Pipe Diameter Calculation From Flow Rate
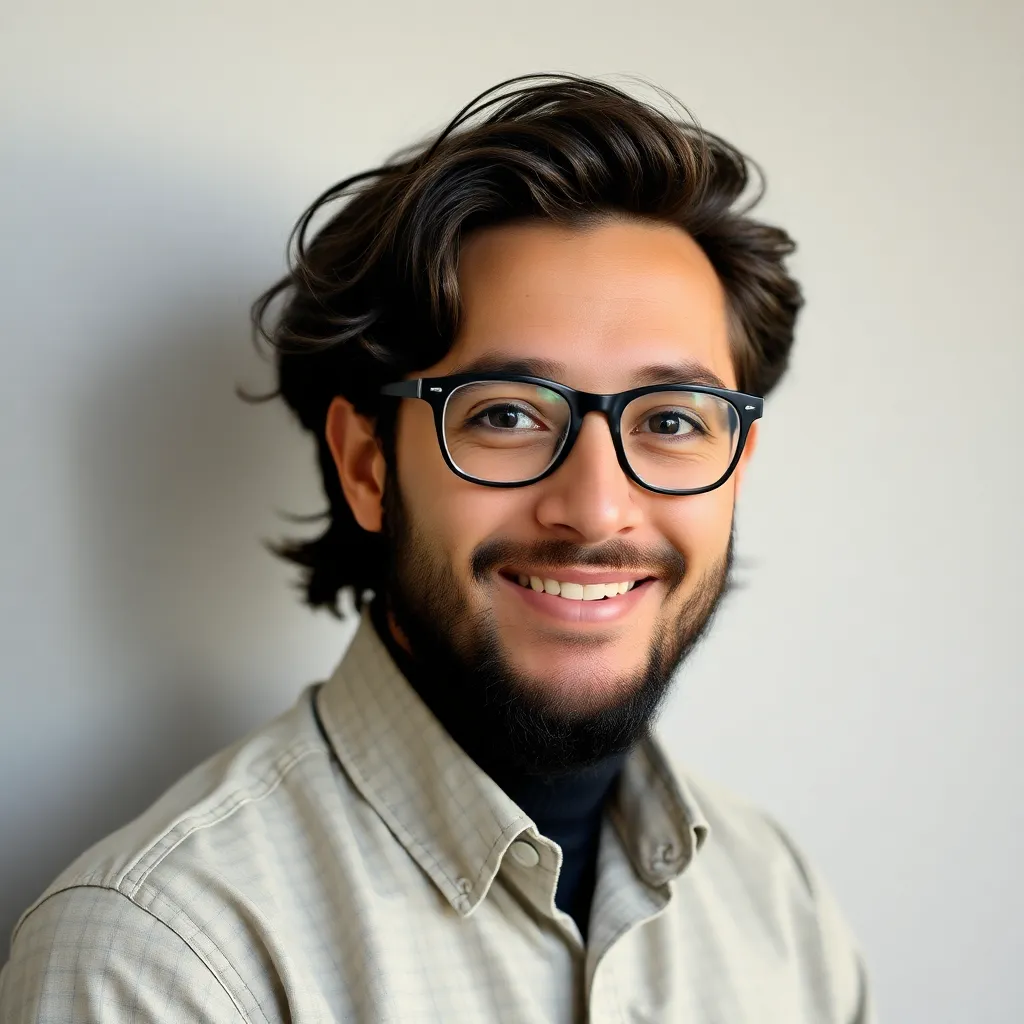
Treneri
May 13, 2025 · 6 min read
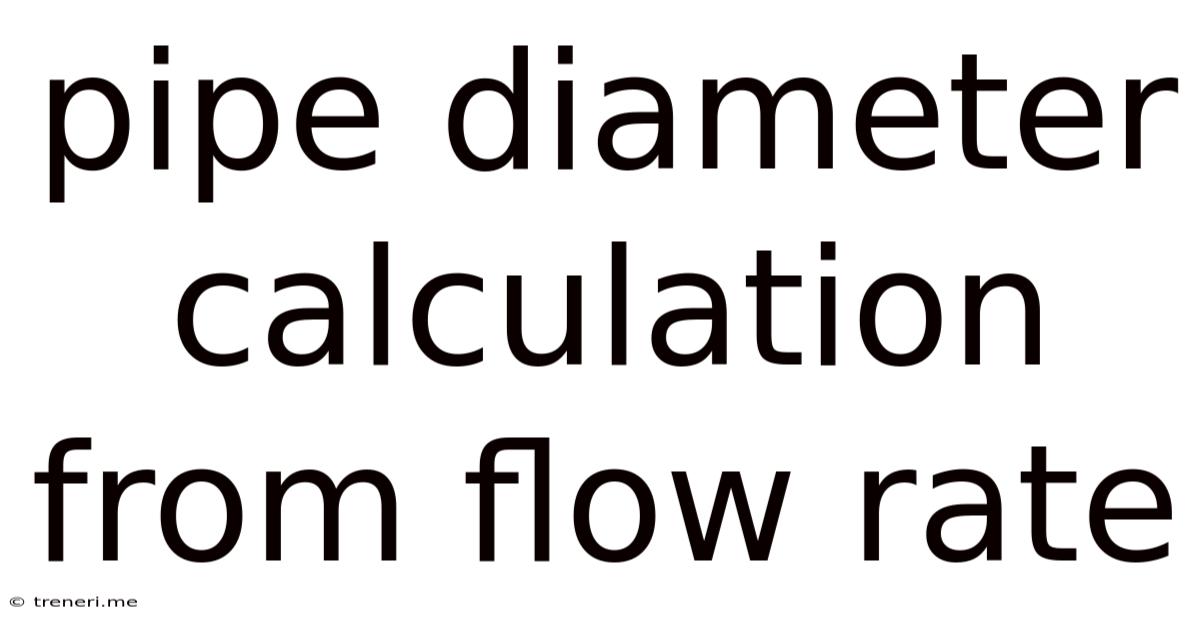
Table of Contents
Pipe Diameter Calculation from Flow Rate: A Comprehensive Guide
Determining the correct pipe diameter is crucial in various applications, from plumbing and irrigation to industrial processes and chemical engineering. An improperly sized pipe can lead to inefficient flow, excessive pressure drops, increased energy consumption, and even system failure. This comprehensive guide explores the methods and considerations involved in calculating pipe diameter based on the required flow rate. We'll delve into the fundamental equations, factors influencing pipe selection, and practical examples to ensure you can confidently tackle this critical engineering task.
Understanding the Fundamentals: Flow Rate and Pipe Diameter
Before diving into calculations, let's clarify the key terms:
-
Flow Rate (Q): This represents the volume of fluid passing a given point per unit of time. Common units include liters per second (L/s), gallons per minute (GPM), cubic meters per hour (m³/h), and cubic feet per second (cfs).
-
Pipe Diameter (D): This is the inside diameter of the pipe, typically expressed in inches (in), millimeters (mm), or centimeters (cm).
The relationship between flow rate and pipe diameter is not linear; it's governed by the principles of fluid dynamics, primarily through the Hazen-Williams equation and the Darcy-Weisbach equation. The choice of equation depends on the specific circumstances of the system.
The Hazen-Williams Equation: A Practical Approach
The Hazen-Williams equation is widely used for calculating pipe diameter based on flow rate, particularly in water distribution systems. It's empirically derived and relatively simple to use, making it a favorite for practical applications. The equation is:
Q = 0.849 * C * A * R<sup>0.63</sup> * S<sup>0.54</sup>
Where:
- Q: Flow rate (in desired units)
- C: Hazen-Williams roughness coefficient (dimensionless, depends on pipe material)
- A: Cross-sectional area of the pipe (πD²/4)
- R: Hydraulic radius (A/P, where P is the wetted perimeter; for a full pipe, R = D/4)
