How To Work Out Tensile Stress
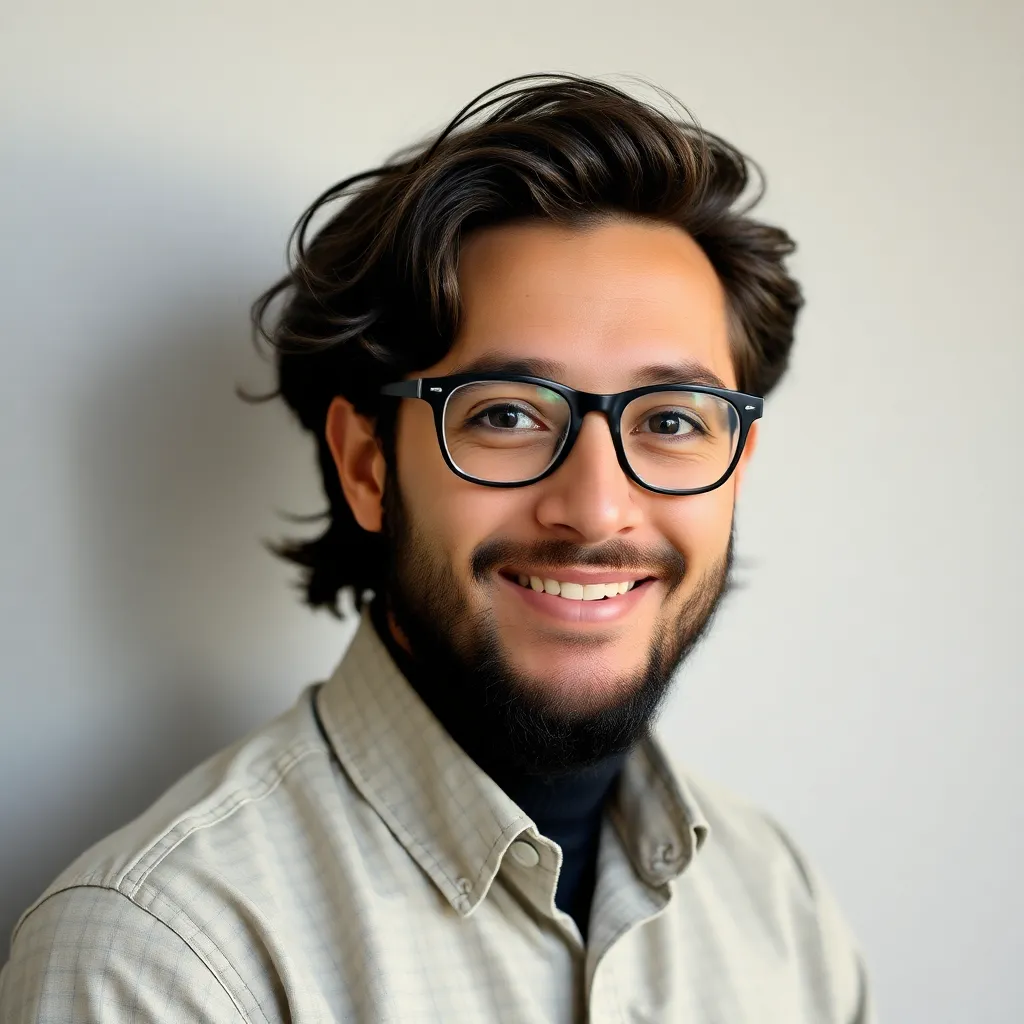
Treneri
May 11, 2025 · 6 min read
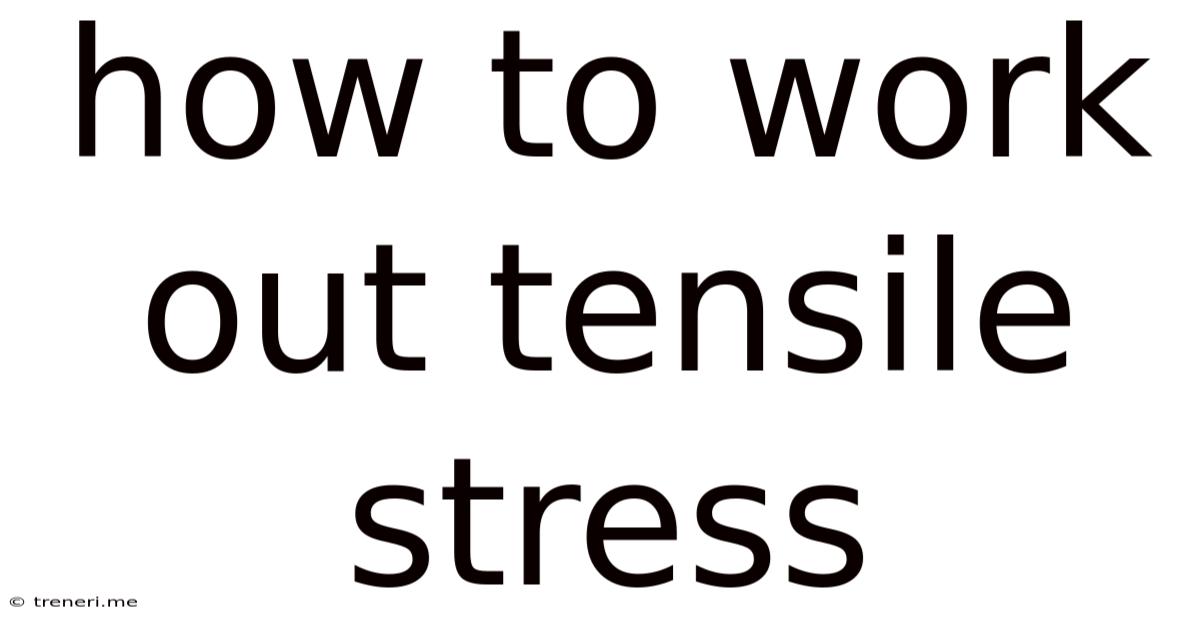
Table of Contents
How to Work Out Tensile Stress: A Comprehensive Guide
Tensile stress, a fundamental concept in materials science and engineering, represents the internal resistance of a material to being pulled apart. Understanding how to calculate and interpret tensile stress is crucial for designing safe and reliable structures and components. This comprehensive guide will walk you through the process, covering various aspects from basic definitions to advanced applications.
Understanding the Fundamentals: Defining Tensile Stress and Related Concepts
Before diving into calculations, let's solidify our understanding of key terms.
What is Tensile Stress?
Tensile stress (σ) is defined as the force (F) applied perpendicularly to a cross-sectional area (A) of a material, causing it to stretch or elongate. It's expressed mathematically as:
σ = F/A
Where:
- σ represents tensile stress (usually measured in Pascals (Pa), megapascals (MPa), or pounds per square inch (psi)).
- F represents the applied tensile force (usually measured in Newtons (N) or pounds (lb)).
- A represents the cross-sectional area perpendicular to the applied force (usually measured in square meters (m²) or square inches (in²)).
It's vital to note that this formula assumes a uniform stress distribution across the cross-sectional area. In real-world scenarios, stress distribution might be non-uniform, necessitating more complex analysis techniques.
Distinguishing Tensile Stress from Tensile Strain
