Brinell Hardness To Rockwell Hardness Conversion
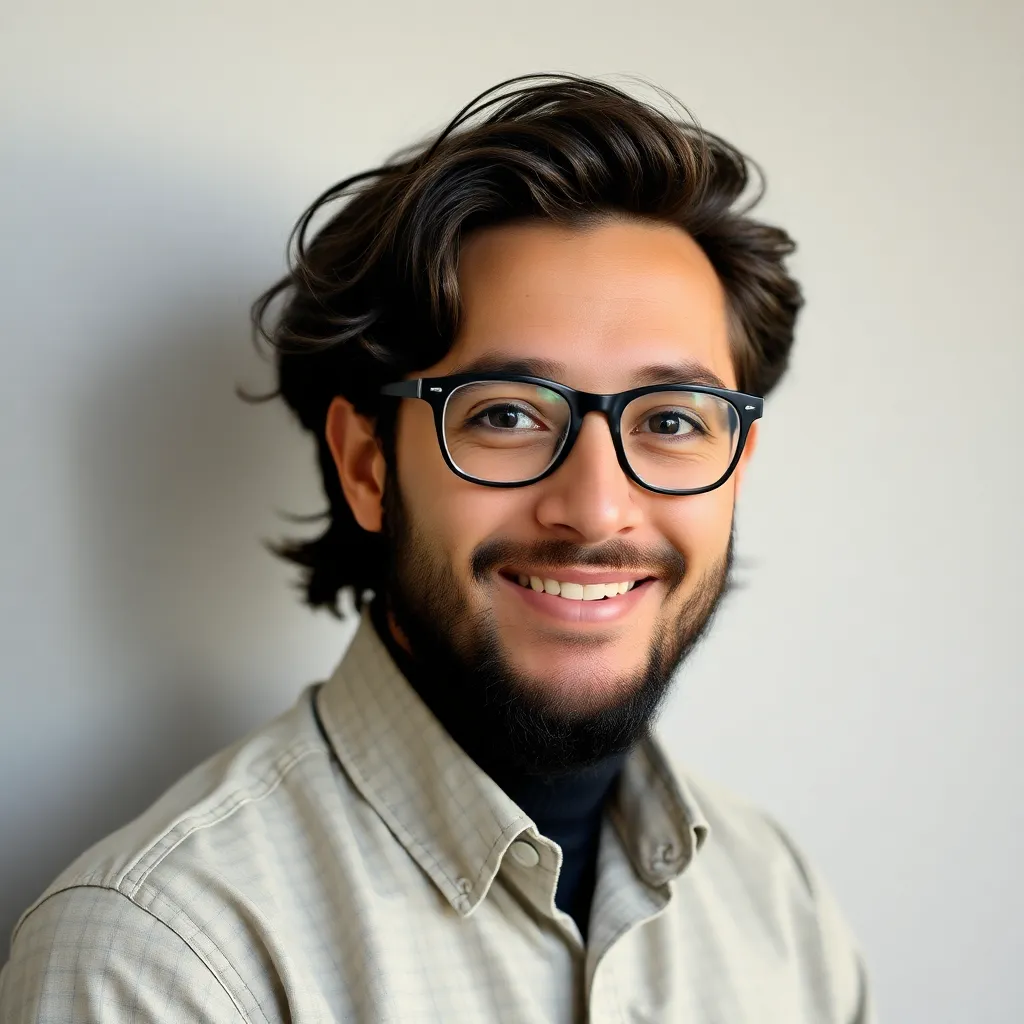
Treneri
Apr 05, 2025 · 5 min read
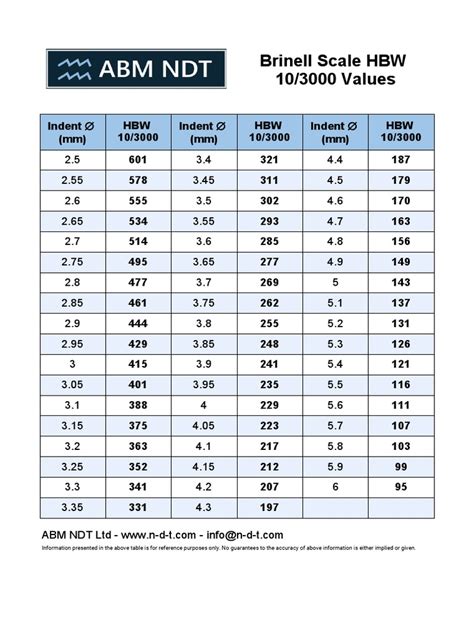
Table of Contents
Brinell Hardness to Rockwell Hardness Conversion: A Comprehensive Guide
Hardness testing is a crucial aspect of material science and engineering, providing valuable insights into a material's resistance to deformation. Two widely used hardness testing methods are Brinell and Rockwell. While both assess hardness, they differ significantly in their methodologies, resulting in different hardness scales. This comprehensive guide delves into the intricacies of Brinell and Rockwell hardness, explaining their differences, and exploring the challenges and methods involved in converting Brinell hardness numbers (HB) to Rockwell hardness numbers (HR).
Understanding Brinell Hardness Testing
The Brinell hardness test, developed by Johan August Brinell in 1900, is a relatively simple and widely accepted method for determining the hardness of a wide range of materials, from soft metals to harder alloys. The test involves indenting the material's surface with a hardened steel ball (typically 10mm diameter) under a standardized load (ranging from 500 kgf to 3000 kgf) for a specific dwell time (usually 10 to 15 seconds). The diameter of the resulting indentation is then measured using a calibrated microscope.
Key Parameters in Brinell Hardness Testing:
- Indenter: A hardened steel ball (most common) or carbide ball.
