True Stress And True Strain Formula
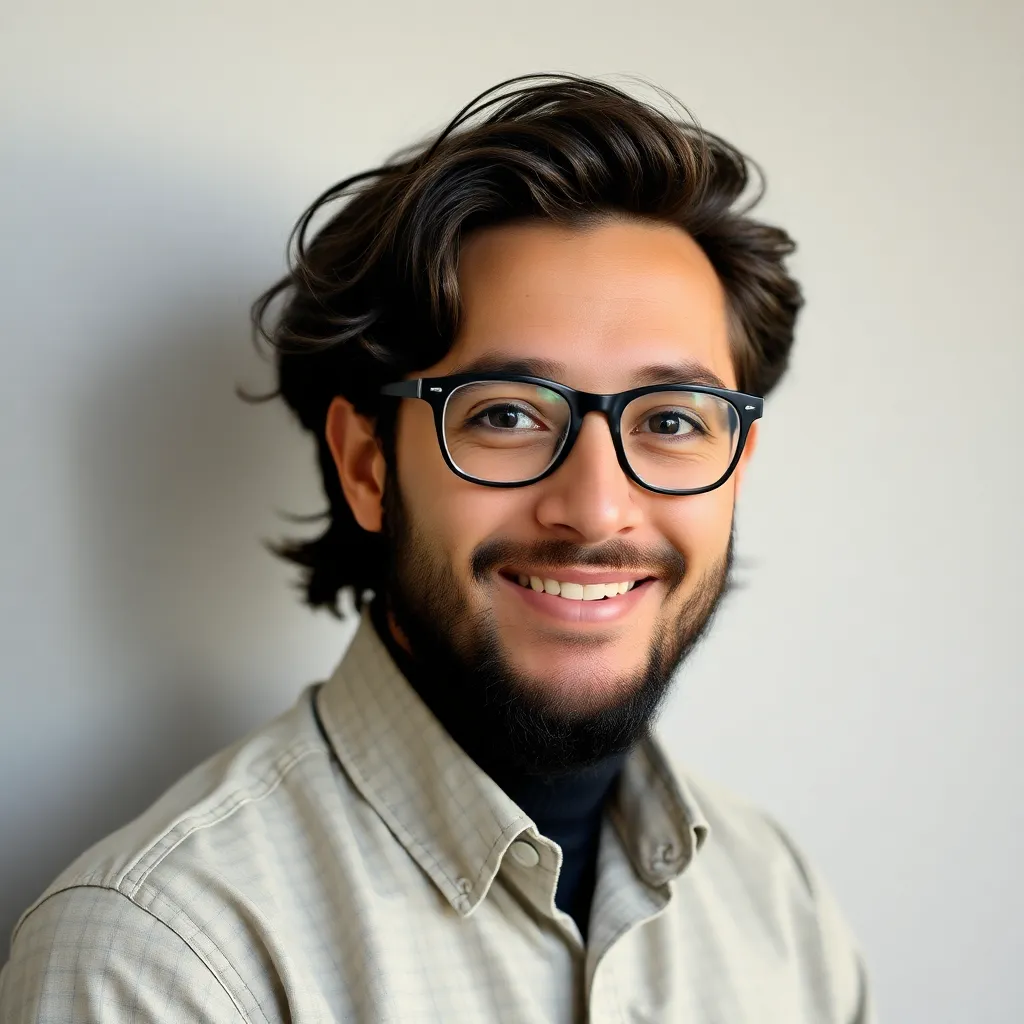
Treneri
May 10, 2025 · 6 min read
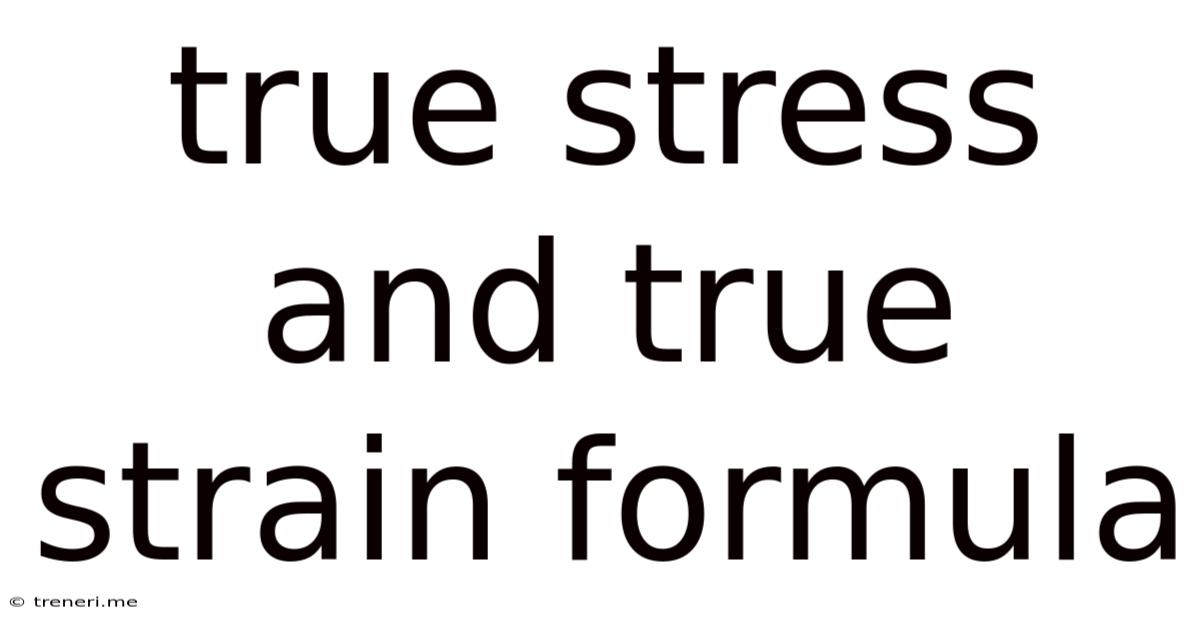
Table of Contents
True Stress and True Strain Formula: A Comprehensive Guide
Understanding true stress and true strain is crucial in materials science and engineering, particularly when dealing with the plastic deformation of materials. Unlike engineering stress and strain, which are based on the original dimensions of a specimen, true stress and strain account for changes in cross-sectional area and length during deformation. This distinction is critical for accurately predicting material behavior under significant loading conditions. This comprehensive guide delves into the formulas for true stress and true strain, their significance, and how they differ from their engineering counterparts.
Defining Engineering Stress and Strain
Before diving into true stress and strain, let's briefly review their engineering counterparts. Engineering stress (σ) is defined as the force (F) applied to a material divided by its original cross-sectional area (A₀):
σ = F/A₀
Engineering strain (ε) is the change in length (ΔL) divided by the original length (L₀):
ε = ΔL/L₀
These definitions are straightforward and easy to calculate, but they become less accurate as deformation progresses, particularly in the plastic region where significant changes in the material's geometry occur. The limitations of these values become apparent when considering necking, a phenomenon where localized deformation reduces the cross-sectional area of a specimen dramatically.
The Importance of True Stress and True Strain
The limitations of engineering stress and strain become apparent during necking. As the material necks, the cross-sectional area decreases significantly while the force continues to increase. Using engineering stress would erroneously suggest that the material is weakening, even though it's actually becoming stronger. This is where true stress and true strain become indispensable.
