Percent Elongation From Stress Strain Curve
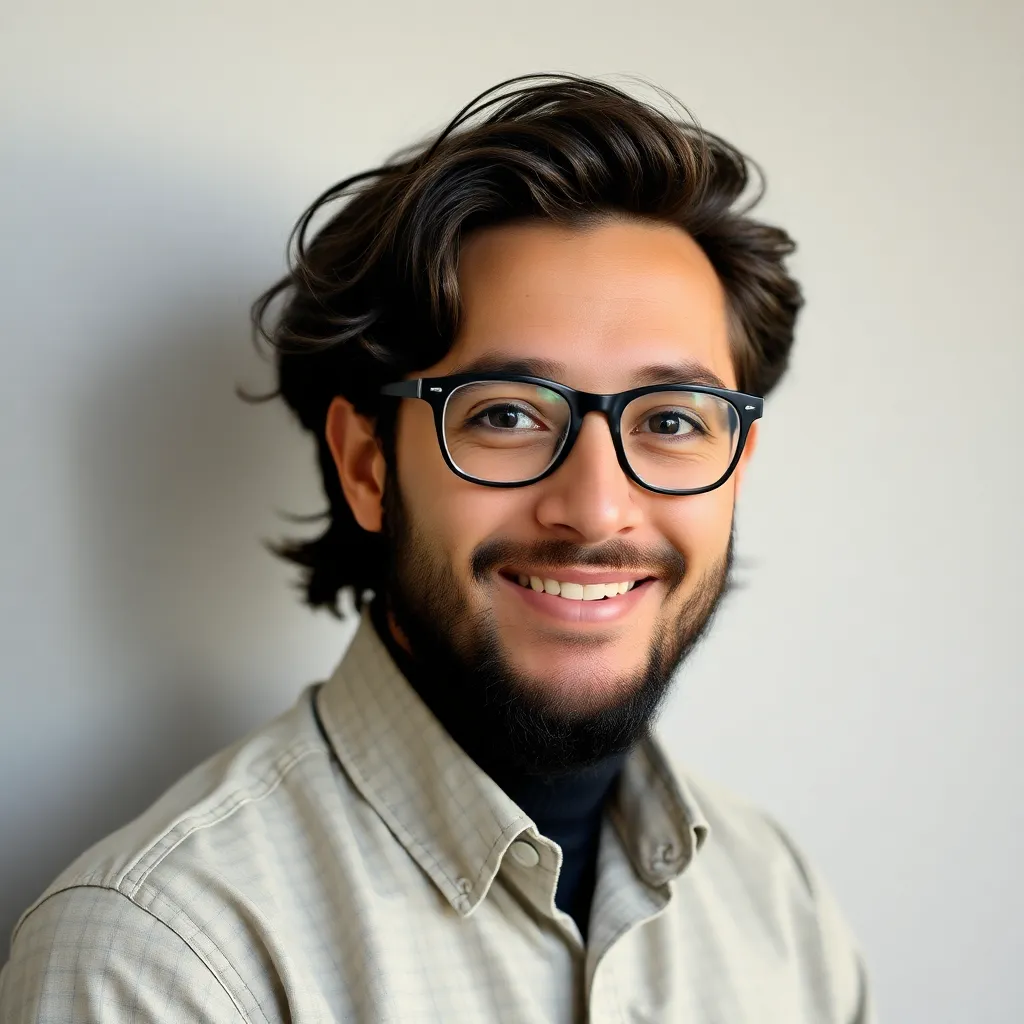
Treneri
May 12, 2025 · 6 min read
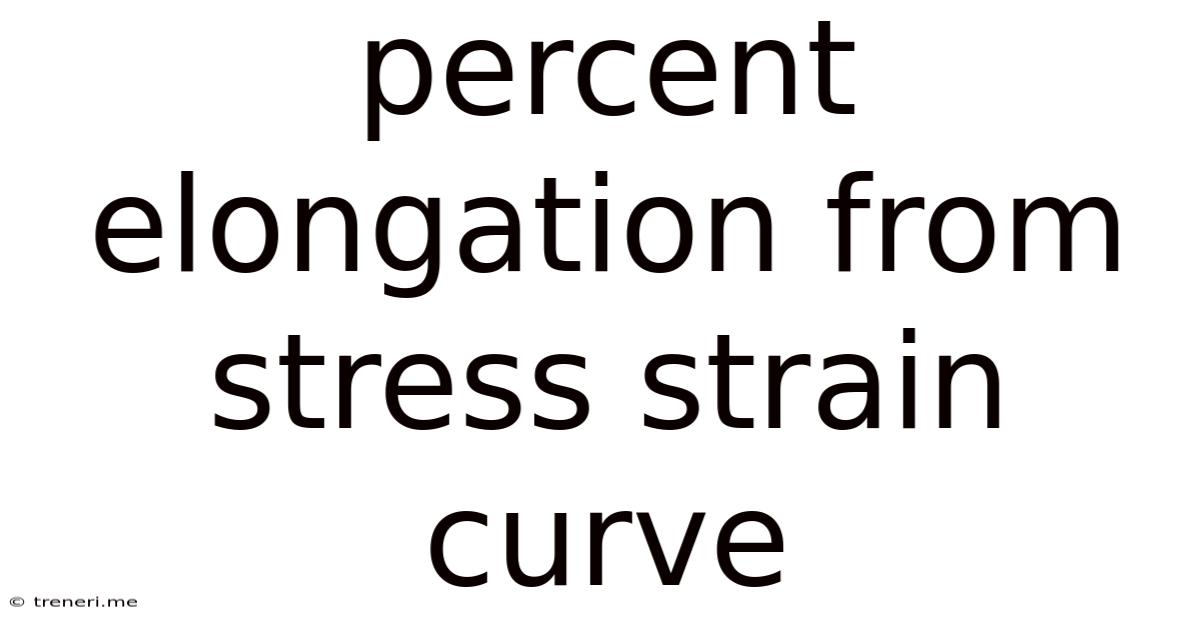
Table of Contents
Percent Elongation from Stress-Strain Curve: A Comprehensive Guide
Understanding material properties is crucial in engineering design. One critical parameter is percent elongation, a measure of a material's ductility derived from its stress-strain curve. This comprehensive guide delves into the intricacies of percent elongation, explaining its calculation, significance, and applications across various engineering disciplines. We'll explore different methods of determining percent elongation and discuss factors influencing this important material characteristic.
What is Percent Elongation?
Percent elongation, also known as elongation at break, is a material property that quantifies the degree to which a material can be stretched before fracturing. It represents the plastic deformation a material undergoes before failure, expressed as a percentage of its original length. A higher percent elongation indicates greater ductility – the material's ability to deform plastically under tensile stress before fracturing. Conversely, a lower percent elongation suggests a more brittle material, prone to fracture with minimal plastic deformation.
This property is vital in selecting suitable materials for applications where deformation under load is crucial or where impact resistance is a primary concern. For instance, designing car bodies requires materials with high percent elongation to absorb impact energy during collisions, minimizing damage and protecting occupants.
Ductility vs. Brittleness: A Crucial Distinction
The concept of percent elongation is intrinsically linked to the material's ductility and brittleness. Ductile materials exhibit significant plastic deformation before fracture, displaying a large percent elongation. Examples include mild steel, copper, and aluminum. Brittle materials, on the other hand, show minimal plastic deformation and fracture suddenly with low percent elongation. Ceramics, glass, and cast iron are classic examples of brittle materials.
