Cost Of Shiplap Per Square Foot
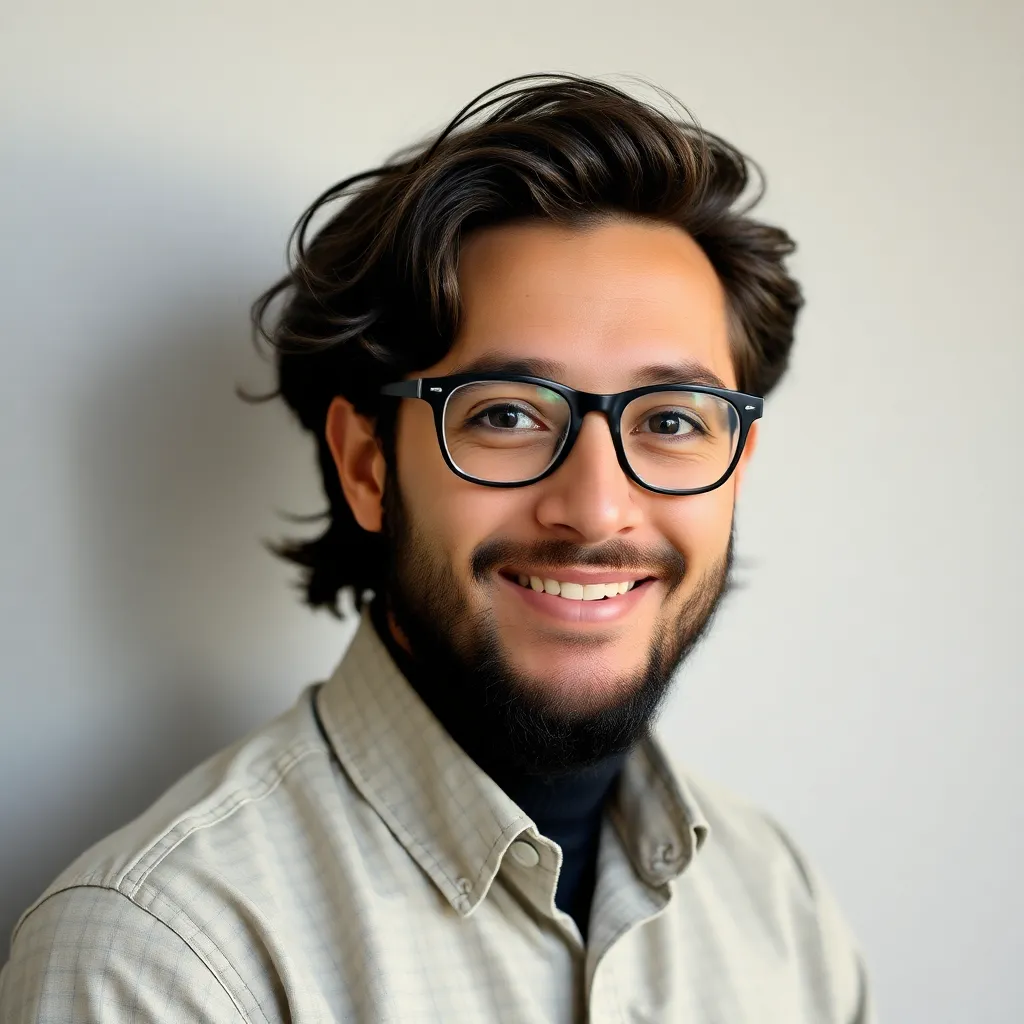
Treneri
May 14, 2025 · 6 min read
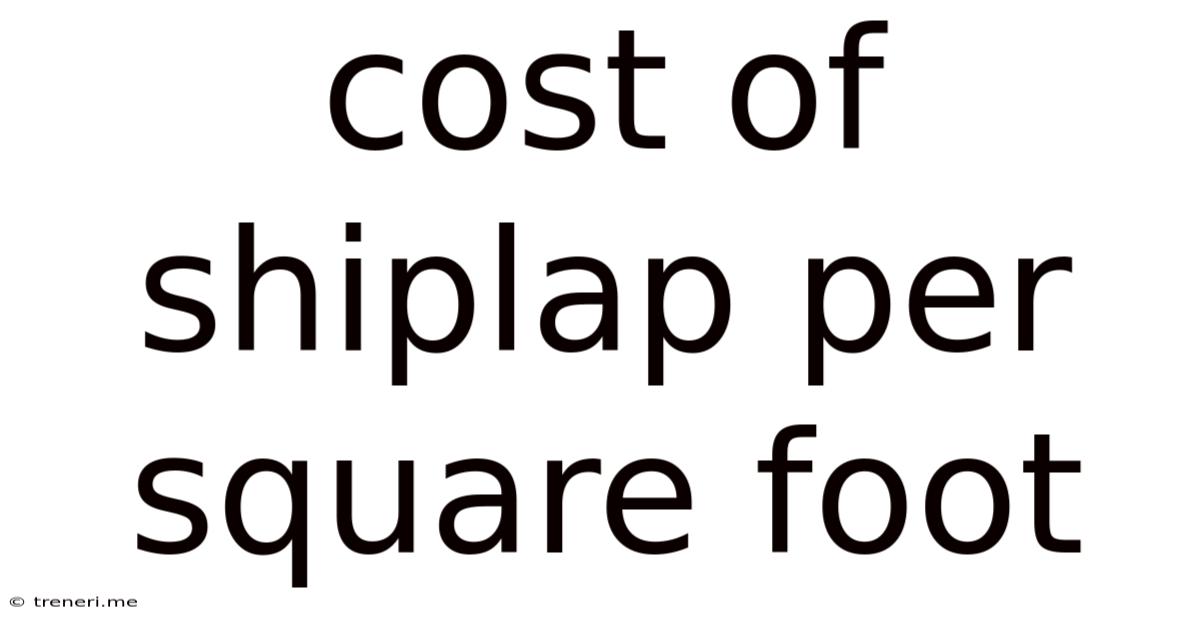
Table of Contents
Decoding the Cost of Shiplap Per Square Foot: A Comprehensive Guide
Shiplap, with its charming rustic appeal and clean lines, has become a popular choice for homeowners looking to add character and visual interest to their interiors and exteriors. But before you dive into this popular design trend, understanding the cost of shiplap per square foot is crucial for budgeting and planning your project effectively. This comprehensive guide will break down the various factors influencing the final price, helping you navigate the world of shiplap costs with confidence.
Factors Affecting Shiplap Cost Per Square Foot
The cost of shiplap per square foot isn't a fixed number. It varies significantly based on several key factors:
1. Type of Wood: A Foundation of Cost
The type of wood you choose dramatically impacts the price. Common choices include:
-
Pine: Pine shiplap is a budget-friendly option, offering a classic, light-colored aesthetic. Expect to pay less per square foot compared to hardwoods.
-
Cedar: Cedar boasts natural resistance to rot and insects, making it ideal for exterior applications. It commands a higher price point due to its durability and natural properties.
-
Fir: Fir shiplap offers a similar look and feel to pine but might be slightly more expensive due to its slightly denser grain.
-