True stress and strain consider the instantaneous values of the cross-sectional area and length during deformation. This allows for a more accurate representation of the material's behavior, particularly in the plastic region. Accurate calculations are vital in predicting material behavior under severe loading. This is important for designing safe and reliable structures and components, especially those subjected to significant forces.
Deriving the True Stress Formula
The formula for true stress (σ<sub>t</sub>) takes into account the instantaneous cross-sectional area (A) during deformation:
σ<sub>t</sub> = F/A
To relate true stress to engineering stress, we must consider the volume constancy assumption during plastic deformation. This assumes that the volume of the material remains constant despite changes in shape. Mathematically, this is expressed as:
A₀L₀ = AL
Solving for A, we get:
A = A₀L₀/L
Substituting this into the true stress equation, we obtain:
σ<sub>t</sub> = (F/A₀) (L/L₀) = σ(1 + ε)
This equation demonstrates that true stress is always greater than engineering stress, particularly at higher levels of deformation.
Deriving the True Strain Formula
Unlike engineering strain, which is a simple ratio, true strain (ε<sub>t</sub>) is defined as the integral of the change in length over the instantaneous length:
ε<sub>t</sub> = ∫(dL/L)
Integrating this equation, we get:
ε<sub>t</sub> = ln(L/L₀) = ln(1 + ε)
This logarithmic relationship reflects the cumulative change in length throughout the deformation process. This is a key distinction from engineering strain, which simply represents the overall change in length relative to the initial length. The logarithmic nature accurately reflects the incremental changes that occur during deformation.