The distinction between ductility and brittleness is critical in engineering design as it directly influences material selection and design considerations. Understanding percent elongation helps engineers predict a material's behavior under load and ensure the structural integrity of their designs.
Determining Percent Elongation from the Stress-Strain Curve
The stress-strain curve is a graphical representation of a material's response to applied tensile stress. It provides valuable insights into various material properties, including percent elongation. The curve typically shows stress (force per unit area) on the y-axis and strain (change in length per unit length) on the x-axis.
The process of determining percent elongation involves identifying key points on the stress-strain curve:
-
Yield Strength: The point where the material begins to deform plastically. This is often identified as the 0.2% offset yield strength.
-
Ultimate Tensile Strength (UTS): The maximum stress the material can withstand before necking (localization of deformation) begins.
-
Fracture Point: The point where the material fractures. This point marks the end of the stress-strain curve.
The percent elongation is calculated using the following formula:
Percent Elongation = [(Lf - Lo) / Lo] x 100
Where:
Lf
is the final length of the specimen at fracture.Lo
is the original gauge length of the specimen.
This calculation directly reflects the total elongation (plastic + elastic) divided by the original length, expressed as a percentage. It is important to note that the gauge length, the initial length of the material used for measurement, must be precisely defined and consistent throughout the testing procedure.
Importance of Gauge Length
The selection of the gauge length is critical in obtaining accurate and reproducible results. Standard gauge lengths are often specified in relevant testing standards (like ASTM standards), ensuring consistency across different experiments and laboratories. The gauge length significantly influences the measured percent elongation. A longer gauge length will generally yield a lower percent elongation compared to a shorter gauge length, as the total elongation is distributed over a longer distance.
