Moment Of Inertia For A Tube
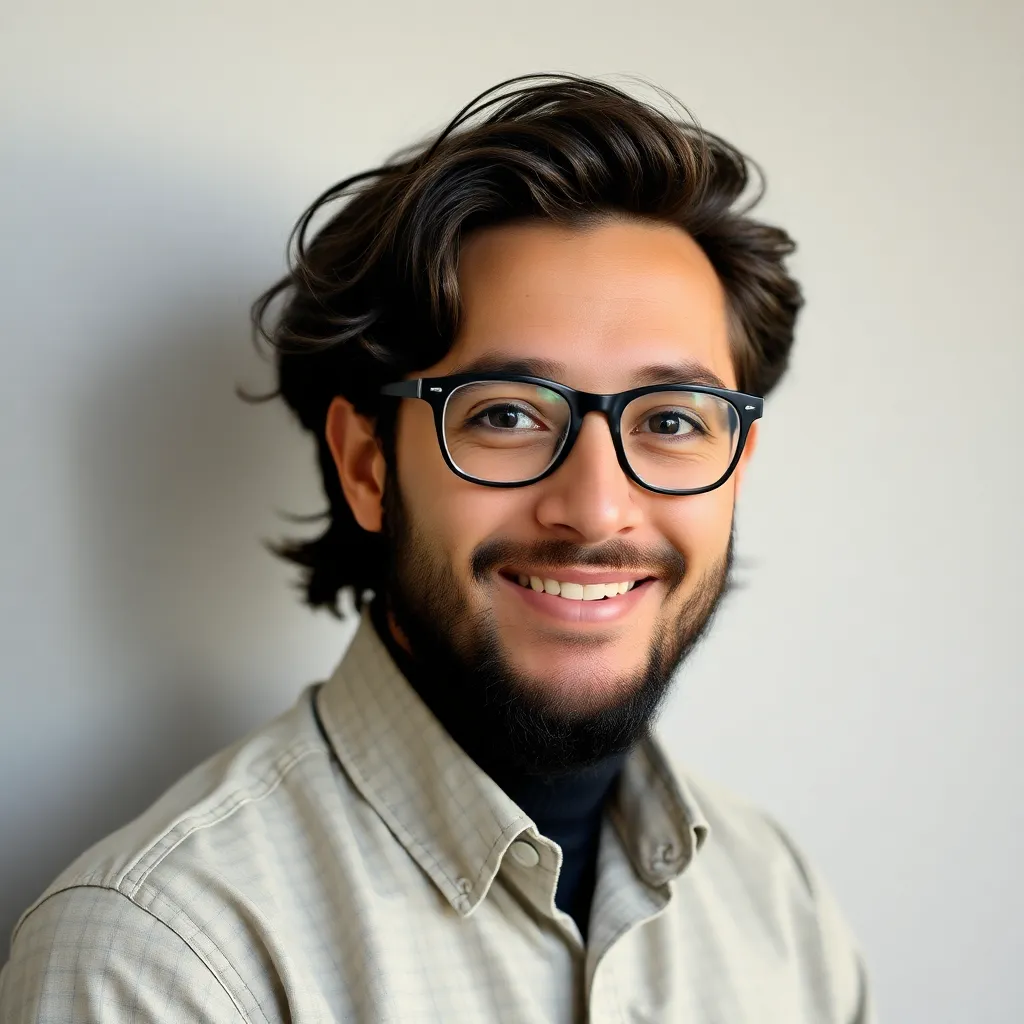
Treneri
May 13, 2025 · 6 min read

Table of Contents
Moment of Inertia for a Tube: A Comprehensive Guide
The moment of inertia, a crucial concept in physics and engineering, quantifies an object's resistance to changes in its rotation. Understanding this property is vital for analyzing the rotational motion of various objects, including tubes. This comprehensive guide delves into the calculation of the moment of inertia for a tube, considering different scenarios and providing practical applications.
Understanding Moment of Inertia
Before diving into the specifics of tubes, let's establish a fundamental understanding of moment of inertia. It's analogous to mass in linear motion; while mass resists changes in linear velocity, the moment of inertia resists changes in angular velocity. The greater the moment of inertia, the more difficult it is to accelerate or decelerate a rotating object.
The moment of inertia (I) depends on both the mass (m) of the object and the distribution of that mass relative to the axis of rotation. This distribution is crucial; a mass concentrated further from the axis of rotation contributes more significantly to the overall moment of inertia than the same mass closer to the axis.
Mathematically, the moment of inertia is calculated using integrals, summing the contributions of infinitesimal mass elements throughout the object. The general formula is:
I = ∫ r² dm
where:
- I is the moment of inertia
- r is the perpendicular distance from the mass element (dm) to the axis of rotation
- dm represents an infinitesimal mass element
Moment of Inertia for Different Tube Configurations
Calculating the moment of inertia for a tube depends heavily on its geometry and the axis of rotation. Let's explore several common scenarios:
1. Thin-Walled Hollow Cylinder (Tube) about its Central Axis
This is the simplest case. Imagine a thin cylindrical tube with a uniform mass distribution. The axis of rotation passes through the center of the tube, parallel to its length. Because the tube is thin-walled, we can approximate the mass as being concentrated at a single radius (R). In this case, the moment of inertia is relatively straightforward:
I = MR²
where:
- M is the total mass of the tube
- R is the radius of the tube
This formula is exceptionally useful for quick estimations, especially when dealing with tubes where the wall thickness is negligible compared to the radius.
