correlations when dealing with intricate geometries or complex flow patterns that are difficult to analyze analytically. However, CFD simulations require significant computational resources and expertise.
3. Experimental Measurement
Direct measurement of the heat transfer coefficient often involves setting up an experiment where heat is transferred from a heated surface to a fluid. By measuring the heat flux (Q/A) and the temperature difference (ΔT), the heat transfer coefficient can be determined using Newton's Law of Cooling.
Methods for Experimental Measurement Include:
- Transient methods: These involve heating or cooling a surface and monitoring its temperature change over time. By analyzing the temperature decay curve, the heat transfer coefficient can be extracted.
- Steady-state methods: These involve maintaining a constant temperature difference between the surface and the fluid and measuring the steady-state heat flux.
Challenges in Experimental Measurements:
- Ensuring accurate temperature measurement.
- Minimizing heat losses to the surroundings.
- Achieving well-defined flow conditions.
4. Analogical Methods
These approaches use analogies between heat transfer and other transport phenomena, like momentum transfer. For example, the Chilton-Colburn analogy relates the heat transfer coefficient to the friction factor, allowing for the estimation of 'h' based on knowledge of pressure drop. These methods are less accurate than direct measurement or CFD, but they can provide valuable estimations in situations where experimental data is scarce.
Factors Affecting Heat Transfer Coefficient Accuracy
Several factors can significantly influence the accuracy of the calculated or measured heat transfer coefficient:
- Fluid Properties: Accurate values of fluid properties (density, viscosity, thermal conductivity, specific heat) are crucial. These properties can vary with temperature and pressure, so accurate accounting for these variations is essential.
- Surface Conditions: Surface roughness, fouling, and the presence of any insulation can dramatically alter the heat transfer coefficient.
- Flow Conditions: The flow regime (laminar or turbulent) and the velocity profile significantly impact heat transfer. Inaccurate characterization of these conditions leads to errors in 'h'.
- Boundary Conditions: Correct specification of boundary conditions (temperature, heat flux) is vital. Incorrect boundary conditions can lead to inaccurate results.
Case Studies: Determining h in Different Scenarios
Let's consider a few scenarios to illustrate how to find the heat transfer coefficient using different methods:
Case Study 1: Air Cooling of an Electronic Component
For air cooling of an electronic component, empirical correlations for natural or forced convection are typically used. The geometry of the component and the airflow pattern will determine the specific correlation. The properties of air at the operating temperature would be needed, along with the surface area of the component and the temperature difference.
Case Study 2: Heat Transfer in a Pipe
For heat transfer in a pipe, correlations for internal flow are employed. The flow regime (laminar or turbulent), the fluid properties, the pipe diameter, and the length would be necessary for calculating the Nusselt number and, subsequently, the heat transfer coefficient. The Reynolds number is crucial in determining the flow regime.
Case Study 3: Condensate Film on a Vertical Plate
For condensation on a vertical plate, specific correlations for film condensation are used, considering the properties of the vapor and the condensate film. These correlations account for the effects of gravity and the properties of the condensed liquid.
Conclusion
Determining the heat transfer coefficient is a multifaceted problem. The choice of method depends on the specific application, the complexity of the system, and the available resources. Empirical correlations provide a relatively simple approach for common scenarios. CFD offers a powerful tool for tackling complex geometries and flow patterns. Experimental measurements provide direct data but can be challenging to implement accurately. Regardless of the chosen method, a thorough understanding of the underlying physical principles and careful attention to detail are critical for obtaining accurate and reliable results. Remember to always carefully choose the most appropriate correlation and consider the potential sources of error in your calculations or measurements to ensure the accuracy of your heat transfer coefficient determination.
Latest Posts
Latest Posts
-
What Is The Reciprocal Of 1 1 8
Apr 27, 2025
-
The Load Is The Pivot Point Of A Lever
Apr 27, 2025
-
Cuanto Son 16 Libras En Kilos
Apr 27, 2025
-
How Much Is 1 2 Tablespoon In Ml
Apr 27, 2025
-
11 3 4 Divided By 2
Apr 27, 2025
Related Post
Thank you for visiting our website which covers about How To Find The Heat Transfer Coefficient . We hope the information provided has been useful to you. Feel free to contact us if you have any questions or need further assistance. See you next time and don't miss to bookmark.