Hardwoods (Oak, Walnut, etc.): Hardwoods significantly increase the cost per square foot. Their rich tones, durability, and exquisite grain patterns are reflected in their higher price tag. These woods offer a luxurious touch to any space.
Note: The specific species within each wood type (e.g., different types of pine) can also affect the price.
2. Grade of Wood: Quality and Cost Correlation
The grade of wood directly correlates with its cost. Higher grades mean fewer knots, imperfections, and more consistent color, leading to a premium price. Lower grades, while more affordable, might contain more knots and variations in color. Consider your desired aesthetic and tolerance for imperfections when selecting a grade.
-
Premium Grade: Expect higher prices, but also the highest quality and consistency. This is ideal for projects where a flawless finish is paramount.
-
Standard Grade: A good balance between price and quality, this grade is suitable for most projects. It may have a few minor imperfections, but they’re often minimal.
-
Rustic Grade: The most affordable option, rustic-grade shiplap embraces the natural imperfections of the wood, featuring more knots and color variations. This choice creates a more rugged and authentic look.
3. Thickness and Width of Shiplap: Dimensions and Pricing
The dimensions of the shiplap also affect the price. Thicker boards generally cost more per square foot than thinner boards. Similarly, wider boards often come at a higher price than narrower ones. Consider the visual impact you desire and balance it with your budget when choosing dimensions.
