How To Measure Electric Motor Torque
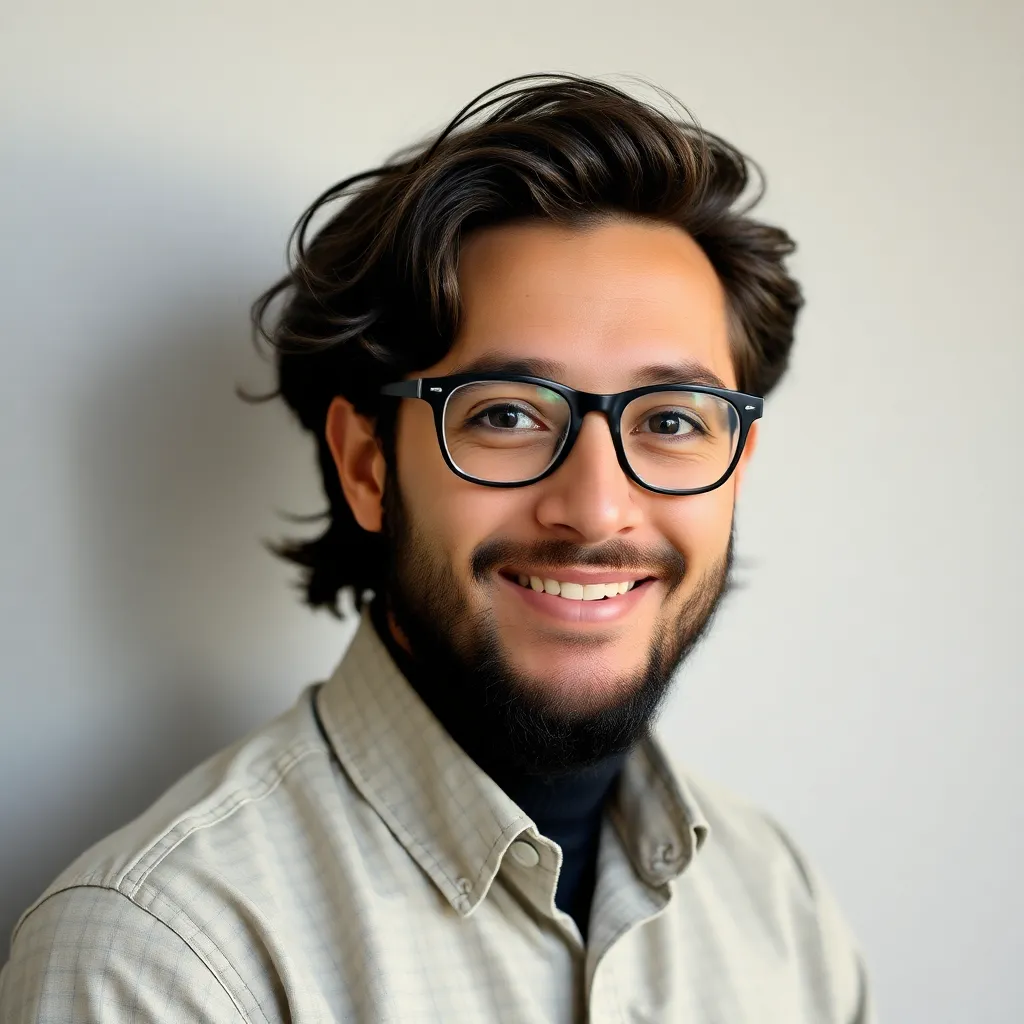
Treneri
May 12, 2025 · 5 min read
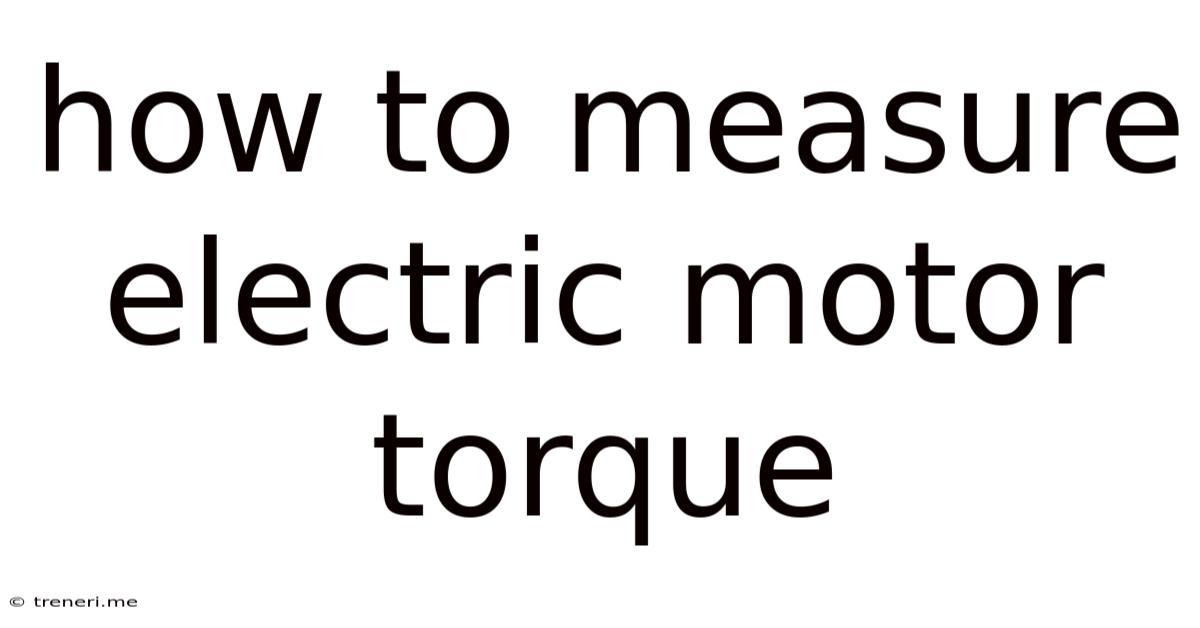
Table of Contents
How to Measure Electric Motor Torque: A Comprehensive Guide
Electric motors are the workhorses of countless applications, from powering industrial machinery to driving electric vehicles. Understanding and measuring their torque output is crucial for ensuring optimal performance, efficiency, and safety. This comprehensive guide delves into various methods for measuring electric motor torque, providing a detailed explanation of each technique and highlighting their advantages and limitations.
Understanding Torque
Before diving into measurement techniques, let's clarify what torque is. Torque, also known as moment of force, is the rotational equivalent of linear force. It represents the twisting force that causes rotation. In the context of electric motors, torque is the force that the motor applies to its shaft, causing it to rotate. It's measured in Newton-meters (Nm) or pound-feet (lb-ft). Higher torque means a greater ability to overcome resistance and accelerate a load.
Methods for Measuring Electric Motor Torque
Several methods exist for measuring the torque produced by an electric motor. The choice of method depends on factors like the motor's size, power rating, application, and the required accuracy.
1. Using a Torque Wrench
This is a straightforward method suitable for smaller motors and applications where high precision isn't paramount. A torque wrench is a specialized tool with a calibrated mechanism that measures the applied torque. The motor is connected to the torque wrench, and the wrench's reading indicates the torque being generated.
- Advantages: Simple, inexpensive, readily available.
- Disadvantages: Limited accuracy, suitable only for low-torque motors, relatively slow measurement process, prone to human error.
- Best for: Small DC motors, hobbyist projects, basic testing.
2. Strain Gauge-Based Torque Transducers
These transducers are sophisticated devices that utilize the principle of strain gauge technology. A strain gauge is a sensor that changes its electrical resistance when subjected to strain. When a torque is applied to the transducer's shaft, it deforms slightly, causing a change in the strain gauge's resistance. This change in resistance is proportional to the applied torque and is measured to determine the torque value.
- Advantages: High accuracy, wide torque range, suitable for various motor sizes, relatively fast measurement.
- Disadvantages: More expensive than torque wrenches, requires specialized equipment and expertise for calibration and data acquisition.
- Best for: Precise torque measurements, research and development, quality control in motor manufacturing.
