Polar Moment Of Inertia For A Cylinder
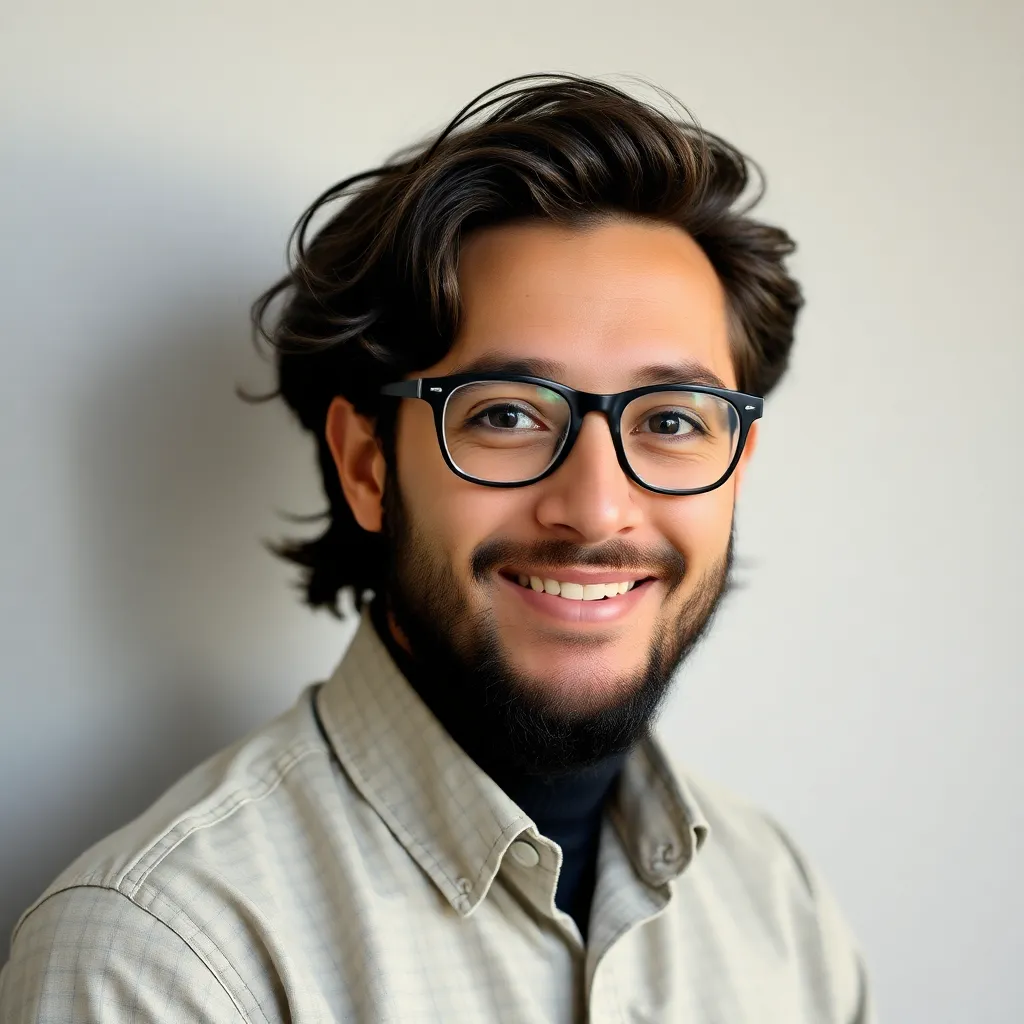
Treneri
May 13, 2025 · 6 min read
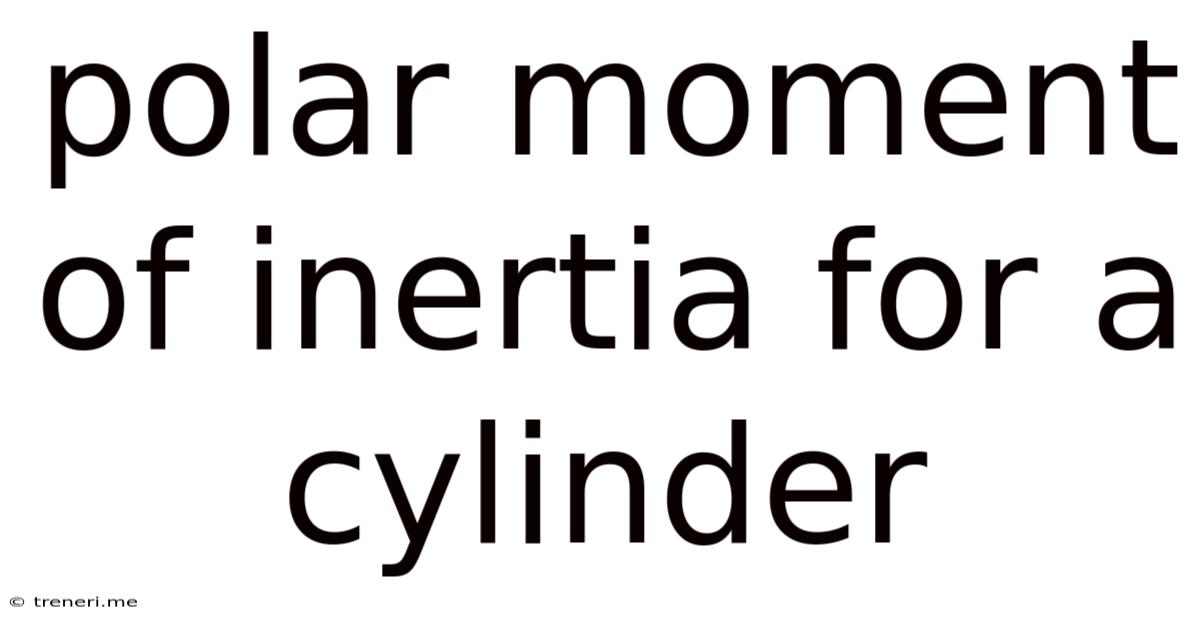
Table of Contents
Polar Moment of Inertia for a Cylinder: A Comprehensive Guide
The polar moment of inertia, often denoted as J or I<sub>p</sub>, is a crucial concept in engineering mechanics, particularly relevant when analyzing torsional stresses and rotational dynamics. This article delves deep into the calculation and application of the polar moment of inertia for a cylinder, a common shape encountered in various engineering disciplines. We'll explore different approaches, provide detailed derivations, and illustrate the significance of this parameter in real-world scenarios.
Understanding the Polar Moment of Inertia
The polar moment of inertia represents the resistance of a cross-sectional area to torsional deformation. Imagine trying to twist a cylindrical shaft. The greater the polar moment of inertia, the more resistant the shaft is to twisting. Unlike the area moment of inertia (I<sub>x</sub> and I<sub>y</sub>), which describe resistance to bending about the x and y axes respectively, the polar moment of inertia describes resistance to twisting about the z-axis (the axis perpendicular to the cross-section).
It's important to distinguish the polar moment of inertia from the area moment of inertia. While both relate to the geometry of a shape, they represent different aspects of its resistance to deformation under different types of loading. The area moment of inertia is relevant for bending, while the polar moment of inertia is relevant for torsion.
Calculating the Polar Moment of Inertia for a Solid Cylinder