4. Pre-Finished vs. Unfinished Shiplap: Labor and Cost Implications
Choosing pre-finished shiplap will increase the upfront cost per square foot, but it saves you on labor costs associated with sanding, priming, and painting or staining. Unfinished shiplap requires additional time and materials, potentially offsetting the initial savings. Weigh the convenience and cost savings of pre-finished shiplap against the customization and potential cost savings of unfinished shiplap.
5. Installation Costs: A Significant Component of the Total Price
The cost of professional installation represents a significant portion of the overall project expense. Factors like the complexity of the project, accessibility, and the installer's hourly rate all contribute to the final cost. DIY installation can significantly reduce the overall cost, but requires time, skill, and the right tools.
6. Location and Supplier: Geographical Variations
Geographical location can play a role in shiplap pricing. Transportation costs, local market demand, and the availability of specific wood types can all affect the price. Comparing prices from multiple suppliers in your area is recommended to find the best deal.
7. Additional Costs: Beyond the Square Footage
Don't forget to factor in additional costs beyond the shiplap itself:
-
Underlayment: Depending on the surface you are installing the shiplap on, you may need underlayment for a smooth finish and to prevent moisture damage.
-
Fasteners: Nails, screws, and other fasteners are necessary for installation.
-
Primer and Paint/Stain: If you opt for unfinished shiplap, budgeting for these is crucial.
-
Caulk and Sealant: For exterior applications or areas prone to moisture, caulking is essential.
-
Waste Factor: Always account for a waste factor (typically 5-10%) when calculating the amount of shiplap you need.
Estimating the Cost of Shiplap: A Practical Approach
To estimate the cost of your shiplap project, follow these steps:
-
Measure the area: Accurately measure the area where you plan to install the shiplap.
-
Choose your materials: Select the type of wood, grade, thickness, width, and finish based on your preferences and budget.
-
Obtain price quotes: Contact multiple suppliers to get quotes for the shiplap and any additional materials.
-
Factor in labor costs: If you're hiring a professional installer, get multiple quotes and compare them.
-
Calculate the total cost: Add up the costs of materials, labor, and any other expenses.
Remember that this is an estimate, and the final cost might vary depending on unforeseen circumstances.
Real-World Cost Ranges: What to Expect
While precise pricing is difficult without specifics, here's a general range based on the factors discussed above:
-
Budget-Friendly (Pine, Standard Grade, DIY Installation): $3-$7 per square foot (including materials)
-
Mid-Range (Pine or Fir, Standard Grade, Professional Installation): $7-$15 per square foot (including materials and labor)
-
High-End (Hardwood, Premium Grade, Professional Installation): $15-$30+ per square foot (including materials and labor)
These figures are rough estimates, and prices can vary significantly depending on location and specific project details.
Maximizing Value: Smart Choices for Shiplap Projects
To get the most value for your money, consider these tips:
-
DIY Installation (if feasible): This can save you significant labor costs.
-
Shop Around: Compare prices from multiple suppliers to find the best deals.
-
Consider Sales and Discounts: Keep an eye out for seasonal sales or discounts on building materials.
-
Optimize Material Usage: Plan your layout carefully to minimize waste.
-
Prioritize Quality Over Quantity: Investing in higher-quality shiplap might require a larger initial investment, but it will likely last longer and offer a better aesthetic result.
Conclusion: A Beautiful and Informed Choice
Shiplap offers a stunning way to enhance your home's interior or exterior. By carefully considering the factors influencing its cost per square foot, planning effectively, and shopping around for the best deals, you can achieve the beautiful look you desire while staying within your budget. Remember that the total cost is more than just the price of the shiplap itself; it encompasses materials, labor, and any additional elements required for a successful project. With careful planning and a well-informed approach, you can enjoy the timeless charm of shiplap for years to come.
Latest Posts
Latest Posts
-
What Percent Of 21 Is 7
May 14, 2025
-
What Is The Gcf Of 56 And 70
May 14, 2025
-
Lcm Of 93 62 And 120
May 14, 2025
-
Cual Es La Raiz De 8
May 14, 2025
-
How Many Ml Are In 20 Oz
May 14, 2025
Related Post
Thank you for visiting our website which covers about Cost Of Shiplap Per Square Foot . We hope the information provided has been useful to you. Feel free to contact us if you have any questions or need further assistance. See you next time and don't miss to bookmark.