The General Rule For Finding The Proper Rivet Diameter Is
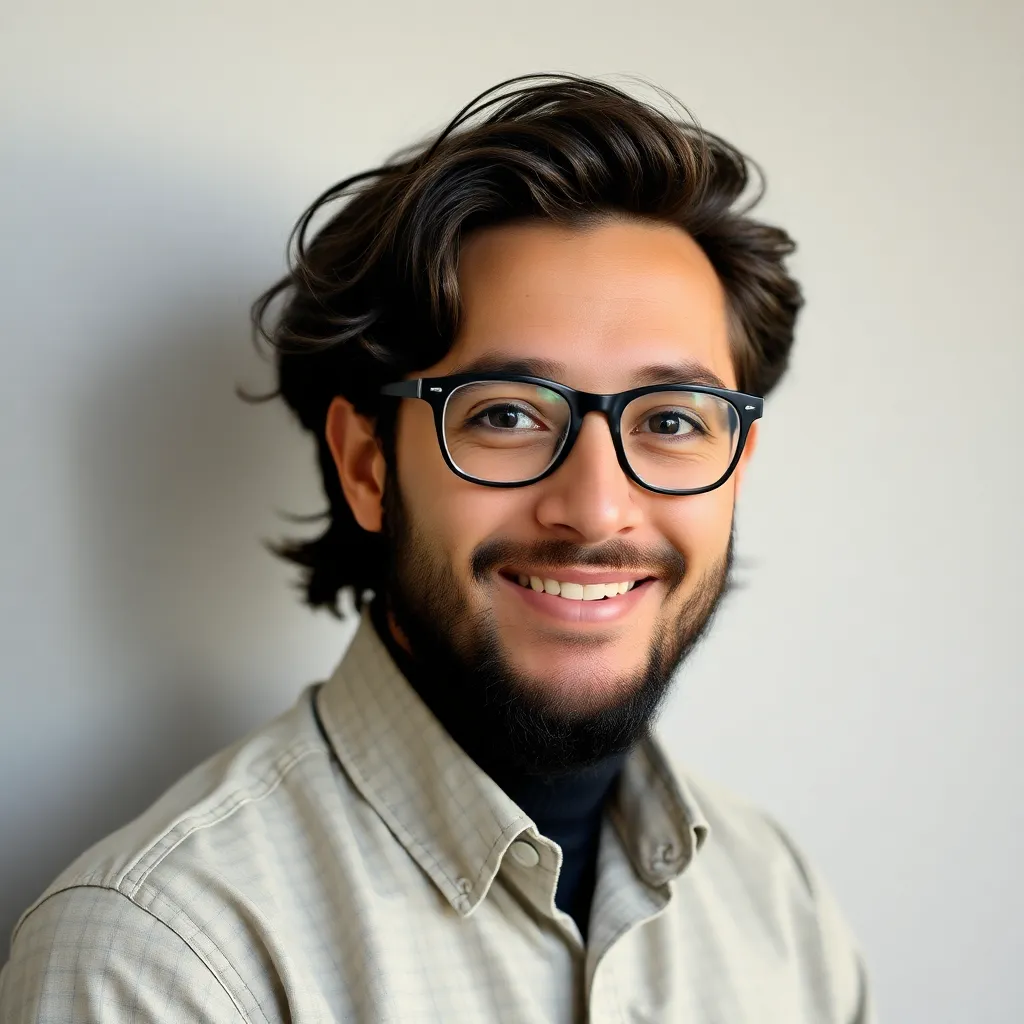
Treneri
May 14, 2025 · 6 min read
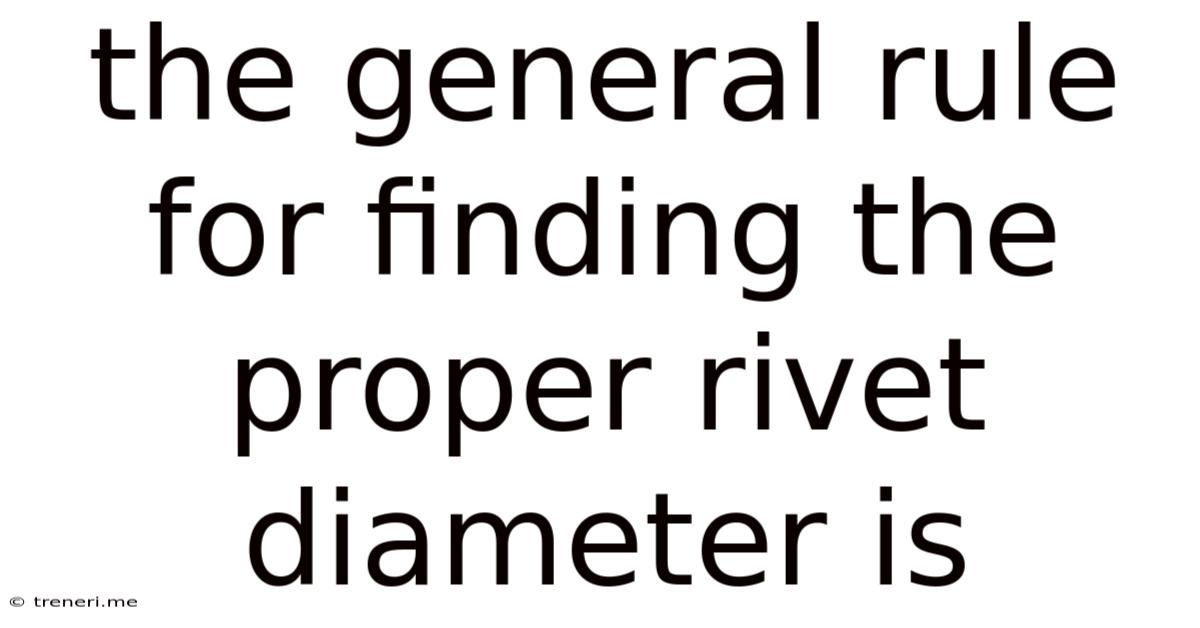
Table of Contents
The General Rule for Finding the Proper Rivet Diameter: A Comprehensive Guide
Choosing the right rivet diameter is crucial for ensuring the structural integrity and longevity of any riveted joint. A rivet that's too small will fail under stress, while one that's too large can damage the surrounding material or create an uneven joint. This comprehensive guide delves into the general rules and considerations for determining the appropriate rivet diameter for your specific application. We'll explore factors like material thickness, shear strength, and the type of rivet itself, providing you with the knowledge to confidently select the perfect rivet for your project.
Understanding the Key Factors Influencing Rivet Diameter Selection
Several critical factors influence the selection of the appropriate rivet diameter. Ignoring these can lead to joint failure and compromise the overall structural integrity of your project. These factors include:
1. Material Thickness: The Foundation of Your Calculation
The thickness of the materials being joined is the most fundamental factor in determining rivet diameter. Thicker materials generally require larger diameter rivets to provide sufficient clamping force and prevent shear failure. A general rule of thumb suggests a rivet diameter roughly equal to, or slightly less than, the thickness of the thickest material being fastened. However, this is a simplified guideline and should be further refined based on the other factors discussed below.
Example: If you are joining two pieces of metal, one 1/8" thick and the other 3/16" thick, your minimum rivet diameter should be around 3/16" (or 0.1875 inches).
2. Material Type and Strength: Beyond Thickness