For a solid cylinder of radius 'r' and length 'l', the polar moment of inertia can be calculated using the following formula:
J = (πr<sup>4</sup>)/2
This formula applies only to the cross-sectional area. The length of the cylinder doesn't affect the polar moment of inertia of the cross-section itself. However, the length does influence the overall torsional stiffness of the cylinder.
Derivation of the Formula
This formula is derived using integral calculus. We consider an infinitesimally small area element 'dA' within the circular cross-section of the cylinder. The distance of this element from the center of the circle is 'ρ'. The polar moment of inertia is then the sum (integral) of the product of this area element and the square of its distance from the center:
J = ∫ρ<sup>2</sup> dA
For a circular cross-section, we use polar coordinates:
dA = ρ dρ dθ
The integral becomes:
J = ∫(from θ=0 to 2π) ∫(from ρ=0 to r) ρ<sup>3</sup> dρ dθ
Solving this double integral gives us the familiar formula:
J = (πr<sup>4</sup>)/2
Calculating the Polar Moment of Inertia for a Hollow Cylinder
A hollow cylinder, also known as a cylindrical tube, has a different formula for its polar moment of inertia due to the absence of material in the central region. Let 'r<sub>o</sub>' be the outer radius and 'r<sub>i</sub>' be the inner radius. The polar moment of inertia for a hollow cylinder's cross-section is:
J = (π/2)(r<sub>o</sub><sup>4</sup> - r<sub>i</sub><sup>4</sup>)
Derivation for Hollow Cylinder
The derivation for a hollow cylinder follows a similar approach to the solid cylinder. We integrate over the annular region between the inner and outer radii:
J = ∫(from θ=0 to 2π) ∫(from ρ=r<sub>i</sub> to r<sub>o</sub>) ρ<sup>3</sup> dρ dθ
Solving this integral results in the formula mentioned above.