3. Load Cell-Based Torque Measurement
Load cells are force sensors that measure the force applied to them. In torque measurement, a load cell is used to measure the force exerted by the motor on a lever arm. By knowing the length of the lever arm, the torque can be calculated using the formula: Torque = Force x Distance.
- Advantages: High accuracy, wide range of applications, robust and durable.
- Disadvantages: Requires careful setup and calibration, may require additional components (lever arm, support structure).
- Best for: High-torque applications, testing large industrial motors.
4. Dynamometer-Based Torque Measurement
A dynamometer, also known as a dyno, is a device used to measure the power and torque of rotating machinery, including electric motors. Dynamometers operate by applying a known opposing force to the motor shaft, thus measuring the torque required to overcome this force. There are various types of dynamometers, such as absorption dynamometers (which dissipate the motor's power as heat) and transmission dynamometers (which measure torque by sensing the force and distance).
- Advantages: High accuracy, wide range of applications, suitable for high-power motors, provides both torque and power measurements.
- Disadvantages: Expensive, requires significant space, may require specialized expertise to operate and maintain.
- Best for: Testing large industrial motors, automotive applications, motor performance testing.
5. Motor Current Measurement (Indirect Method)
This method uses the relationship between motor current and torque. For a given motor, there's a relatively consistent relationship between the current drawn and the torque produced. By accurately measuring the motor's current using a current clamp meter or data acquisition system, one can estimate the torque produced. This method requires a calibration curve that relates motor current to torque, which needs to be determined experimentally.
- Advantages: Inexpensive, relatively easy to implement, useful for real-time monitoring.
- Disadvantages: Less accurate than direct measurement techniques, heavily reliant on the accuracy of the calibration curve, influenced by various factors like motor temperature and voltage fluctuations.
- Best for: Rough estimations, real-time torque monitoring in applications where high precision isn't critical.
Factors Affecting Torque Measurement Accuracy
Several factors can affect the accuracy of torque measurement. These include:
- Calibration: Proper calibration of instruments is crucial for obtaining reliable results. Regular calibration ensures the accuracy of the measuring devices.
- Environmental factors: Temperature, humidity, and vibrations can influence the readings. Maintaining a stable environment is essential.
- Mechanical losses: Friction in the motor bearings and other mechanical components can introduce errors. Minimizing these losses is important.
- Instrumentation errors: Errors inherent in the measuring instruments can affect accuracy. Using high-quality instruments is recommended.
- Data acquisition: The method of data acquisition and analysis also plays a critical role. Using appropriate software and procedures ensures accurate results.
Choosing the Right Method
Selecting the appropriate torque measurement method depends on several factors:
- Motor size and power: For small motors, a torque wrench or strain gauge may suffice. Large motors often require dynamometers.
- Required accuracy: High-precision applications require dynamometers or strain gauge-based methods. Less precise applications may tolerate current measurement-based estimations.
- Budget: Torque wrenches are the most affordable, while dynamometers are the most expensive.
- Expertise: Some methods, such as dynamometer testing, require specialized expertise.
- Application: The specific application will dictate the suitable measurement method.
Conclusion
Measuring electric motor torque accurately is crucial for various applications. This guide has explored various methods, highlighting their strengths and weaknesses. By understanding the principles and limitations of each method, engineers and technicians can select the most appropriate technique to accurately assess the torque output of an electric motor and optimize its performance and efficiency. Remember to always prioritize safety when dealing with electrical machinery and follow proper safety procedures. Remember to always consult relevant safety guidelines and regulations when performing these measurements. Accurate and reliable torque measurements are essential for successful motor applications across all industries.
Latest Posts
Latest Posts
-
When Is The Best Uv To Tan
May 14, 2025
-
How Much Is 1 4 Ounce Of Yeast
May 14, 2025
-
How Much Does 500 Mcm Copper Weight Per Foot
May 14, 2025
-
What Is The Greatest Common Factor Of 28 And 70
May 14, 2025
-
60 Days From Oct 29 2024
May 14, 2025
Related Post
Thank you for visiting our website which covers about How To Measure Electric Motor Torque . We hope the information provided has been useful to you. Feel free to contact us if you have any questions or need further assistance. See you next time and don't miss to bookmark.