The type of material being riveted also plays a crucial role. Different materials have varying strengths and tensile properties. Materials like stainless steel are considerably stronger than aluminum, necessitating a careful consideration of the rivet's shear strength capabilities relative to the material's tensile strength. Consult engineering handbooks or material datasheets to find the specific properties of your materials.
Consideration: A rivet suitable for joining mild steel might not be strong enough for joining high-strength aluminum alloys. Ensure the rivet material and its shear strength are appropriate for the materials being joined.
3. Shear Strength: Ensuring Joint Stability Under Load
Shear strength is the rivet's ability to resist forces that attempt to cut it in two. This is a paramount factor in determining the appropriate rivet diameter. A larger diameter rivet naturally offers greater shear strength due to its increased cross-sectional area. The chosen rivet must possess a shear strength exceeding the anticipated load on the joint, with a considerable safety factor included to account for unforeseen stresses.
Safety Factor: It's crucial to always incorporate a safety factor, typically ranging from 1.5 to 2.0, when calculating the required shear strength. This accounts for potential variations in material properties, manufacturing tolerances, and unforeseen loads.
4. Rivet Type and Material: A Wide Variety of Options
Different rivet types (solid, blind, semi-tubular) and materials (aluminum, steel, stainless steel) possess unique characteristics affecting their suitability for specific applications. Blind rivets are often used for applications where access to only one side of the joint is available. Solid rivets, requiring access to both sides, are generally stronger. Material choice impacts corrosion resistance and strength.