- S: Slope of the energy line (head loss per unit length)
Choosing the Hazen-Williams Coefficient (C):
The 'C' value depends heavily on the pipe material and its condition. Here's a table with approximate values:
Pipe Material | C (Hazen-Williams) |
---|---|
New cast iron | 130 |
Galvanized iron | 120 |
Wrought iron | 110 |
Concrete | 100 |
Asphalted cast iron | 140 |
PVC | 150 |
Plastic pipe (smooth) | 150-160 |
Limitations of the Hazen-Williams Equation:
- Accuracy: While practical, it's an empirical formula and less accurate than the Darcy-Weisbach equation, especially for non-circular pipes or turbulent flow conditions with high Reynolds numbers.
- Turbulent Flow Assumption: It's best suited for turbulent flow. For laminar flow, other equations are more appropriate.
- Specific to Water: While it can be adapted for other fluids, the accuracy diminishes.
The Darcy-Weisbach Equation: A More Accurate Approach
The Darcy-Weisbach equation offers greater accuracy and is applicable to a broader range of flow conditions. It directly incorporates the friction factor, making it suitable for various fluids and pipe materials. The equation is:
h<sub>f</sub> = f * (L/D) * (V²/2g)
Where:
- h<sub>f</sub>: Head loss due to friction (meters or feet)
- f: Darcy-Weisbach friction factor (dimensionless, depends on Reynolds number and pipe roughness)
- L: Pipe length (meters or feet)
- D: Pipe diameter (meters or feet)
- V: Flow velocity (m/s or ft/s) (V = Q/A)
- g: Acceleration due to gravity (9.81 m/s² or 32.2 ft/s²)
Determining the Friction Factor (f):
Calculating the friction factor (f) is the most challenging aspect of using the Darcy-Weisbach equation. It requires determining the Reynolds number (Re):
Re = (ρVD)/μ
Where:
- ρ: Fluid density (kg/m³ or lb/ft³)
- μ: Dynamic viscosity of the fluid (Pa·s or lb/ft·s)
Once the Reynolds number is known, the friction factor can be determined using the Moody chart or various empirical correlations like the Colebrook-White equation. The Colebrook-White equation is implicit and requires iterative solutions. Many online calculators and software packages provide assistance in this process.