- Load: The force applied to the indenter (expressed in kilograms-force or kgf). Common loads include 500 kgf, 1500 kgf, and 3000 kgf.
- Dwell Time: The duration the load is applied. This is typically 10 to 15 seconds.
- Calculation: The Brinell Hardness Number (HB) is calculated using the formula: HB = 2P / (πD(D - √(D² - d²))), where P is the applied load, D is the diameter of the indenter, and d is the diameter of the indentation.
Advantages of Brinell Hardness Testing:
- Wide Applicability: Suitable for a broad range of materials, including soft metals, ferrous and non-ferrous alloys, and some non-metals.
- Relatively Simple: The test procedure is straightforward and requires minimal specialized equipment.
- Large Indentation: Provides a more representative average hardness value, reducing the influence of individual microstructural features.
Disadvantages of Brinell Hardness Testing:
- Larger Indentation Size: The relatively large indentation may not be suitable for small or thin specimens.
- Time-Consuming: Measuring the indentation diameter can be time-consuming, particularly for manual measurements.
- Surface Preparation: Requires a relatively smooth and flat surface for accurate results.
Understanding Rockwell Hardness Testing
The Rockwell hardness test, developed in the early 20th century, offers a faster and more convenient method for determining hardness. It utilizes a smaller indenter (either a diamond cone or a hardened steel ball) and measures the depth of penetration under different loads. The Rockwell hardness number is a direct reading from a dial gauge, eliminating the need for complex calculations.
Key Parameters in Rockwell Hardness Testing:
- Indenter: A diamond cone (for harder materials) or a hardened steel ball (for softer materials).
- Loads: Two loads are involved: a minor load (typically 10 kgf) and a major load (ranging from 60 kgf to 150 kgf).
- Scale: Several different Rockwell scales exist (e.g., Rockwell B, Rockwell C, Rockwell A) depending on the indenter and load combination.
- Measurement: The difference in depth of penetration between the minor and major load is used to calculate the Rockwell hardness number (HR).
Advantages of Rockwell Hardness Testing:
- Speed and Simplicity: Provides a direct reading, making it a rapid and efficient method.
- Smaller Indentation: Allows for testing of smaller components and thinner sections.
- Wide Range of Scales: Various scales cater to different material hardness ranges.
Disadvantages of Rockwell Hardness Testing:
- Less Representative: The smaller indentation may not always be representative of the average hardness of the material.
- Scale Dependency: The results are scale-specific and cannot be directly compared across different scales.
- Surface Sensitivity: Surface finish can have a more significant influence on Rockwell hardness measurements compared to Brinell.
The Challenges of Converting Brinell to Rockwell Hardness
Direct conversion between Brinell and Rockwell hardness values is inherently complex due to the fundamental differences in the testing methodologies. There's no single universal formula for accurate conversion because the relationship isn't linear and depends on several factors, including:
- Material type: Different materials exhibit different relationships between Brinell and Rockwell hardness.
- Specific Rockwell scale: The Rockwell scale used (e.g., B, C, A) significantly impacts the conversion.
- Testing conditions: Variations in load, dwell time, and surface preparation affect both Brinell and Rockwell measurements.
Methods for Approximate Brinell to Rockwell Conversion
While precise conversion is impossible without empirical data specific to the material, approximate conversion charts and formulas are available, offering reasonably accurate estimations for certain materials and Rockwell scales. These methods should be used with caution and are generally only suitable for preliminary estimations.
Conversion Charts:
Numerous conversion charts have been developed based on extensive experimental data for specific materials and Rockwell scales. These charts provide a graphical representation of the approximate relationship between Brinell and Rockwell hardness values. However, these charts are often limited in scope and may not be applicable to all materials or Rockwell scales.
Empirical Formulas:
Several empirical formulas have been proposed to approximate the conversion between Brinell and Rockwell hardness. These formulas are usually material-specific and often lack the accuracy of direct experimental data. They should be considered only as a rough estimate and should always be validated with experimental data if possible.
Using Material-Specific Data:
The most accurate approach is to use material-specific conversion data. If the material being tested has been previously characterized and conversion data exists, it is essential to utilize that information. Material datasheets or industry standards may offer this type of conversion data for specific materials.
Importance of Experimental Verification
Regardless of the chosen conversion method, it's crucial to understand that these methods provide approximations. To ensure accuracy, it's strongly recommended to conduct experimental hardness testing using the specific Rockwell scale needed. This will provide the most reliable and accurate hardness measurement for the material in question.
Conclusion: The Need for Precise Measurement
While approximate conversion methods exist, it is crucial to remember their limitations. The inherent differences in the Brinell and Rockwell hardness testing methods mean a direct, universally applicable conversion is not possible. The best approach is always to conduct the appropriate hardness test for the specific application and material. Relying solely on conversion charts or formulas may lead to inaccurate results and potential problems in material selection and quality control. Always prioritize precise measurement techniques to ensure material properties are accurately assessed. The accuracy of hardness data is paramount in engineering and manufacturing, preventing potential failures and ensuring product reliability. Understanding the nuances of hardness testing is therefore essential for successful material selection and quality control in various industries.
Latest Posts
Latest Posts
-
How Much Is 33 Kg In Pounds
Apr 05, 2025
-
How Much Is 14 5 Oz In Cups
Apr 05, 2025
-
Area Of A 13 14 15 Triangle
Apr 05, 2025
-
What Would A 9 12 Grade Be
Apr 05, 2025
-
How Long To Tan In 7 Uv
Apr 05, 2025
Related Post
Thank you for visiting our website which covers about Brinell Hardness To Rockwell Hardness Conversion . We hope the information provided has been useful to you. Feel free to contact us if you have any questions or need further assistance. See you next time and don't miss to bookmark.