Relating True Stress and True Strain: The Flow Curve
The relationship between true stress and true strain is often represented by a flow curve. This curve is a crucial material property that describes the material's resistance to deformation at different strain levels. It's empirically determined through tensile testing. The flow curve is often described by a power law equation:
σ<sub>t</sub> = Kε<sub>t</sub><sup>n</sup>
where:
- K is the strength coefficient, a material constant representing the material's strength.
- n is the strain-hardening exponent, another material constant that indicates the rate at which the material strengthens with increasing deformation.
The values of K and n are material-specific and are determined experimentally. The flow curve is essential for predicting the material's behavior under various loading conditions.
Comparing True and Engineering Stress-Strain Curves
The difference between engineering and true stress-strain curves is significant, especially in the plastic region. The engineering stress-strain curve typically shows a decrease in stress after the ultimate tensile strength (UTS) is reached due to necking. This is because the engineering stress calculation is based on the initial cross-sectional area, which doesn't account for the reduction in area caused by necking.
The true stress-strain curve, however, continues to rise even after necking. This is because the true stress calculation accounts for the reduction in the cross-sectional area. The true stress-strain curve provides a more accurate representation of the material's actual strength and deformation behavior, particularly during significant plastic deformation.
Practical Applications of True Stress and True Strain
The true stress and true strain concepts find numerous applications in various engineering disciplines:
-
Metal Forming: Processes like forging, rolling, and extrusion involve substantial plastic deformation. Using true stress and strain enables accurate prediction of the forces and energy required for these processes, leading to optimized process parameters and improved product quality.
-
Sheet Metal Forming: Understanding the true stress-strain relationship is vital in predicting the formability of sheet metal, minimizing the risk of fracture, and ensuring the production of high-quality components.
-
Crashworthiness Analysis: In automotive design, true stress-strain curves are crucial in simulating the behavior of vehicle components during collisions. Accurate prediction of material behavior ensures improved passenger safety.
-
Finite Element Analysis (FEA): Many FEA simulations utilize true stress-strain data to model the behavior of materials under complex loading conditions. This allows for accurate stress and strain predictions in complex geometries and loading scenarios.
-
Material Characterization: The determination of true stress-strain curves is an essential part of material characterization. It provides valuable insights into the material's strength, ductility, and overall mechanical behavior.
Advanced Considerations and Limitations
While true stress and strain provide a more accurate representation of material behavior than engineering stress and strain, there are some limitations and advanced considerations to bear in mind:
-
Homogeneity Assumption: The derivation of true stress and true strain relies on the assumption of homogeneous deformation. In reality, inhomogeneous deformation is frequent, especially during necking.
-
Triaxial Stress States: The equations discussed here are primarily applicable to uniaxial stress states. In complex situations involving triaxial stresses, more advanced constitutive models are needed.
-
Rate Effects: Material behavior can be influenced by the strain rate. At very high strain rates, the true stress-strain relationship can change significantly.
-
Temperature Dependence: Material properties are often temperature-dependent. The true stress-strain curve may vary with temperature.
Conclusion
True stress and true strain offer a more accurate and comprehensive understanding of material behavior under significant loading conditions, particularly during plastic deformation. Their use is crucial in many engineering applications, from metal forming to crashworthiness analysis. While some limitations exist, understanding the formulas and their implications is crucial for engineers and materials scientists seeking to accurately predict and model material behavior and design robust and reliable structures. By mastering the concepts of true stress and true strain, engineers can optimize processes, enhance product quality, and ensure the safety and reliability of engineering systems. The continuous advancement of material modeling techniques and computational capabilities will further refine our ability to use these concepts in increasingly sophisticated applications.
Latest Posts
Latest Posts
-
Dynamic Viscosity And Kinematic Viscosity Conversion
May 10, 2025
-
How To Find The Angle Of A Sector
May 10, 2025
-
How Much Is Half Pound In Grams
May 10, 2025
-
20 Out Of 40 As A Percentage
May 10, 2025
-
How To Calculate Mass Of A Cube
May 10, 2025
Related Post
Thank you for visiting our website which covers about True Stress And True Strain Formula . We hope the information provided has been useful to you. Feel free to contact us if you have any questions or need further assistance. See you next time and don't miss to bookmark.