Advantages of the Darcy-Weisbach Equation:
- Accuracy: More accurate than the Hazen-Williams equation, particularly for turbulent flow in rough pipes.
- Versatility: Applicable to a wider range of fluids, pipe materials, and flow conditions.
Limitations of the Darcy-Weisbach Equation:
- Complexity: Requires iterative solutions for friction factor calculation, making it more computationally intensive.
Choosing the Right Equation: Practical Considerations
The choice between the Hazen-Williams and Darcy-Weisbach equations depends on the specific application and desired accuracy.
-
For simple water distribution systems where high accuracy isn't critical: The Hazen-Williams equation offers a simpler, faster solution.
-
For situations requiring greater accuracy, particularly with non-Newtonian fluids, complex pipe geometries, or high pressure drops: The Darcy-Weisbach equation, though more complex, provides a superior result.
Factors Beyond Flow Rate: Influencing Pipe Diameter Selection
While flow rate is the primary driver in pipe diameter selection, several other factors must be considered:
-
Pressure Drop: Excessive pressure drop can lead to insufficient flow or system malfunction. The equations mentioned above help assess this, but other factors like elevation changes and fittings also contribute.
-
Velocity: High velocity can cause erosion and noise. Low velocity can promote sedimentation and bacterial growth. Optimum velocity ranges are usually specified for various applications.
-
Pipe Material: Material choice affects the roughness coefficient (C in Hazen-Williams) and friction factor (f in Darcy-Weisbach), impacting flow characteristics. Consider factors like corrosion resistance, cost, and temperature tolerance.
-
Future Expansion: Allow for potential future increases in flow rate when selecting pipe diameter. Oversizing can be more cost-effective in the long run than having to replace the piping later.
-
Cost: Larger diameter pipes are more expensive. Balancing cost with the long-term operational efficiency is crucial.
-
Installation Constraints: Consider the available space for pipe routing, accessibility for maintenance, and other site-specific limitations.
Practical Example using the Hazen-Williams Equation
Let's assume we need to design a water distribution pipeline with a required flow rate of 100 L/s. The pipe is made of new cast iron (C = 130), and the allowable head loss is 1 meter per 100 meters of pipe (S = 0.01).
-
Estimate the Diameter: We can start with an initial guess for the diameter and iterate. Let's assume D = 200 mm (0.2 m).
-
Calculate the Cross-sectional Area (A): A = πD²/4 = π(0.2)²/4 ≈ 0.0314 m²
-
Calculate the Hydraulic Radius (R): R = D/4 = 0.2/4 = 0.05 m
-
Apply the Hazen-Williams Equation: Q = 0.849 * C * A * R<sup>0.63</sup> * S<sup>0.54</sup> = 0.849 * 130 * 0.0314 * 0.05<sup>0.63</sup> * 0.01<sup>0.54</sup> ≈ 0.086 m³/s (86 L/s)
-
Iterate: Since our calculated Q (86 L/s) is less than the required 100 L/s, we need to increase the diameter and repeat the calculation. This iterative process continues until a diameter that satisfies the flow requirement is found. This often involves using a spreadsheet program or specialized software.
Conclusion
Calculating pipe diameter from flow rate is a crucial aspect of many engineering and design tasks. While both the Hazen-Williams and Darcy-Weisbach equations provide solutions, the latter offers superior accuracy, particularly for complex scenarios. Remember to consider factors beyond just flow rate, such as pressure drop, velocity, material selection, and cost-effectiveness, to ensure a robust and efficient system. Utilizing engineering software and iterative calculations often proves necessary for achieving optimal pipe sizing. This comprehensive guide provides the foundational knowledge and tools to confidently approach these calculations and design effective piping systems.
Latest Posts
Latest Posts
-
Best Uv Index To Tan Outside
May 13, 2025
-
What Is The Greatest Common Factor Of 77 And 55
May 13, 2025
-
What Is A Common Denominator For 6 7 And 3 5
May 13, 2025
-
Cuanto Es 130 Cm En Pulgadas
May 13, 2025
-
1 Ton Equal To How Many Btu
May 13, 2025
Related Post
Thank you for visiting our website which covers about Pipe Diameter Calculation From Flow Rate . We hope the information provided has been useful to you. Feel free to contact us if you have any questions or need further assistance. See you next time and don't miss to bookmark.