Example: Stainless steel rivets offer superior corrosion resistance compared to aluminum rivets but might be more expensive.
5. Joint Design and Configuration: The Bigger Picture
The overall design and configuration of the riveted joint also influence the rivet diameter selection. The number of rivets, their spacing, and the edge distance are important considerations. A poorly designed joint can lead to premature failure regardless of rivet diameter.
Best Practices: Proper spacing between rivets minimizes stress concentration. Sufficient edge distance prevents the rivet from pulling through the material's edge. Consult relevant design codes and standards for specific recommendations.
The General Rule and Its Refinements: Beyond the Simplified Approach
The often-quoted simplified rule of thumb – rivet diameter approximately equal to the material thickness – is a starting point, not a definitive answer. It provides a good initial estimate, especially for simple applications with relatively low loads. However, for critical applications, more sophisticated calculations are required.
Beyond the Simplified Rule: A More Accurate Approach
A more accurate approach involves considering the following:
- Determine the anticipated load on the joint: This requires careful analysis of the forces acting on the structure. Consider both static and dynamic loads.
- Calculate the required shear strength: Use the anticipated load and a suitable safety factor to determine the minimum shear strength needed.
- Consult rivet manufacturer's datasheets: These provide the shear strength values for different rivet sizes and materials.
- Select a rivet diameter that meets or exceeds the calculated shear strength: This ensures sufficient strength to withstand the expected loads.
- Verify the chosen rivet diameter: Ensure that it provides adequate grip length and avoids causing material damage during installation.
Detailed Example: Putting Theory into Practice
Let's consider a specific example. We're joining two 1/4-inch thick steel plates using solid steel rivets. The anticipated load on the joint is 5000 lbs. We'll assume a safety factor of 1.5.
-
Required Shear Strength: 5000 lbs * 1.5 = 7500 lbs. This is the minimum shear strength required from the rivet.
-
Rivets Datasheet: Consulting a rivet manufacturer's datasheet, we find that a 1/2-inch diameter steel rivet has a shear strength exceeding 7500 lbs.
-
Selection: A 1/2-inch diameter rivet would be suitable for this application.
-
Verification: We need to verify this choice. This includes ensuring sufficient grip length (the length of the rivet shank embedded in the materials) and checking for the possibility of material damage during installation.
Addressing Common Mistakes and Pitfalls
Several common mistakes can occur when choosing rivet diameter:
- Ignoring Material Properties: Failing to consider the material's strength and properties can lead to choosing a rivet that's too weak.
- Insufficient Shear Strength: Underestimating the required shear strength results in a rivet that may fail under load.
- Neglecting Safety Factor: Omitting a safety factor dramatically increases the risk of failure.
- Improper Joint Design: Poor joint design will compromise the strength regardless of rivet selection.
- Incorrect Installation: Improper installation techniques can reduce rivet strength and lead to premature failure.
Beyond Diameter: Other Critical Rivet Selection Considerations
Beyond diameter, other factors are crucial for selecting the proper rivet:
- Grip Length: The length of the rivet shank gripping the materials being joined. Insufficient grip length can lead to pull-through failure.
- Head Style: Different head styles (countersunk, button, pan) serve different aesthetic and functional purposes. Choose the style appropriate to your application.
- Material Compatibility: Ensure that the rivet material is compatible with the materials being joined to avoid galvanic corrosion.
Conclusion: A Precise Approach for Reliable Results
Selecting the correct rivet diameter is critical for structural integrity and longevity. While a simplified rule of thumb provides a starting point, a more precise approach considering material thickness, shear strength, and rivet type is essential for reliable results, particularly in critical applications. Always consult manufacturer datasheets, relevant design codes, and standards, and ensure a suitable safety factor is included to ensure the joint's safety and long-term performance. Remember, investing time in proper rivet selection prevents costly repairs and ensures the success of your project.
Latest Posts
Latest Posts
-
Cuantos Son 100 Mililitros En Onzas
May 14, 2025
-
What Is 7 Out Of 11
May 14, 2025
-
Time And A Half For 14 An Hour
May 14, 2025
-
Which Number Is A Perfect Square 33 37 48 49
May 14, 2025
-
Can You Tan In A Uv Of 5
May 14, 2025
Related Post
Thank you for visiting our website which covers about The General Rule For Finding The Proper Rivet Diameter Is . We hope the information provided has been useful to you. Feel free to contact us if you have any questions or need further assistance. See you next time and don't miss to bookmark.