Applications of the Polar Moment of Inertia for Cylinders
The polar moment of inertia for a cylinder plays a vital role in several engineering applications:
1. Torsional Stress Analysis
In mechanical design, it's crucial to determine the maximum torsional stress (τ<sub>max</sub>) a cylindrical shaft can withstand before yielding or fracturing. The formula relating torsional stress, torque (T), polar moment of inertia, and radius is:
τ<sub>max</sub> = (Tr)/J
A higher polar moment of inertia results in a lower torsional stress for the same applied torque, indicating improved resistance to twisting.
2. Shaft Design
Engineers use the polar moment of inertia to design shafts for machinery and power transmission systems. By selecting materials with appropriate strength properties and ensuring the shaft's geometry (including its diameter and therefore its polar moment of inertia) is sufficient, they can guarantee that the shaft will withstand the expected torsional loads without failure.
3. Rotating Machinery
The polar moment of inertia is essential in analyzing the dynamics of rotating machinery such as motors, turbines, and flywheels. It determines the rotational inertia, resisting changes in rotational speed. A larger polar moment of inertia implies a greater resistance to changes in angular velocity, affecting the system's response to applied torques and influencing factors like startup time and braking performance.
4. Structural Engineering
In structural analysis, the polar moment of inertia is relevant for columns and shafts subjected to torsional loads. Understanding the torsional stiffness, which is directly proportional to the polar moment of inertia, is crucial in determining the structural stability and preventing failure under torsional stress.
5. Aerospace Engineering
Aerospace components, such as aircraft shafts and rotor blades, are often cylindrical or have cylindrical sections. Accurately calculating the polar moment of inertia is necessary for analyzing stress and ensuring structural integrity under flight conditions, including aerodynamic loads that can induce torsional stresses.
Factors Affecting Polar Moment of Inertia
Several factors influence the polar moment of inertia of a cylinder:
- Radius: The radius is the most significant factor. An increase in the radius dramatically increases the polar moment of inertia (proportional to r<sup>4</sup>).
- Material: While the material doesn't directly affect the formula, its density influences the mass moment of inertia, which is related to the polar moment of inertia through the material's density.
- Hollow vs. Solid: Hollow cylinders have a lower polar moment of inertia compared to solid cylinders of the same outer radius, making them lighter and potentially less resistant to torsion.
Beyond Simple Cylinders: More Complex Shapes
While this article focuses on solid and hollow cylinders, the concept of polar moment of inertia extends to other shapes. For complex geometries, numerical methods or advanced computational techniques are often used to determine the polar moment of inertia.
Conclusion
The polar moment of inertia for a cylinder is a fundamental concept with wide-ranging applications in various engineering fields. Understanding how to calculate it for different scenarios (solid vs. hollow cylinders) and its significance in determining torsional stress, rotational inertia, and overall structural integrity is essential for engineers and designers alike. The ability to accurately determine this value is critical in ensuring the safe and efficient operation of a wide variety of mechanical systems and structures. This knowledge allows engineers to design robust and reliable components that can withstand the expected loads and operate safely within their intended applications.
Latest Posts
Latest Posts
-
How To Find The Length Indicated
May 13, 2025
-
What Is The Factor Of 71
May 13, 2025
-
31 Km To Miles Per Hour
May 13, 2025
-
What Size Rug For 10x12 Room
May 13, 2025
-
How Many Days Is A 100 Hours
May 13, 2025
Related Post
Thank you for visiting our website which covers about Polar Moment Of Inertia For A Cylinder . We hope the information provided has been useful to you. Feel free to contact us if you have any questions or need further assistance. See you next time and don't miss to bookmark.