2. Thick-Walled Hollow Cylinder (Tube) about its Central Axis
For a thick-walled tube, the simplification of a single radius is no longer valid. The mass is distributed across a range of radii. We need to consider the inner radius (Rᵢ) and the outer radius (Rₒ). The derivation involves integration, leading to the following formula:
I = ½M(Rₒ² + Rᵢ²)
where:
- M is the total mass of the tube
- Rₒ is the outer radius of the tube
- Rᵢ is the inner radius of the tube
This formula provides a more accurate representation of the moment of inertia for tubes with significant wall thickness. Note that when Rᵢ approaches zero, this equation converges to the moment of inertia of a solid cylinder.
3. Thin-Walled Hollow Cylinder (Tube) about an Axis Perpendicular to its Length
Consider now the scenario where the axis of rotation is perpendicular to the length of the tube and passes through its center. This is a more complex scenario, requiring a different approach to integration. The formula becomes:
I = ½MR² + ML²/12
where:
- M is the total mass of the tube
- R is the radius of the tube
- L is the length of the tube
This formula highlights the dependence of the moment of inertia on both the radius and the length of the tube. The first term reflects the rotational inertia due to the radial distribution of mass, while the second term accounts for the contribution of the tube's length.
4. Thick-Walled Hollow Cylinder (Tube) about an Axis Perpendicular to its Length
This is the most complex scenario. The integration becomes substantially more challenging, demanding a sophisticated understanding of calculus and multiple integrals. The resulting formula is significantly more involved and typically involves the inner and outer radii (Rᵢ and Rₒ), length (L), and total mass (M). Software packages like Mathematica or Maple are often utilized to perform these calculations effectively.
While a closed-form solution exists, its complexity renders it less practical for immediate applications. Numerical methods offer a viable alternative, especially when dealing with tubes of irregular shapes or varying density.
Practical Applications and Importance
The moment of inertia for tubes is crucial in various engineering and physics applications:
-
Mechanical Design: Designing rotating machinery, such as shafts, axles, and gears, relies heavily on understanding the moment of inertia. This allows engineers to predict torque requirements, rotational speeds, and potential stresses. Improper estimations could lead to component failure.
-
Robotics: In robotics, accurate calculation of the moment of inertia is critical for controlling the movement of robotic arms and manipulators. Precise control of rotational motion is essential for smooth and efficient operation.
-
Aerospace Engineering: The design of aircraft and spacecraft involves considering the moment of inertia of various components. This is vital for stability and control during flight. Understanding how the distribution of mass affects rotational motion is key to optimizing aircraft design.
-
Structural Analysis: Civil engineers use moment of inertia in the analysis of structural elements subject to torsion. Understanding how a structural member resists twisting forces is essential for ensuring stability and preventing failure.
-
Physics Experiments: In physics labs, the moment of inertia is a fundamental parameter in various experiments involving rotational motion, allowing students to verify theoretical calculations and gain hands-on experience with rotational dynamics.
Factors Affecting Moment of Inertia of a Tube
Several factors influence the moment of inertia of a tube:
-
Mass: A larger mass inherently leads to a larger moment of inertia, all other factors being equal.
-
Radius: Increasing the radius significantly increases the moment of inertia. This is because mass is distributed farther from the axis of rotation.
-
Wall Thickness: For thick-walled tubes, the moment of inertia is significantly higher than that of thin-walled tubes.
-
Material Density: Although less directly apparent, material density influences the moment of inertia by impacting the mass for a given volume. Denser materials will have a greater moment of inertia.
-
Axis of Rotation: The choice of axis of rotation drastically affects the moment of inertia. Calculations are significantly simpler when considering rotation about the central axis.
Conclusion
Calculating the moment of inertia for a tube involves understanding the tube's geometry and the axis of rotation. While simple formulas exist for thin-walled tubes about their central axes, more complex calculations are required for thick-walled tubes or different axes of rotation. Understanding moment of inertia is crucial for various engineering and physics applications, allowing for accurate prediction and control of rotational motion. Accurately determining this value is essential for designing robust and efficient systems, whether in mechanical engineering, robotics, or aerospace. Therefore, mastery of this concept is crucial for professionals in these fields.
Latest Posts
Latest Posts
-
How To Make A Huge Circle In Minecraft
May 13, 2025
-
800 Grams Cottage Cheese To Cups
May 13, 2025
-
Cuanto Es 2 Litros De Agua En Onzas
May 13, 2025
-
30 Days After October 31 2024
May 13, 2025
-
1000 Board Feet To Square Feet
May 13, 2025
Related Post
Thank you for visiting our website which covers about Moment Of Inertia For A Tube . We hope the information provided has been useful to you. Feel free to contact us if you have any questions or need further assistance. See you next time and don't miss to bookmark.