While often used together, tensile stress and tensile strain are distinct concepts. Tensile strain (ε) represents the deformation of the material in response to the applied tensile stress. It's the ratio of the change in length (ΔL) to the original length (L₀):
ε = ΔL/L₀
Tensile strain is a dimensionless quantity. The relationship between stress and strain is described by the stress-strain curve, a crucial tool in material characterization.
Understanding Young's Modulus (Elastic Modulus)
Young's Modulus (E), also known as the elastic modulus, is a material property representing its stiffness or resistance to elastic deformation. It relates tensile stress and tensile strain within the elastic region of the material's behavior:
E = σ/ε
This means that a higher Young's Modulus indicates a stiffer material, requiring a greater stress to produce a given amount of strain. The elastic region is the portion of the stress-strain curve where the material returns to its original shape after the removal of the applied load.
Calculating Tensile Stress: A Step-by-Step Guide
Let's now delve into practical calculations, illustrating the process with different scenarios.
Scenario 1: Simple Tensile Test
Imagine a cylindrical steel bar with a diameter of 10 mm subjected to a tensile force of 10,000 N. To calculate the tensile stress:
-
Calculate the cross-sectional area: The cross-sectional area of a cylinder is given by A = πr², where r is the radius. The radius is half the diameter, so r = 5 mm = 0.005 m. Therefore, A = π(0.005 m)² ≈ 7.85 x 10⁻⁵ m².
-
Apply the tensile stress formula: σ = F/A = 10,000 N / 7.85 x 10⁻⁵ m² ≈ 127.3 MPa.