Practical Considerations in Determining Percent Elongation
Obtaining an accurate percent elongation measurement requires careful consideration of several factors:
-
Specimen Preparation: Precise preparation of the test specimen is crucial. Any imperfections or irregularities can significantly influence the results.
-
Testing Machine Calibration: The testing machine used must be accurately calibrated to ensure precise measurements of force and elongation.
-
Environmental Conditions: Temperature and humidity can influence material behavior and impact the results.
-
Strain Rate: The rate at which the load is applied can affect the stress-strain curve and hence, the percent elongation. Consistent strain rates are necessary for reliable results.
Factors Influencing Percent Elongation
Several factors influence the percent elongation of a material:
-
Material Composition: The chemical composition of a material significantly impacts its ductility. Alloying elements can either increase or decrease percent elongation. For example, adding carbon to steel increases its strength but decreases its ductility.
-
Temperature: Temperature plays a significant role in material behavior. Generally, increasing temperature increases ductility and thus percent elongation, while decreasing temperature leads to decreased ductility and percent elongation.
-
Strain Rate: As mentioned previously, the rate at which the load is applied affects the material's response. Higher strain rates often result in lower percent elongation due to less time for plastic deformation.
-
Microstructure: The microstructure of the material, including grain size, precipitates, and defects, strongly influences its mechanical properties, including percent elongation. Finer grain sizes often exhibit higher ductility.
-
Processing Techniques: Manufacturing processes such as cold working can significantly impact the material's microstructure and consequently, its percent elongation. Cold working typically leads to decreased ductility and percent elongation.
-
Presence of Defects: Internal defects like voids or inclusions can act as stress concentrators, leading to premature fracture and lower percent elongation.
Applications of Percent Elongation Data
Percent elongation data is essential across numerous engineering disciplines:
-
Automotive Industry: Selecting materials for car bodies, bumpers, and other components requires materials with high percent elongation for impact absorption.
-
Aerospace Industry: Percent elongation is crucial for selecting materials for aircraft structures that must withstand fatigue and impact loads.
-
Biomedical Engineering: Materials for implants and medical devices must possess appropriate ductility and percent elongation to ensure compatibility and proper function.
-
Civil Engineering: Selecting materials for bridges, buildings, and other structures necessitates considering percent elongation for assessing the material's behavior under various loading conditions.
-
Manufacturing Processes: Percent elongation helps in designing and optimizing manufacturing processes such as drawing, rolling, and extrusion.
Advanced Considerations: Necking and its Impact on Percent Elongation
Necking is a phenomenon where the cross-sectional area of a specimen undergoing tensile testing begins to decrease significantly in a localized region before fracture. This localization of deformation influences the calculation and interpretation of percent elongation. The necking region experiences higher stresses, contributing to the eventual fracture. The presence and extent of necking affect the accuracy of the percent elongation measurement derived solely from the change in total length.
In materials exhibiting significant necking, the elongation in the necking region is often greater than the average elongation across the entire specimen. Therefore, solely relying on the total change in length might underestimate the true extent of ductility in the material. Advanced techniques, such as digital image correlation, can help capture the localized deformation during necking, offering more comprehensive analysis of material behavior.
Conclusion
Percent elongation is a vital material property that provides crucial insights into a material's ductility and its behavior under tensile loading. It's a key parameter in material selection for a wide range of engineering applications where deformation resistance and impact strength are vital. Accurate determination of percent elongation requires careful attention to experimental procedure and a thorough understanding of the factors that influence this material property. The integration of advanced techniques alongside conventional testing methods ensures a comprehensive evaluation of material behavior, leading to safer, more efficient, and reliable engineering designs. The stress-strain curve remains an invaluable tool for engineers seeking to understand and utilize the full potential of materials in a wide array of applications. Remember that consistently applying appropriate testing standards and paying attention to detail are paramount to obtaining reliable and repeatable results for percent elongation testing.
Latest Posts
Latest Posts
-
What Is The Gcf Of 42 And 48
May 13, 2025
-
104 Km Equals How Many Meters
May 13, 2025
-
Cuanto Falta Para 17 De Diciembre
May 13, 2025
-
How To Do Reconstitution Med Math
May 13, 2025
-
How Much Days Is A Million Seconds
May 13, 2025
Related Post
Thank you for visiting our website which covers about Percent Elongation From Stress Strain Curve . We hope the information provided has been useful to you. Feel free to contact us if you have any questions or need further assistance. See you next time and don't miss to bookmark.