Therefore, the tensile stress in the steel bar is approximately 127.3 MPa.
Scenario 2: Non-Circular Cross-Sections
For materials with non-circular cross-sections (e.g., rectangular, square), calculating the area requires appropriate geometric formulas. For example, a rectangular bar with width (w) and thickness (t) has a cross-sectional area of A = w x t.
Scenario 3: Considering Units
Consistency in units is paramount. Ensure all measurements are in compatible units (e.g., meters for length, Newtons for force, etc.) before applying the formula to prevent errors. Conversion factors might be necessary if the initial measurements are in different units.
Advanced Considerations: Factors Affecting Tensile Stress
Several factors beyond the basic formula influence the actual tensile stress experienced by a material:
Stress Concentrations: Geometric Discontinuities
Sharp corners, holes, or changes in cross-sectional area can lead to stress concentrations, regions where the stress is significantly higher than the nominal stress (calculated using the basic formula). These concentrations can initiate crack formation and failure, even under relatively low loads. Finite element analysis (FEA) is often employed to model stress concentrations accurately.
Temperature Effects
Temperature significantly affects material properties, including strength and elasticity. High temperatures can reduce a material's strength, leading to lower tensile stress capacity. Conversely, extremely low temperatures can make materials brittle, increasing susceptibility to failure under tensile stress.
Material Imperfections: Defects and Microstructure
Internal defects such as voids, inclusions, or dislocations in the material's microstructure can act as stress concentrators, reducing its tensile strength. The material's processing history and composition also affect its microstructure and, consequently, its tensile strength.
Fatigue: Cyclic Loading
Repeated application of tensile stress (cyclic loading) can lead to fatigue failure, even at stress levels significantly below the material's ultimate tensile strength. Fatigue cracks usually initiate at stress concentrations and propagate gradually until failure occurs.
Creep: Time-Dependent Deformation
At high temperatures, materials can exhibit creep, a time-dependent deformation under constant stress. Creep can lead to gradual elongation and eventual failure of the material under sustained tensile loading.
Applications of Tensile Stress Calculations: Real-World Examples
The principles of tensile stress calculation are fundamental to numerous engineering applications.
Structural Engineering: Design of Bridges and Buildings
Understanding tensile stress is crucial for the safe design of bridges, buildings, and other structures. Engineers use tensile stress calculations to ensure structural components can withstand the anticipated loads without failing. Factors like wind load, seismic activity, and dead load (the weight of the structure itself) are considered during the design process.
Mechanical Engineering: Design of Machine Components
In mechanical engineering, tensile stress analysis is essential for designing machine components such as shafts, rods, and cables. Engineers must consider the forces these components are subjected to during operation to prevent failure. Fatigue analysis is often crucial for components experiencing cyclic loading.
Aerospace Engineering: Aircraft and Spacecraft Design
The aerospace industry relies heavily on tensile stress calculations for designing aircraft and spacecraft structures. These structures must withstand extreme loads during takeoff, flight, and landing, and materials need to exhibit high tensile strength and fatigue resistance.
Biomedical Engineering: Design of Implants and Medical Devices
Biomedical engineering utilizes tensile stress analysis for the design of implants, prosthetics, and other medical devices. These devices must be biocompatible, strong enough to withstand the forces they experience in the body, and durable enough for long-term use.
Conclusion: Mastering Tensile Stress Calculations
Understanding how to work out tensile stress is a cornerstone of engineering design and materials science. While the basic formula is straightforward, accurately predicting the behavior of real-world materials requires considering factors such as stress concentrations, temperature effects, material imperfections, fatigue, and creep. By mastering these concepts and employing appropriate analytical techniques, engineers can design safe, reliable, and efficient structures and components. Remember that consulting relevant material property data sheets and potentially employing advanced simulation techniques like FEA are vital for robust design in complex scenarios.
Latest Posts
Latest Posts
-
What Is The Least Common Multiple Of 3 And 11
May 11, 2025
-
How Many Yards Is 30 Inches
May 11, 2025
-
How Old Are People Born In 1974
May 11, 2025
-
How Much Time Till 10 15
May 11, 2025
-
How Many Lbs Of Soil In A Cubic Foot
May 11, 2025
Related Post
Thank you for visiting our website which covers about How To Work Out Tensile Stress . We hope the information provided has been useful to you. Feel free to contact us if you have any questions or need further assistance. See you next time and don't miss to bookmark.